Bericht über die ZVO-Oberflächentage 2014 in Neuss
Der Vorteil für die Fachleute eines Bereichs, der als klassische Schlüsseltechnologie bezeichnete werden kann, liegt unter anderem darin, dass die Verfahren immer gebraucht und eigentlich überall eingesetzt werden können. Allerdings muss eine solche Position, wie sie auch die Oberflächentechnik innehat, durch kontinuierliche Anpassungen an die Markterfordernisse und die Weiterentwicklung der Verfahren stets neu behauptet werden. Die ZVO-Oberflächentage sind die unentbehrliche Plattform, um sich detailliert mit diesen Punkten auseinanderzusetzen. In 66 Einzelvorträgen wurde vom 17. bis 19. September in Neuss die gesamte Palette von der Reinigung und Vorbehandlung über die Oberflächenbehandlung mit chemischen, galvanischen oder thermisch-mechanischen Verfahren bis hin zu den unterschiedlichen Einsatzmöglichkeiten mit deren Vor- und Nachteilen erläutert. Dazu kommen traditionell neben den erfahrenen Fachleuten auch die Nachwuchskräfte zu Wort.
Feierliche Eröffnung
In einem gut gefüllten Festsaal eröffnete der ZVO-Vorsitzende Walter Zeschky die ZVO-Oberflächentage mit der Begrüßung der Ehrenmitglieder. Er zeigte sich erfreut, dass wiederum eine Reihe junger Kollegen aus den Schulen und Hochschulen Deutschlands die Gelegenheit wahrgenommen hatte, sich mit den Fachleuten und deren Arbeitsgebieten vertraut zu machen. Für den Nachwuchs stand eine Tour zur Anke GmbH & Co. KG in Essen und der BIA Kunststoff- und Galvanotechnik GmbH & Co. KG in Solingen auf dem Programm.
Für den Festvortrag konnte der ZVO den Motivationstrainer und zehnfachen Teilnehmer am legendären Ironman-Wettbewerb Slatco Sterzenbach gewinnen. Wie Sterzenbach einführend betonte, gehört das Reden vor Publikum zu den Tätigkeiten, die ihm am meisten Spaß machen – und damit war er bereits mitten im Thema. Denn nur mit Tätigkeiten, die einem Spaß machen, ist nach seiner Meinung auch eine lange und erfolgreiche berufliche Beschäftigung möglich. Darüber hinaus erfordern erfolgreiche Tätigkeiten auch stets ein erhebliches Maß an Disziplin und Willensstärke, sich den anstehenden Aufgaben gleich zu stellen und nicht auf die lange Bank zu verschieben. Sein Motto: Wir können nur dann ein perfektes Leben bekommen, wenn wir den Tag perfekt gestalten können. Krank ist es seiner Meinung nach, eine Tätigkeit auszuüben, die einem keinen Spaß macht.
Um dieses Ziel zu erreichen, spielt nach seiner Erfahrung die Fitness eines jeden Einzelnen eine große Rolle, wobei die Vorstellung von Sterzenbach über die Gewichtung und Erzielung der Fitness sicher stark von seinem persönlichen Wunsch nach sportlicher Betätigung – der Teilnahme am Ironman-Wettbewerb – geprägt sind. Weitere wichtige Punkte für ein erfülltes Leben ergeben sich nach seiner Meinung durch Visionen, die jeder einzelne haben und verfolgen sollte, das Setzen von Zielen, die es planmäßig anzustreben gilt. Weiter ist dafür eine Strategie zu erarbeiten, die durchaus von Zeit zu Zeit überprüft und angepasst werden muss. Dem folgt die Forderung nach Training – körperlich oder geistig – sowie die Schaffung eines Bewusstseins für die Fülle an unbewussten Gedanken, die unser Leben bestimmen. Damit sollte es möglich sein, seine Gedanken viel genauer darauf zu richten, welche Handlungen uns ein erfülltes Leben verschaffen können und zeitraubende, aber sinnlose Aktionen zu vermeiden.
Der zweite Teil des Festabends war der Verleihung von Preisen gewidmet, die der DGO-Vorsitzende Rainer Venz moderierte. Der DGO-Förderpreis wurde durch Prof. Dr. Wolfgang Paatsch an Loreen Wermuth verliehen. Die Preisträgerin hat in Zusammenarbeit zwischen der TU Dresden und der Airbus DS GmbH in München eine superhydrophobe Titanoberfläche zur Vermeidung von Eisbildung entwickelt. Derartige Oberflächen finden vor allem in der Luft- und Raumfahrt Anwendung. Darüber hinaus sind sie aber auch zunehmend bei Windkraftanlagen von Interesse. Eine solche superhydrophobe Oberfläche verzögert zum einen die Eisbildung und reduziert zum anderen den Energieeinsatz für das Enteisen von Flächen. Insbesondere die Flügelkanten bei Flugzeugen müssen eisfrei sein, um die Strömungseigenschaften der Tragflächen zu gewährleisten und so Unfälle zu vermeiden.
Der zweite verliehene Preis war der Heinz-Leuze-Preis. Für das Preiskuratorium erläuterte Prof. Dr. Waldfried Plieth die Wahl des diesjährigen Preisträgers, Prof. Dr. Uwe Landau. Er erhielt den Preis, bestehend aus einer Medaille und einem Preisgeld, für seinen Aufsatz über die antimikrobiell wirkende AgXX-Beschichtung. Diese wird seit einigen Jahren kommerziell angeboten und kann vor allem in der Medizintechnik, aber auch für die Wasseraufbereitung in der Raumfahrt einen beachtlichen Erfolg und ein hohes Interesse aufweisen.
Ausklang fand der Begrüßungsabend mit Büfett und Unterhaltung, unter anderem mit einer kurzweiligen Bauchrednernummer. Hier konnten alte Verbindungen aufgefrischt und neue geknüpft werden.
Fachvorträge
Rainer Venz eröffnete den ersten Tagungstag der Fachvorträge mit einem Rückblick auf deutliche Veränderungen der Galvanotechnik in den letzten 20 Jahren. So sind Stoffe wie Cyanid, Cadmium oder Chrom(VI) verschwunden oder zumindest wurde der Einsatz drastisch reduziert. Auch derzeit geht dieser Umbruch weiter, indem zunehmend neue Verfahren bei der Beschichtung von Kunststoffen oder der Herstellung von Chromschichten entwickelt und eingesetzt werden. Hier kommt den Entscheidungsträgern eine wichtige Verantwortung zu, da Fehlentscheidungen langfristig sind und drastische Folgen für die Oberflächentechnikbranche haben können. Dazu wurden und werden Aktivitäten gebündelt, wie in den letzten Jahren deutlich am Wandel der Schwerpunkte von DGO und ZVO zu erkennen war.
Eröffnungsvortrag – Additive Bauteilfertiung
Im ersten Fachvortrag gab Kolja Andreas einen Einblick in die additive Bauteilfertigung im Kontext der Oberflächentechnik. Der Lehrstuhl des Referenten deckt bei seiner Betrachtung die gesamte Prozesskette von der Werkstoffcharakterisierung bis zur Qualitätssicherung ab.
Bei der Auswahl von Fertigungsverfahren werden Anforderungen wie Machbarkeit, Marktanforderungen, Standort oder Technikverfügbarkeit bewertet. Der Produktionsstandort Deutschland ist dabei stark vom heute üblichen Qualitätsmanagement, der Prozessautomatisierung oder der Einführungsdauer für Prozesse geprägt. Vor allem der hohe Flexibilitätsfaktor führt dabei zwangsläufig zur additiven Fertigungstechnik. Wichtige Faktoren zur Bewertung der Verfahren sind beispielsweise die erreichbare Zugfestigkeit und Produktionsgeschwindigkeit. Entsprechend der Form der Ausgangsstoffe wird beispielsweise nach Fluid, Pulver, Strang oder Folie unterschieden, wobei zur Energiezufuhr stets Laser zum Einsatz kommen. Das Bauteil selbst wird schichtweise und ohne den bisher üblichen Werkzeugeinsatz erzeugt. Bereits daraus ist ersichtlich, dass auch die Stückzahl 1 zu den selben Kosten wie hohe Stückzahlen realisierbar ist.
Im Rahmen eines Ringversuchs wurden unter anderem alle relevanten Kenngrößen wie Festigkeit, Aufwand für Nacharbeit oder Oberflächengüten eines Probekörpers aus Edelstahl bewertet. Dabei zeigten die Körper je nach Hersteller Unterschiede in der Oberflächenrauheit. Ein erheblicher Einfluss auf die Qualität des Teils ergab sich bei der Nachbearbeitung durch eine Wärmebehandlung. Es zeigte sich auch, dass ein hoher Anteil an Gefügedefekten die Nachbearbeitung durch Vermindern der Oberflächenrauheit wirkungslos machen kann. Poren führen ebenso wie Rauheiten zu Spannungsspitzen mit Nachteilen auf die Festigkeit. Die Ergebnisse belegen deutlich, dass eine Nachbearbeitung die Qualität des Bauteils erheblich verbessert.
Weiteres Beispiel ist ein Massivumformwerkzeug, das durch Laserauftragschweißen erzeugt wird. Auch hier liegt oftmals die Bauteillosgröße bei 1, woraus sich ein besonderes Interesse an der additiven Fertigung ableiten lässt. Für die Vorversuche wurden beispielsweise die Arbeitsgeschwindigkeit und die eingesetzte Laserleistung am Parameter Oberflächenrauheit bewertet, wobei die Geschwindigkeit gegenüber der Leistung einen geringeren Einfluss besitzt. Entscheidend ist ein vollständiges Aufschmelzen der Pulver. Zwingend notwendig ist auch hier eine Nachbearbeitung.
In einem weiteren komplexen Versuchsbauteil eines Lüftergehäuses aus Edelstahl wurde der Einfluss des Oberflächenstrahlens nach Fertigstellen des Teils untersucht. Strahlen entfernt die hier vorhandene Oxidschicht und reduziert die Oberflächenrauheit. Beides verbessert die Qualität des Teils deutlich.
Anwendung findet das additive Fertigen für die Produktionsbereiche Rapid Prototyping und Rapid Manufactering, wogegen für das Rapid Tooling noch erhebliche Verbesserungen notwendig sind. Dabei machen sich vor allem Oberflächenbearbeitungen stark bemerkbar.
Impulsvorträge
Unternehmen hatten im Rahmen von Impulsvorträgen, moderiert von Christoph Matheis, die Möglichkeit, neue Produkte und Verfahren vorzustellen. Dabei wurde den Rednern ein Zeitlimit von fünf Minuten gesetzt.
Dr. Ingo Klüppel stellte das neue Delta Prozinc der Dörken MKS als Prozess für die Herstellung von Zinkbeschichtung mit Vorbehandlung, Beschichtung und Nachbehandlung vor. Dabei spielt vor allem der weltweit einheitliche Prozessablauf mit hohen Anforderungen an Schutzwirkungen und Umweltfreundlichkeit eine große Rolle. Auf Stoffe wie Chrom(VI), Nickel, Kobalt und Komplexbildner wird vollständig verzichtet. In Kombination mit einem neu entwickelten Dickschichtpassivierungssystem werden beim Korrosionsschutz 840 Stunden ohne Weiß- oder Rotrost erreicht.
Mit Strata präsentierte Dr. Thorsten Kühler den neuen dekorativen Korrosionsschutz ohne Chrom(VI) der Coventya GmbH. Hierbei wird der Forderungen nach Einchränkungen der bisherigen Verfahren aufgrund von REACh Rechnung getragen. Bei Strata wird nach den bisherigen Glanzkupfer- und Nickelschichten eine mikrorissige Nickelschicht, eine Nickellegierungs- und eine Chrom(III)schicht abgeschieden. Das System ist auch bei komplizierten Bauteilgeometrien und mit höchsten Anforderungen an Glanz und Korrosionsbeständigkeit herstellbar.
Das Online-Sensorsystem der SensAction AG, vorgestellt von Michael Münch, eignet sich beispielsweise zur Konzentrationsmessung von Reinigungsmedien. Dafür stehen zwei Systeme zur Verfügung: eine Bauart für die vollständig automatisierte Messung in einem Rohrsystem und eine für die manuelle Messung. Gemessen wird die Konzentration des Reinigers, für den das Messgerät kalibriert wird und somit auch die Nachdosierung gesteuert werden kann. Bei Mehrkomponentensystemen wird die Menge des Builders erfasst. Besonders einfach ist die Anwendung dadurch, dass der Anbieter für die meisten Reinigersysteme eine Anwendersoftware zur Steuerung der Geräte verfügbar hat.
Sauberkeit als Basis für die Beschichtungsqualität
Auf großes Interesse stieß auch in diesem Jahr das in die Veranstaltung integrierte Forum Bauteilreinigung des Fachverbands industrielle Teilereinigung e. V. (FiT). Wesentliche Voraussetzung für die Qualität, Langzeitstabilität und Optik einer Beschichtung ist unabhängig von der Anwendung die bedarfsgerechte Sauberkeit der Oberfläche. Antworten auf die Frage, wie sich diese nicht nur prozesssicher, sondern auch wirtschaftlich und nachhaltig erzielen lässt, bot das Forum Bauteilreinigung des Fachverbands industrielle Teilereinigung am 18. September in neun Vorträgen.
Mit den Grundlagen der industriellen Teilereinigung beschäftigte sich der Vortrag von Karl-Heinz Wießner, Max F. Keller GmbH, deutsche Vertretung der Borer Chemie AG. Er zeigte dabei auf, dass optimal abgestimmte Prozessparameter im gesamten Fertigungsprozess eine Grundvoraussetzung sind, um das erforderliche Reinigungsergebnis wirtschaftlich zu erreichen. Die unterschiedlichen Bestandteile wässriger Reinigungschemie wurden in diesem Referat ebenso thematisiert wie der Anlagenbau und Verfahren zur Überwachung der Badqualität.
Mit Lösungen für eine qualitätssichernde Prozessführung beschäftigte sich der Vortrag von André Lohse, SITA Messtechnik GmbH. Er stellt dabei Messmethoden zur kontinuierlichen Ermittlung der Tensidkonzentration im Reinigungsbad, der Überwachung der Verschmutzung durch Öle und Fette in den Reinigungs- und Spülbädern sowie zur Kontrolle der erzielten filmischen Sauberkeit vor.
Den Anwendungsgebieten salzfreier Reiniger, sogenannter Neutralreiniger, widmete sich der Vortrag von Jens Emmrich, Projektmanager industrielle Reinigung bei der SurTec Deutschland GmbH. Er zeigte dabei die Vorteile dieser Reiniger auf – auch unter dem Aspekt 1- und 2-Komponentensysteme sowie der Anpassung an verschiedene Reinigungsverfahren wie Tauch-, Spritz- und Ultraschallreinigung. Darüber hinaus stand der temporäre Korrosionsschutz im Fokus, der mit diesen Reinigungssystemen erreicht werden kann.
Unter dem Titel Wir strahlen anders stellte Olav G. Schulz, Geschäftsführer der SLCR Lasertechnik GmbH, die Möglichkeiten, Potenziale und Grenzen der Laserstrahltechnik in der industriellen Teilereinigung vor. Verdeutlicht wurden dabei die verschiedenen Wirkprinzipien des Verfahrens und die erzielbaren Effekte beim Reinigen, Aufrauen und Aktivieren. Der Einsatz der Lasertechnik hat seine Vorteile insbesondere in der hohen Flexiblität.
Ein weiterer Punkt war die Automatisierung der Reinigung. Mit der Optimierung der Reinigung auf Basis der Prozesskettenanalyse beschäftigte sich der Vortrag von Reiner Grün, Vorsitzender des FiT. Er beleuchtete die Kriterien für die Auswahl der Reinigungschemie, Anlagen-, Verfahrens- und Aufbereitungstechnik unter dem Gesichtspunkt Verschmutzung und erforderliche Sauberkeit für den nachfolgenden Fertigungsschritt, wie beispielsweise mechanische Bearbeitung, Wärmebehandlung oder Montage.
Die Einflussgröße Restmagnetismus: Analyse von aktuellen Anforderungen und Entmagnetisierverfahren thematisierte Marek Rohner, Head of Technology bei der Maurer Magnetic AG. Aufgezeigt wurde, wie Grenzwerte für Restmagnetismus bei verschiedenen Anwendungen festgelegt werden. Eine Beschreibung der vor Reinigungsanlagen eingesetzten Wechselfeld-Entmagnetisiersysteme verdeutlichte, wie sich die Verfahren effektiver einsetzen lassen.
Der Online-Konzentrationsmessung des Reinigerbestandteils Builder mittels akustischer Wellenleiter widmete sich das Referat von Michael Münch, Geschäftsführer der SensAction AG. Er informierte die Teilnehmer über den Aufbau und die Einbaumöglichkeiten des Messsystems bei Reinigungsanlagen sowie über die Kalibrierung, die auf Basis des spezifischen Reinigers sowie der Prozessparameter Temperatur und Dichte erfolgt. Die Selektivität der Messung lässt sich auf Öle, Fette und Reste von Kühlschmiermitteln auslegen.
Dr. Rolf Schreinert von der EnviroFalk GmbH ging in seinem Vortrag auf die Aufbereitung der verschiedenen Medien wässriger Reinigungsprozesse ein. Beleuchtet wurden dabei die Möglichkeiten und Einsatzgebiete der Ultrafiltration und Umkehrosmose sowie die Herstellung von VE-Wasser.
Von Dieter Ortner, Vertriebsleitung Technik International bei der Pero AG, erfuhren die Teilnehmer anhand eines Anwendungsbeispiels, wie sich Klebeflächen von elektrischen Leistungsmodulen für die Elektromobilität mit modifiziertem Alkohol reinigen lassen. Dabei sind definierte Vorgaben sowohl hinsichtlich partikulären als auch filmischen Restschmutzes einzuhalten. Ortner stellte in seinem Vortrag die verschiedenen Schritte der Medien- und Verfahrensauswahl vor.
Die Teilnehmer des Forums Bauteilreinigung waren sowohl mit dem breit gefächerten Vortragsangebot als auch der Qualität der Referate sehr zufrieden und konnten zahlreiche Anregungen mit in ihre Unternehmen nehmen.D. Schulz
Funktioneller Korrosionsschutz
Insbesondere Teile aus Eisenwerkstoffen müssen durch Beschichtungen gegen Korrosion geschützt werden. Dafür kommen in erster Linie Schichten aus oder mit Zink in Betracht, da der dabei wirkende kathodische Korrosionsschutz das Grundmaterial sehr effizient schützt.
Zink-Eisen-Schichten
Eröffnet wurde die Vortragssitzung von Christoph Hoge, Coventya GmbH, mit einem Beitrag zu galvanisch abgeschiedenen Zink-Eisen-Legierungen mit höheren Eisengehalten. Diese Schichten werden zunehmend interessant, seit bekannt ist, dass Nickel aufgrund der REACh-Verordnung unter verstärkte Beobachtung gerät. Zinklegierungsschichten haben aufgrund einer höheren Härte und eines etwas günstigeren Potenzialwertes, was eine höheren Korrosionsbeständigkeit bewirkt, die bisher üblichen reinen Zinkschichten aus vielen Anwendungen verdrängt. Aussichtsreiche Alternativen zu Zink-Nickel sind Zink-Eisen-Legierungen mit etwa 15 % Eisen. Der Vortragende stellte deren Verhalten unter mechanischer und korrosiver Belastung vor.
Schwarze Zinklamellenbeschichtung
Eine weitere wichtige Beschichtung griff Andreas Fink, Atotech Deutschland GmbH, mit der Zinklamellenbeschichtung auf. Hierbei werden in eine Matrix Zinklamellen eingebettet, wodurch der kathodische Korrosionsschutz erzeugt wird. Die Matrix liefert dabei einen zusätzlichen Korrosionsschutz, da es sich in der Regel um ein Polymer mit entsprechend guter Beständigkeit handelt. Herstellungsbedingt wird darüber hinaus Wasserstoffversprödung vermieden. Für viele Anwendungen sind schwarze Schichten gefragt, die in der Regel durch Auftrag einer schwarzen Decklackierung erzielt werden.
Eine neue Beschichtung arbeitet mit einer schwarzen Grundbeschichtung, wodurch einerseits die Zahl an Einzelbeschichtungen zum Aufbau der Gesamtschicht reduziert und andererseits die Farbintensität erhöht wird. Besondere Herausforderungen ergeben sich nach den Ausführungen des Vortragenden bei Schrauben mit Innenangriff, bei denen oftmals störende Anhäufungen festzustellen sind. Die neue Beschichtungssysteme verbessern die Situation aufgrund der geringeren Anzahl an Einzelschritten zur Herstellung der Beschichtung. Sie erfüllt nach ersten Prüfungen die hohen Anforderungen der Vorschrift VW TL 180.
Optimierung bei Zinklamellensystemen
Einen weiteren Aspekt bei Zinklamellensystemen erläuterte Michael Krumm, Coventya GmbH. Insbesondere bei den Gewinden von Schrauben tritt bei Zinklamellensystemen je nach den Eigenschaften des Systems und der Substrate des öfteren eine ungleichmäßige Beschichtung auf. Die Vertiefungen des Gewindes enthalten eine zu hohe und die äußeren Flanken eine zu geringe Schichtdicke, wodurch der Korrosionsschutz schlechter und vor allem ungleichmäßig ausfällt.
Durch eine Modifikation des Fließverhaltens der Beschichtungslösung kann die Verteilung der Schicht deutlich verbessert werden. Dabei wird berücksichtigt, dass die Verteilung der Zinklamellen in der Beschichtungslösung ebenfalls gleichmäßig sein muss.
Oberflächen für die Elektronikindustrie
Silber-Palladium für Kontakte
Friedrich Talgner, Umicore Galvanotechnik GmbH, stellte einen neuen, cyanidfreien Elektrolyten zur Abscheidung von Silber-Palladium für elektronische Kontakte vor. Motivation zur Entwicklung der neuen Legierung ist der hohe Goldpreis, aufgrund dessen bisher vor allem Palladium und Palladiumlegierungen in Kombinationsschichten mit Gold zum Einsatz kamen. Reines Silber ist durch eine geringe Härte und die Bildung einer störenden Anlaufschicht nur bedingt für den Einsatz in der Elektrotechnik geeignet.
Durch Legieren lassen sich die Nachteile beseitigen. Bereits bei Palladiumgehalten von etwa 10 % kann die Härte der Schichten von etwa 70 HV für reines Silber auf etwa 250 HV für die Legierung gesteigert werden. Eine Alterung führt zu Härten von deutlich über 300 HV. Zugleich erhöht sich die Abriebbeständigkeit deutlich. Zudem bleibt die Zusammensetzung der Schichten auch über einen sehr breiten Stromdichtebereich von etwa 1 A/dm2 bis 14 A/dm2 nahezu unverändert, wodurch sich der Elektrolyt für den Einsatz in der Bandbeschichtung eignet.
Bondoberfläche
Eine weitere zukunftsträchtige Beschichtung für die Elektrotechnik ist das Nanoschichtsystem aus Nickel, Palladium und Gold, das Markus Klingenberg, Inovan GmbH & Co. KG, vorstellte. Hierbei wird mit außerordentlich dünnen Edelmetallschichten von etwa 50 nm bis 250 nm Palladium und etwa 5 nm Gold gearbeitet. Diese geringen Dicken verhelfen der Beschichtung zu hoher Wirtschaftlichkeit, da die Bondverbindungen auch nach einer Lagerung von beschichteten Teilen sicher durchgeführt werden können. Genauere Untersuchungen zeigen, dass die Bondverbindung zwischen Aluminiumdraht und Palladiumschicht erfolgt, die Goldschicht hier also vorrangig für den notwendigen Kontakt sorgt. Durch Weiterentwicklung soll die Anwendung auch für das Löten optimiert werden.
Nickelfreie Bondoberflächen
Im dritten Beitrag des Blocks erläuterte Andreas Groß die Anwendung und Praxiseignung von Edelmetalloberflächen ohne Nickel für das Bonden auf Leiterplatten. Auch hier sind die Aktivitäten in Zusammenhang mit REACh die treibenden Kräfte der Entwicklungen zum Ersatz von Nickel. Zur Herstellung von Bondoberflächen nach einer neuen Technologie werden die Kupferleiterbahnen mit Kombinationsschichten aus Palladium und Gold beschichtet. Die Bondverbindungen werden mit Aluminium- und Golddraht hergestellt, wobei darüber hinaus die Schichten auch für Lötverbindungen geeignet sein sollten. Aufgrund der großen Stückzahlen derartiger Verbindungen, spielt die Reduzierung der Edelmetallschichtdicken eine wichtige Rolle. Der Vortragende zeigte an einer großen Zahl unterschiedlicher Bond- und Lötversuche die Eignungen der verschiedenen Schichtvarianten.
Anlagentechnik
Zerstörung von Komplexverbindungen
Im Bereich der Abwasserbehandlung stellen vor allem neue Komplexverbindungen eine Herausforderung dar. Diese kommen unter anderem durch Weiterentwicklungen neuer Elektrolytvarianten und Behandlungslösungen zunehmend zur Anwendung. Zudem muss aus Gründen des Umweltschutzes sowohl dem Einsatz von Behandlungschemikalien als auch dem Abbau von chemischen Verbindung eine erhöhte Aufmerksamkeit geschenkt werden. Anke Heisel, HeiTec, stellte eine Verfahrenstechnik zur Zerstörung von Komplexverbindungen mit Hilfe von Druck vor. Der Druck wird hierfür durch eine Temperaturerhöhung bei konstantem Volumen oder durch Druckbeaufschlagung von Außen erzeugt. Die Resultate stellte die Vortragende am Beispiel von Komplexverbindungen mit Nickel und mit Silber vor.
Effiziente Gleichrichter
In der Galvanotechnik wird beim Betrieb von Gleichrichtern ein erheblicher Teil der zugeführten Energie als Wärme abgegeben. Thomas Köhl-Skarval stellte in seinem Beitrag Lösungsmöglichkeiten vor, den Energieeinsatz für Gleichrichter in Galvanikbetrieben zu reduzieren. Dazu eignen sich einerseits die Gleichrichter mit Schaltnetztechnologie, die einen hohen Wirkungsgrad bei gleichzeitig geringem Platzbedarf aufweisen. Zum anderen kann Energie durch eine geringe Leitungslänge zwischen Gleichrichter und Abscheideelektrolyten eingespart werden. Schließlich bieten geeignete Wasserkühlungen die Möglichkeit, Wärme an anderen Stellen im Prozess zu nutzen und so die Gesamteffizienz einer Anlage zu steigern. Dazu zeigte der Vortragende ein Reihe von Kombinationsmöglichkeiten, wie sie in Galvanikbetrieben realisiert wurden.
Kühlanlagen
Ebenfalls um die Einsparung von Energie beziehungsweise deren optimalem Einsatz ging es im dritten Beitrag von Thomas Imenkämper, der sich mit Energiespartechniken bei Kühlanlagen befasste. Anhand der Kühlungsvarianten wie Brunnenkühlung, Freikühlung, Kühlturmanlagen oder Kältemaschinen zeigte er auf, mit welchen Eingangsbedingungen die einzelnen Verfahren betrieben werden können und wie sie aufgebaut sind. Hierbei wird beispielsweise von unterschiedlichen Temperaturen des vorliegenden Kühlwassers ausgegangen. Je nach Betriebsausstattung und Einsatzfall lassen sich mit den Anlagen erhebliche Energiemengen einsparen. Zugleich führt das optimale Temperaturmanagement zu einer hohen Prozessstabilität.
Junge Kollegen
Die von Prof. Dr. Wolfgang Paatsch moderierte Reihe der Jungen Kollegen bietet Absolventen von Schulen und Hochschulen sowie jungen Wissenschaftlern die Möglichkeit, ihre Untersuchungen vorzustellen und damit für ihre Arbeit zu werben. Zugleich zeigen die Arbeiten aber auch potenzielle Entwicklungstrends auf, die sowohl wichtige Aspekte des Umweltschutzes, der Materialeinsparung oder der Eigenschaftsverbesserung beinhalten. Eröffnet wurde die Vortragsreihe von der Preisträgerin des Nachwuchsförderpreises der DGO.
Superhydrophobe Titanoberflächen
Wie Loreen Wermuth einleitend darlegte, stellt das Vereisen von Oberflächen bei Flugzeugen nach wie vor ein erhebliches Problem dar. Darin begründet sich auch das hohe Interesse der Luft- und Raumfahrt an Oberflächen, die die Eisbildung verhindern, reduzieren oder für ein schnelles Enteisen geeignet sind. Für die Untersuchungen wurde eine Titanlegierung gewählt. Diese müssen eine lange Beständigkeitsdauer aufweisen und zugleich die aerodynamischen Bedingungen erfüllen. Durch das Anodisieren in einem fluoridhaltigen Elektrolyten entstehen Nanoröhren mit Durchmessern von etwa 50 nm. Das Anodisieren selbst wird bei Spannungen von etwa 20 V vorgenommen. Zur Erzeugung einer superhydrophoben Oberfläche wird zusätzlich eine Schicht zum Beispiel auf Perfluorbasis aufgetragen, ohne die feine Mikrostruktur zuzusetzen. Die nur wenige Nanometer dicke Schicht entsteht also in den Röhreninnenwänden und Außenflächen. In diesem Fall bleibt der superhydrophobe Effekt auch bei tiefen Temperaturen erhalten.
In den Enteisungsversuchen zeigte es sich, dass die Anodisierspannung keinen messbaren Einfluss hat und die Art der Zusatzbeschichtung kaum zu Unterschieden führt. Die selben Ergebnisse ergeben sich auch bei Verwendung von Titanfolien, die auf CFK-Grundkörper aufgebracht werden. Damit ist es möglich, ein Bauteil herzustellen, bei dem zwischen Titanfolie und Grundkörper eine elektrische Heizung integriert wird. Bei den durchgeführten Versuchen wurde für das Enteisen eine sehr geringe erforderliche Heizenergie gemessen. Auf Basis der neu entwickelten Oberfläche lassen sich auch für andere Industriebereiche, beispielsweise die Rotoren von Windkraftanlagen, Anwendungen erkennen. Ausschlaggebend sind die einfache Herstellungsmethode und deren hohe Funktionssicherheit. Ein Nachteil ist bisher, dass unter Einwirkung von Fett der superhydrophobe Effekt verloren geht.
Bewertung einer elektrochemischen Dispersionsabscheidung
Justus Köhler von der Hochschule Aalen stellte in seinem Beitrag Überlegungen zur Modellbildung der Dispersionsabscheidung und deren mögliche Verwendung vor. Die Modellbildung ist unter anderem erforderlich, um beispielsweise eine Beeinflussung der Schichteigenschaften durch Dispersionsabscheidung steuern zu können. Entsprechende Modelle wurden erstmals ab etwa 1972 entwickelt. Diese berücksichtigen unter anderem die Adsorption oder die Hydrodynamik, aber auch die Bildung von Doppelschichten an der Oberfläche der verwendeten Partikel, die in die Doppelschicht der zu beschichtenden Oberfläche integriert wird. In einem weiteren Schritt kommen auch die wirkenden Kräfte zur Geltung, die über die Zeitdauer der Anlagerung an der Oberfläche entscheidet. Damit werden beispielsweise Gründe für die Frage geliefert, weshalb nicht alle Teile mit der selben Qualität in eine wachsende Schicht eingebaut werden.
Am Einbau von Siliziumcarbid in Nickel zeigte der Vortragende am Mechanismus der Partikeladsorption, dass die Abscheidegeschwindigkeit in Zusammenhang mit der Anlieferungsgeschwindigkeit die Einbaurate bestimmt. Dazu fügte er dem Elektrolyten als zweite Partikelsorte Siliziumoxid in zwei Größen (2 µm und 8 µm) zu. In Abhängigkeit von Stromdichte und Strömung ergaben sich unterschiedliche Einbauraten. Insbesondere wirkte sich aber der Anteil der zweiten Partikelsorte auf die Einbaurate des Siliziumcarbids aus. Ab einer Zusatzmenge von etwa 10 g/l Siliziumoxid steigt die Einbaurate für Siliziumcarbid erkennbar an. Aus den Messergebnissen leitete der Vortragende unter Verwendung von vorhandenen Modellen drei mögliche Wirkungsmechanismen ab.
Abscheidungen mit Bismut
Den Einsatz von Magnetfeldern bei der Abscheidung von Bismut und Bismut-Kupfer untersuchte Franziska Karnbach. Mit dem Verfahren sollte es möglich werden, Gradientenschichten für Sensoren herzustellen. Dafür wurden zunächst Untersuchungen mit unterschiedlichen Ionenarten (paramagetischen und diamagnetischen) zur Keimbildung durchgeführt. Die Ergebnisse deuten auf einen Einfluss der Konvektion hin.
Auf Basis dieser Erkenntnis konnten die Unterschiede bei der Abscheidung von Bismut und Bismut-Kupfer erklärt und gesteuert werden. Mit der verwendeten Technologie lässt sich bei der Abscheidung aus einem Elektrolyten mit Bismut und Kupfer durch Veränderung der Magnetfelder der Anteil an Bismut in der Schicht verändern.
Analyse von Chrom(III)passivierungen
Insbesondere für den Einsatz für sicherheitsrelevante Bauteile für die Luft- und Raumfahrt ist es erforderlich, die Wirkungsweise von Verfahren zur Einschätzung von eventuellen Risiken sehr genau zu kennen. Jennifer Honselmann untersuchte dazu die Passivierung von Aluminium mit einem System auf Basis von Chrom(III)verbindungen. Als Legierung wurde die kupferhaltige EN-AW2024 ausgewählt. An der Schichtbildung sind bei der verwendeten Passivierung (SurTec 650 chromitAL TCP) neben Chrom(III) auch Zirkon(IV) und Fluorid beteiligt. Als erster Schritt einer Passivierung wird eine Beizbehandlung durchgeführt, nach der Kupferanreicherungen an der Oberfläche festzustellen sind. Diese kupferhaltigen Phasen wirken in der Anfangsphase des Passivierungsvorganges als keimbildend, indem dort zuerst Oxide mit Chrom und Zirkonium gebildet werden. Etwa 10 Sekunden nach Beginn der Passivierung ist die Aluminiumoberfläche weitgehend mit Oxiden bedeckt. Interessant ist die Tatsache, dass das vorhandene Chrom(III) anfangs als metallisches Chrom und erst im weiteren Verlauf der Passivierung als Chromoxid abgeschieden wird. Auf den Oberflächenbereichen ohne Kupferanreicherungen entsteht ein Mischoxid mit Aluminiumfluorid. Darüber wurde festgestellt, dass sich zwischen diesem Oxid und den Chrom-Zirkon-Mischoxiden auf den Kupferphasen Risse bilden.
Eisenlegierungsschichten
Eine Arbeit von Roy Morgenstern und Kollegen befasst sich mit korrosions- und verschleißbeständigen Eisenlegierungsschichten und deren Verwendung. Eisenbeschichtungen wurden bisher vor allem zum Reparieren von Oberflächen, in der Galvanoformung sowie als Verschleißschutz eingesetzt. Insbesondere Legierungsschichten bieten darüber hinaus aber auch die Möglichkeiten, Oberflächen mit weiteren Eigenschaften auszustatten, wie sie teilweise auch rostfreie Stähle aufweisen. Damit bieten die Schichten ein Potenzial zur Einsparung von Kosten. Untersucht wurden Eisenlegierungen mit Chrom und Nickel sowie Molybdän und Nickel, mit denen hohe Korrosions- und Verschleißbeständigkeiten erzielbar sind.
Dispersionsschichten
Wie Mathias Weiser in seinem Vortrag erläuterte, ist die Elektrotechnik vor allem im niederen Spannungsbereich auf die Verwendung von Goldschichten angewiesen. Durch Legieren der Goldschichten mit Nickel oder Kobalt kann die Härte von etwa 80 HV für reines Gold auf etwa 200 HV für die Legierungen gesteigert werden. Eine weitere Verbesserung der Verschleißbeständigkeit sollte durch die Herstellung von Dispersionsschichten mit Gold möglich sein. Dazu wurden Aluminiumoxid-
Nanopartikel mit Durchmessern zwischen 10 nm und 70 nm verwendet und als Dispergierhilfsmittel unter anderem Zucker eingesetzt. Mit den auf gutes Dispergieren optimierten Elektrolyten wurden Schichten hergestellt, wobei Abscheidegeschwindigkeiten von 0,4 µm/min erreicht wurden. Die Einbauraten für das verwendete Aluminiumoxid lagen bei etwa 1 % und die Härten reiner Goldschichten mit eingebauten Nanopartikeln bei etwa 135 HV.
Oberflächenfunktionalisierung von Polymeren
Durch das hohe Interesse am Leichtbau werden neben Leichtmetallen auch zunehmend thermoplastische Hochleistungspolymere (z.B. Polyetheretherketon (PEEK)) in Betracht gezogen. Die Festigkeit der Polymere wird durch eine Faserverstärkung erhöht, während die Oberfläche mit einer geringen Verschleißbeständigkeit nach den Worten von Gerd Paczkowski eine Schwachstelle des Werkstoffverbundes ist. Eine Möglichkeit zur Verbesserung der Situation ist die Metallisierung der Kunststoffteile. Das Thermische Spritzen eignet sich sehr gut zur Verbindung unterschiedlichster Materialklassen, dies erfordert jedoch gezielte Maßnahmen zur Bauteilvorbehandlung und Prozessparameteroptimierung. Um die Eigenschaften des Verbundes gewährleisten zu können, ist vor allem auf eine gute Haftung der Beschichtungen auf dem Grundwerkstoff zu achten. Dazu wurden von der Arbeitsgruppe des Vortragenden Untersuchungen durchgeführt.
Easy-to-clean-Lackoberflächen
Sven Müller befasste sich mit der Charakterisierung von Lackaufbauten für die Anwendung in der Automobilindustrie, mit denen easy-to-clean-Eigenschaften darstellbar sind. Dabei ist der easy-to-clean-Effekt vom Lotus-Effekt dadurch abzugrenzen, dass nicht die Mikrostruktur der Oberfläche entscheidend ist, sondern der sich ausbildende Kontaktwinkel beim Benetzen mit Wasser. Näher an der Realität, nämlich vorhandenen Schmutz von der Oberfläche einfach zu entfernen, ist allerdings das Verfahren des Vortragenden. Bei diesem wird eine Oberfläche definiert mit einem Gemisch aus Baumharz und Ruß belegt, dieses durch Trocknen konditioniert und anschließend eine Reinigung vorgenommen. Als Kriterium für den Reinigungseffekt dient die bei durch Reinigen freigelegte Oberfläche, die eine Korrelation zum Kontaktwinkel aufweist. Das neuen Verfahren zeichnet sich dadurch aus, dass es relativ schnell ist und einen großen Oberflächenbereich erfasst.
Teilereinigung
Im letzten Beitrag der wieder sehr interessanten Vortragsreihe stellte Stefan Büttner seine wissensbasierte Prozessführung in der industriellen Teilereinigung vor. Bei der Teilereinigung spielt die Sauberkeitskontrolle eine immer wichtigere Rolle, die wiederum durch eine hohe Prozesssicherheit unterstützt wird. Hierbei zeigt es sich, dass die entsprechenden Kenntnisse der Vorgänge und Verfahren bei unterschiedlichen Parteien, wie Anlagenlieferant, Verfahrenslieferant und Anwender liegen. Mit den Methoden der modernen Datenbanktechnik und Prozessverfolgung und -steuerung wurden die einzelnen Know-how-Bereich erfasst und verarbeitet. Daraus ist eine Simulation entstanden, mit der die verschiedenen Belastungszustände und die notwendigen Qualitäten der Reinigung erfasst und gesteuert werden können.
– wird fortgesetzt –
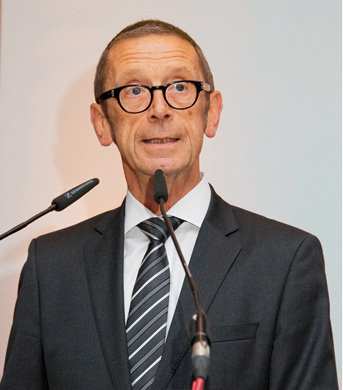
Der ZVO-Vorsitzende Walter Zeschky eröffnet die ZVO-Oberflächentage in Neuss

Motivationstrainer Slatco Sterzenbach brachte Bewegung in die Fachleute der Oberflächentechnik
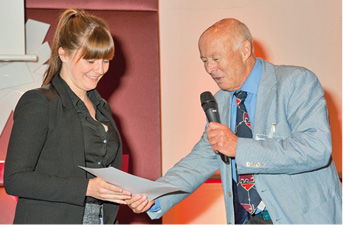
Loreen Wermuth erhält den DGO-Nachwuchsförderpreis aus den Händen von Prof. Dr. Paatsch

Heinz-Leuze-Preis für Prof. Dr. Uwe Landau (Mitte) mit Prof. Dr. Plieth und S. Leuze-Reichert

Rainer Venz, DGO-Vorsitzender












