Eine der wichtigsten Aufgaben der Oberflächentechnik ist der Schutz von Werkstoffen gegen Korrosion; ein Thema, dem sich das
37. Ulmer Gespräch gewidmet hat. In 15 Vorträgen wurden die Herausforderungen in Bezug auf die wirtschaftliche Notwendigkeit ebenso beleuchtet, wie die unterschiedlichen Verfahren aus den Bereichen der physikalischen Beschichtung, der Galvanotechnik und der Lackiertechnik. Insbesondere für die Galvanotechnik spielen die Zink- und Zinklegierungsschichten mit den unterschiedlichen Nachbehandlungsarten eine wichtige Rolle. Dieses Thema wurde im Rahmen einer Podiumsdiskussion aus verschiedenen Richtungen betrachtet. Darüber hinaus ist nach wie vor die Prüfung der Beständigkeit aus Gründen der Qualitätssicherung nicht zufriedenstellend gelöst, da zum einen die Übertragbarkeit zwischen Schnelltest und Praxisverhalten stark differiert und zum anderen zu viele unterschiedliche Verfahren mit entsprechenden Schwankungen bei den Ergebnissen in Gebrauch sind. Dazu stellten verschiedene Fachleute neue Überlegungen und Ergebnisse vor.
Seit vielen Jahren zählt die wissenschaftliche Fachtagung Ulmer Gespräch zu den wichtigsten Veranstaltungen der Deutsche Gesellschaft für Galvano- und Oberflächentechnik e. V. (DGO), die in Zusammenarbeit mit dem VDI Technologiezentrum interessante Beiträge zur Entwicklungsrichtung der Oberflächentechnik bietet. Für die inzwischen 37. Ausgabe der Tagung wurde nach den einführenden Worten von Prof. Dr. Wolfgang Paatsch mit dem Thema Korrosionsschutz und Oberflächentechnik eines der vorrangigen Themen für die Beschichtungsindustrie gewählt. Dass hier auch für die nächsten Jahre umfangreiche Anforderungen zu bewältigen sind, ergibt sich unter anderem aus einer aktuelle Studie der World Corrosion Organisation (WCO); danach entstehen durch Korrosion und deren Folgen in den Industrieländern Kosten in Höhe von drei bis vier Prozent des Bruttoinlandprodukts und damit Milliardenbeträge. Auswirkungen der Korrosion sind dabei nicht so sehr die visuell erkennbaren Veränderungen der Werkstoffe, als vielmehr die durch Schädigungen entstehenden Gefahren für die öffentliche Sicherheit oder Umweltschäden. Auch spielen Kosten durch den Stillstand von Anlagen oder Einrichtungen und die Reparatur von Schäden eine große Rolle.
Mit den Vorträgen und Diskussionen wurden in Neu-Ulm unterschiedliche Beschichtungssysteme ebenso thematisiert, wie die nach wie vor hohen Herausforderungen zum Aufklären der häufig komplexen Korrosionsprozesse. Insbesondere die stetig neu entwickelten Werkstoffe und daraus hergestellten Werkstoffkombinationen sowie die sich ändernden Umweltbedingungen werden der Korrosionsforschung und dem Korrosionsschutz auch in Zukunft ein reichhaltiges Betätigungsfeld garantieren.
Korrosion und deren Kosten
Etwa 3,1 Prozent des Bruttosozialprodukts gehen pro Jahr durch Korrosion verloren (140 Mrd. US$ in D), wobei davon etwa 25 % durch gezielten Korrosionsschutz vermeidbar wären, wie Prof. Dr.-Ing. Bernd Isecke zur Eröffnung der Fachvorträge einleitend feststellte. Planmäßig kann nur bei sehr wenigen Produkten mit einer Korrosion ohne Funktionseinschränkung über eine geplante Lebensdauer gerechnet werden, wie etwa bei Eisenbahnschienen. Umgekehrt kann bei kostengünstigen Produkten dann ein großer Schaden entstehen, wenn diese in hohen Stückzahlen hergestellt werden, beispielsweise Blumentöpfe aus Messing. Durch einen fehlerhaften Herstellprozess tritt hierbei zum Beispiel Spannungsrisskorrosion in großem Umfang auf. Ähnliche Beispiele sind aus dem Bereich der Automobilproduktion bekannt, etwa bei falsch konstruierten Türelementen (Verzicht auf eine Grundierung im Türinneren) mit einem fatalen Korrosionsverlauf von Innen nach Außen.
Bei der Verwendung von Stählen sind Schwankungen der Korrosion unter anderem durch die unterschiedlichen Preise von Nickel oder Chrom festzustellen, die häufig zu einer Änderung der Zusammensetzung von rostfreien Stählen führen. Darüber hinaus werden Werkstoffe falsch eingesetzt, mit der Folge von Spannungsrisskorrosion. Ähnliche Effekte sind vor allem im Baubereich durch nicht korrekt berücksichtigte Umgebungsbedingungen, wie falsch eingeschätzte oder übersehene Feuchtbereiche oder fehlender Zugang von Sauerstoff, bekannt. In all diesen Fällen wird zudem übersehen, dass Korrosion eine Systemeigenschaft ist, bei der Dinge wie die Bildung von Passiv- oder Deckschichten, Konzentrationen von angreifenden Bestandteilen in Elektrolyten durch Verdunsten und Nachbefeuchtung, sich ändernde pH-Werte durch Hydrolyse, sich ändernde Redoxpotenziale oder die Bildung von Korrosionselementen die Beständigkeit von Werkstoffen bestimmen.
Bei der Betrachtung von Korrosion ist zu berücksichtigen, dass die Funktionsfähigkeit auch unter ungünstigen Bedingungen erhalten bleiben muss, also eine hohe Fehlstellentoleranz gewährleistet ist. Sehr empfehlenswert ist nach Aussage des Vortragenden eine höhere Investition beim Entwurf von Bauteilen oder ganzen Systemen; dies schließt die Phasen Konstruktion, Werkstoffauswahl und Bauteilgestaltung mit ein. Damit lassen sich die späteren Wartungs- und Instandhaltungskosten senken. Zudem ist es empfehlenswert, sich im Vorfeld einer Investitionsentscheidung unterschiedliche Meinungen einzuholen und das eigene Wissen nicht zu überschätzen.
Grundlagen der Korrosion
Prof. Dr. Bund gab einen Einblick in die Grundlagen der Korrosion. Hier ist zunächst die Thermodynamik zu betrachten, derzufolge die meisten Metalle in die thermodynamisch stabilere Form ihrer Oxide übergehen. In diesem Fall werden die aus den Metallen freigesetzten Elektronen bei Anwesenheit von Sauerstoff von diesem aufgenommen. Nur Gold besitzt ein so hohes Nernstpotenzial, um diesen Vorgang zu unterbinden. Allerdings macht die Thermodynamik keine Aussagen über die Zeit, innerhalb derer solche Vorgänge ablaufen. Das unterschiedliche Verhalten bei der Betrachtung der Thermodynamik ist die Grundlage zur Herstellung von Batterien, bei der je nach gewählter Werkstoffkombination unterschiedliche Energiebeiträge freigesetzt werden. Dass trotzdem Metalle mit einer praktisch vertretbaren Lebensdauer verwendbar sind, liegt an der Kinetik der Korrosionsprozesse. Eine Verlängerung der Lebensdauer ist vor allem durch eine gut gewählte Kombination von Werkstoffen mit geringem Potenzialabstand zu erreichen.
Messwerte für Korrosionsvorgänge liefert die Aufzeichnung von Stromdichte-Potenzial-Kurven, die am Punkt des Gleichgewichtspotenzials die Austauschstromdichte angeben. Damit kommt die Kinetik als wichtige Größe der Korrosion zum Tragen. So hängt die Reaktionsgeschwindigkeit beispielsweise von der Diffusion der beteiligten Partner ab. Ähnlich starken Einfluss haben die reaktionsfähigen Flächen, da die auftretende lokale Stromdichte am Korrosionspunkt begrenzt ist.
Durch Beschichtung kann die Korrosion eines Werkstoffs verändert werden. Dabei kann prinzipiell zwischen einem kathodischen und einem anodisch wirkenden Korrosionsschutz unterschieden werden. Als das am häufigsten angewandte System für den kathodischen Korrosionsschutz gilt die Beschichtung mit Zink und Zinklegierungen; sie zählt zu den am meisten genutzten galvanischen Verfahren für Eisenmetalle. Auch hier steht nicht so sehr der absolute Schutz gegen Korrosion im Vordergrund als vielmehr die Reduzierung der unvermeidlichen Korrosionsabläufe.
Zum Abschluss seines Beitrags stellte Prof. Dr. Bund als wissenschaftlich wichtige Messmethode zur Aufklärung der Korrosionsvorgänge die Aufzeichnung der Stromdichte-Potenzial-Kurven vor. Dazu werden die Stromdichten von anodischen und kathodischen Reaktionen gemessen, wie sie bis zu mehreren hundert Millivolt über und unter dem sich einstellenden Korrosionspotenzial ablaufen. Dabei wird mit solchen Messungen auch die Kinetik an den Phasengrenzen von Werkstoffen zum umgebenden Elektrolyt ermittelt. Bei diesen handelt es sich allerdings immer um eine Systemaussage, sodass eine Übertragung der Werte für Potenzial oder Stromdichte nur sehr bedingt möglich ist.
Ein weiteres Verfahren ist die Impedanzspektroskopie, bei der die Widerstände an den Grenzflächen gemessen werden. Auch hier muss berücksichtigt werden, dass die Werte einer Kurzzeitmessung nur beschränkt auf das Systemverhalten im Felde übertragbar sind.
Korrosion von Harstoffschichten
Dr. Martin Fenker befasste sich in seinem Vortrag mit dem Korrosionsverhalten von Hartstoffschichten auf Stahl. Kritisch ist bei Hartstoffschichten in der Regel deren hohe chemische Beständigkeit, entsprechend einem positiven elektrochemischen Potenzial und der daraus resultierenden Neigung zum Entstehen von Lochkorrosion. Ausgangspunkte dieser Korrosionserscheinungen sind häufig nicht zu vermeidende Oberflächendefekte wie Droplets (punktuelle Wachstumsstörungen in physikalisch abgeschiedenen Schichten), aber auch solche mit deutlich kleineren Abmessungen auf der Nano- und Submikron-Skala.
Ein wichtiges Kriterium für die Entstehung von groben Defekten ist die Schichtdicke beziehungsweise die Wachstumsgeschwindigkeit von physikalisch abgeschiedenen Schichten und Schichtsystemen, die häufig zu sehr groben Kristallen mit einer großen Anzahl an Zwischenräumen führt. Des Weiteren erzeugen Rückstände, die vor dem Start der Beschichtung nicht vollständig abgereinigt werden, Defekte. Im Nano- und Submikrobereich spielen Kristallstrukturen eine Rolle, wobei amorphe Schichten die besten Voraussetzungen für einen hohen Korrosionsschutz bieten.
Ab Schichtdicken von mehr als zehn Mikrometer erreichen die Korrosionsströme geringe Werte, sodass Stähle hinreichend gegen Korrosion geschützt werden können. Ebenfalls positiv wirkt sich die Anwendung einer Biasspannung aus, durch welche die Dichte der Schichten erhöht wird.
Prinzipiell besitzen Titannitrid (TiN) und Titan-Bor-Nitrid (TiBN) hohe und Niobnitrid (Nb2N) einen eher niedrigeren Wert für das elektrochemische Potenzial; alle liegen aber über dem von Stählen wie HSS 1.3207. Im neutralen Salzsprühtest zeigt es sich, dass die elektrochemischen Potenziale eher eine geringe Rolle spielen, während vor allem Fehlstellen in der Schicht zum Versagen führen. Dabei tritt in der Regel eine starke Lochkorrosion auf, bei der das Substrat unter einer Fehlstelle aufgelöst wird, ohne die Schicht zu zerstören.
Ein Ansatz zur Verbesserung des Korrosionsverhaltens sind Multilagenschichten, wobei Nitridschichten mit rein metallischen Schichten gemischt werden können. Durch solche Systeme werden Spannungen in den Schichten abgebaut und der Korrosionsstrom wird gesenkt. Allerdings fehlt bei vielen derartigen Untersuchungen der Vergleich mit dem üblichen Salzsprühtest.
Zur Herstellung von Multilagen bieten sich auch Kombinationen aus Nitriden und sehr unedlen Werkstoffen wie Magnesium an, bei denen die Gesamtbeständigkeit des Systems mit dem steigenden Anteil an Magnesium zunimmt. Außerdem zeigen Schichten auf glattem Untergrund eine höhere Beständigkeit als solche auf rauem Untergrund.
Ein weiterer Ansatz geht dahin, Schichten mit hohem elektrischen Widerstand für den Korrosionsschutz einzusetzen. Auf Stahl wurde eine erhöhte Korrosionsbeständigkeit mit Schichten erreicht, die beispielsweise einen hohen Sauerstoffanteil aufweisen. In einem weiteren Projekt wird an der Verbesserung solcher Systeme gearbeitet. In Kombination mit einer ALD-Beschichtung nach der PVD-Beschichtung – sogenannte Duplex-Schichten – sollte die Korrosionsbeständigkeit ebenfalls verbessert werden. Die ALD-Schichten verbessern die Beständigkeit des Gesamtsystems insbesondere durch deren extrem gute Streuung, wodurch auch Spalte und Poren der PVD-Schicht abgedeckt werden. Als Materialien kommt neben Aluminium auch Tantal in Betracht. Die Abscheidung erfolgt mit sehr hoher Effizienz.
Korrosion bei CFK-Metall
Die Einsparung von Treibstoffen ist sowohl bei Fahrzeugen als auch bei Fluggeräten die treibende Kraft für den Einsatz von kohlefaserverstärkten Kunststoffen, die über eine besonders hohe Festigkeit verfügen und so den Bau von leichten Strukturelementen erlauben. Prof. Dr.-Ing. Christian Hühne zeigte einführend die neuen Ansätze zur Herstellung von Flugzeugkörpern aus Laminaten aus CFK und Metalllagen. Die in der Regel sehr duktilen Metalllagen sind in der Lage, auftretende Rissen zu stoppen, und die Fasern des CFK liefern die hohe Festigkeit in Faserrichtung. Solche Laminate sind auch gegen Impakt, also punktuelle mechanische Belastung beispielsweise durch Schlag, sehr beständig. Derartige Werkstoffverbunde zeichnen sich zudem durch ein sehr positives plastisches Deformationsverhalten aus. Die Metalllagen bestehen hierbei aus Stahlfolien (z. B. 1.4310) mit einer Dicke von etwa 50 Mikrometer. Dieser Verbundwerkstoff weist eine um etwa 14 Prozent höhere Festigkeit auf, wobei Werte von mehr als 700 Nm/kg erreicht werden. Insbesondere bei einer Biegebeanspruchung besteht bei reinem CFK das Problem eines verminderten Vermögens zu Energieaufnahmen, das durch Verwendung des Laminats um mehr als 50 Prozent erhöht werden kann.
Ein erster Einsatz erfolgte bei einer Tragfläche, bei der insbesondere auf eine sehr glatte Oberfläche ohne jede Niete zu achten war. Hierfür wurden in die eingesetzten Tragflächenelemente weitere Funktionen wie Antennen oder Heizungen integriert. Lokale Hybridisierungen mit einer erhöhten Zahl an Metallfolien erlaubten die Herstellung von Bereichen für höhere Krafteinleitungen. Unter Hybriden werden hier zusätzliche Elemente wie eingelagerte Versteifungen beispielsweise mit Schaumkernen verstanden. Darüber hinaus lassen sich diese Bauteile mit partiellen Metallfolien auf der Außenseite ausstatten; so lässt sich der Schutz gegen Abrasion drastisch verbessern.
Zu den besonderen Herausforderungen von solchen Verbundstrukturen zählen die Anbindung zwischen Metall und Kunststoff sowie die Korrosion des Verbundes, aber auch Verfahrensanforderungen zum spanenden Bearbeiten oder die Bemühungen zur Reduzierung der Herstellkosten. Für die Haftung kommen beispielsweise Sol-Gel-Prozesse, Beizen oder eine mechanische Aufrauung durch Strahlen in Betracht. Die besten Eigenschaften sowohl in Bezug auf die Haftung als auch auf die Skalierbarkeit in eine reguläre Produktion wurde mittels Vakuumstrahlen erzielt. Ein weiteres Kriterium der Untersuchungen bezog sich auf das thermische Verhalten, wie es beim Aushärten auftritt und zu Eigenspannungen und Verformungen führen kann.
Ein Aspekt bei der Auswahl von Verbunden ist auf deren Langlebigkeit gerichtet. Dazu kamen Korrosionsmessungen wie EIS oder Polarisation zum Einsatz, aus denen sich unter anderem eine erhebliche Differenz beim Ruhepotential ergab, die eine stärkere Korrosion aufgrund von Elementbildung nahelegt. Im Korrosionstest wurde dies bestätigt und Lochkorrosion festgestellt.
Korrosion bei Biomassekraftwerken
Wie Dr. Melanie Montgommery einleitend betonte, beruht die Korrosionsgefahr bei Biomassekraftwerken auf der relativ hohen Temperaturbelastung verbunden mit entsprechenden Korrosionsmedien. Durch das steigende Interesse an solchen Kraftwerken steigt auch die Forderung nach kostengünstigen, beständigen Elementen in den Kraftwerksanlagen. Die Temperaturen reichen über 500 °C im Kontakt mit dem Dampf bis zu 1000 °C auf der Feuerseite. Je nach Zusammensetzung des Brennstoffs werden dabei unterschiedliche Komponenten im Brenngas freigesetzt, die zu Ablagerungen und einem Korrosionsangriff der unterschiedlichen Metallkomponenten im System führen. Insbesondere die gegenüber reinen mit Öl, Gas oder Kohle betriebenen Kraftwerken wechselnden Zusammensetzungen des Brennstoffs sind eine besondere Herausforderung für den Schutz der Metalle.
Unterstützt wird die Korrosion durch sich bildende Ablagerungen auf den Metallelementen, die in der Regel porös sind und damit korrosive Medien aufnehmen und mit dem Grundwerkstoff in Kontakt bringen können. Vor allem Salzsäure und Kaliumsulfat (K2SO4) in Zusammenwirkung mit Salzsäure wurden als problematische Medien identifiziert.
Als besonders kritisch hat sich die Chromverarmung im Oberflächenbereich erwiesen, welche zu einer sehr porösen Metalloberfläche führt. Dabei nimmt die Korrosionsgeschwindigkeit mit der Temperatur stark zu und kann Werte bis zu 1 µm/h erreichen. Die besten Ergebnisse wurden bei Chromgehalten von etwa 15 Prozent erzielt, während höhere Chromgehalte einen negativen Effekt auf die korrosive Auflösung haben. Dabei wird Chrom, ebenso wie Nickel und Eisen, durch Bildung von Chlorid aus der Oberfläche herausgelöst. Das Oxid wird im Fall von Chrom in einiger Entfernung von der Oberfläche in Chromoxid umgewandelt, während Nickel und Molybdän unter bestimmten Bedingungen als Metall an der Oberfläche verbleiben.
Als Biomasse untersucht wurden insbesondere Stroh und Holzschnitzel, bei denen sich vergleichbare Ergebnisse zeigten. Aufgrund der Ergebnisse wurde für Dänemark die Empfehlung ausgesprochen, die Dampftemperatur unter 540 °C zu halten. Durch die Beimischung von Kohle kann der Gehalt an schädlichem Kalium verringert werden. Der Nachteil von Stroh zeigte sich insbesondere am steigenden Anteil an Salzsäure. Daraus wurde abgeleitet, dass der Anteil an Stroh beispielsweise auf 20 Prozent begrenzt werden sollte. Weiterer kritischer Punkt ist der Wassergehalt im Brennstrom. Dazu wurde eine Sensor in das System eingeführt, der eine Begrenzung auf den zulässigen günstigen Bereich erlaubt.
Offshore-Windanlagen
Sascha Buchbach stellte in seinem Referat die besonderen Herausforderungen bei der Herstellung von Offshore-Windanlagen sowie bei deren Inspektion und Reparatur vor. Er wies darauf hin, dass erhebliche Unterschiede bezüglich der Belastung zwischen Windkraftanlagen in der Nord- und in der Ostsee auftreten. Neben der Belastung durch Wasser müssen die ungünstigen Wetterlagen durch Sturm oder Eisbildung sowie der biologische Angriff bewältigt werden, ebenso wie die Notwendigkeit, verschiedene Werkstoffe einzusetzen. Darüber hinaus ist zu berücksichtigen, dass Wartung und Reparatur mit hohem Aufwand verbunden sind, wobei auftretende Schäden sehr schnell zum vollständigen Ausfall einer Anlage führen können.
Da die Korrosionsraten bei Stählen bis zu 200 µm pro Jahr betragen können, muss der Einsatz aller möglichen Techniken, von der Auswahl der Materialien, über die Beschichtung bis hin zum aktiven Korrosionsschutz in Betracht gezogen werden. Üblich sind Beschichtungsdicken von 500 µm bis 1000 µm, beispielsweise durch Duplexschichten mit Zinkstaub. Kritisch ist der Bewuchs, der nicht nur ein zusätzliches Gewicht, sondern auch die Förderung von beispielsweise biologisch unterstützter Korrosion bewirken kann.
Neben den Vorkehrungen bei der Herstellung der Anlagen, wird an einem Projekt zur Erstellung von Reparatur- und Instandhaltungssystemen gearbeitet. Eine Offshore-Anlage, die seit zwei Jahren in Betrieb ist, dient hier als Arbeitsprojekt. Es wird vor allem versucht, Verfahren zur Reparatur ohne einen Abbau der Anlage vornehmen zu können, da in diesem Fall die Kosten deutlich niedriger sind. Die Differenzen zu Anlagen an Land ergeben sich daraus, dass für die Wartungsarbeiten an Land etwa 25 Euro und für die auf See etwa 4000 Euro pro Quadratmeter veranschlagt werden müssen. Das Konzept schließt auch die Ermittlung der kritischen Bereiche einer Offshore-Anlage ein, um Schädigungen an diesen Bereichen zukünftig zu vermeiden.
Aufgrund der hohen Anforderungen an die Prüfung (100-%-Prüfung innerhalb von vier Jahren) und die Reparatur, wird derzeit der Einsatz von Prüfdrohnen untersucht, durch die ein Teil des Aufwandes deutlich reduziert werden kann. Besondere Anforderungen bestehen zudem an die verwendeten Beschichtungssysteme bezüglich der Verarbeitung.
– wird fortgesetzt –

Praktische Spannungsreihe (in V) von Werkstoffen in bewegtem Meerwasser bei Raumtemperatur
Quelle: Prof. Bund/Ulmer Gespräch 2015/wwwcorrosionist.com
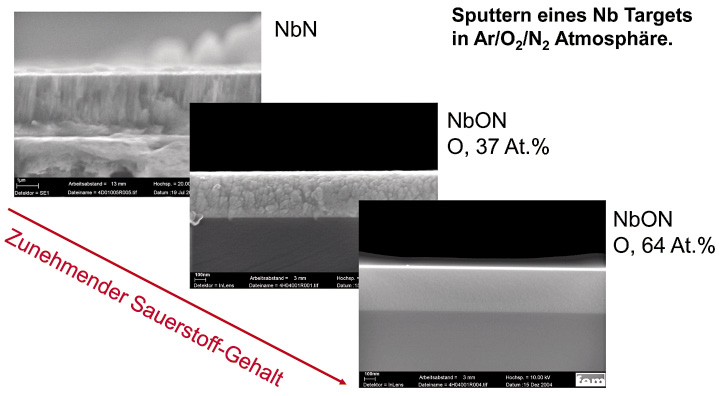
Änderung der Schichtstruktur mit steigendem Sauerstoff, gezeigt an Bruchbildern
Quelle: Dr. Fenker/Ulmer Gespräch 2015
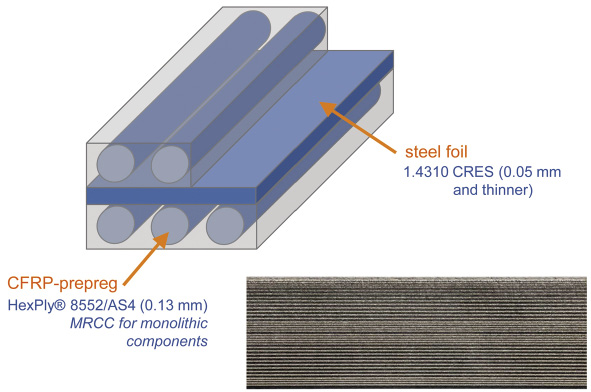
Aufbau des Werkstoffverbundes aus CFK und Stahlfolien
Quelle: Prof. Hühne/Ulmer Gespräch 2015
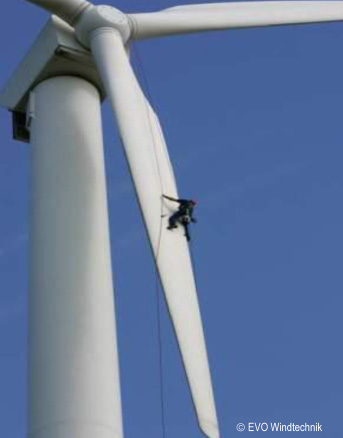
Hohe Kosten entstehen bei Reparaturen durch die schwierige ZugänglichkeitQuelle: S. Buchbach
Ulmer Gespräch – Podiumsdiskussion
Korrosionsschutz und Oberflächentechnik
Die Podiumsdiskussion beim diesjährigen Ulmer Gespräch setzte sich mit der Normung im Korrosionsschutz auseinander. Als Teilnehmer der Runde diskutierten unter der Leitung von Prof. Dr. Bernd Isecke Peter Fischer, Rainer Venz, Dr. Andreas Heyn und Christof Waibel das Thema, ob und in welchem Umfang Normung die nach wie vor herrschende Unsicherheit bei der Korrosionsprüfung verbessert. Für die Beschichtungsindustrie stellt sich die Frage, welche der zahlreichen und deutlich unterschiedlichen Prüfverfahren die richtigen Kenngrößen für die eigenen Beschichtungen liefert. Darüber hinaus werden nach wie vor direkte Rückschlüsse von den unterschiedlichen Kurzzeitprüfungen auf das Verhalten im Feld angezweifelt. Für die Industrie folgt daraus die Herausforderung, sich auf allgemein akzeptierte Verfahren und Aussagen zu verständigen.
(Nachfolgend ist die Diskussion, ohne Anspruch auf Vollständigkeit, zusammenfassend widergegeben.)
Wie Prof. Isecke zu Beginn der Diskussion vermerkte, sind die verwendeten Begrifflichkeiten keine wirkliche Hilfe, da Korrosionsuntersuchung und Korrosionsprüfung nicht klar abgegrenzt werden. Darüber hinaus tragen Normen nicht dazu bei, Sicherheit bezüglich der Korrosionsbeständigkeit zu gewinnen oder Beschichtungen für die jeweiligen Bauteile auswählen zu können.
Nach Ansicht von Rainer Venz sind nicht mehr, sondern neue und angepasste Normen erforderlich. Darüber hinaus ist es wichtig, Vorschriften zu verwenden, die für die Praxis sinnvolle Produkte liefern. Nach den Worten von Peter Fischer müssen die Korrosionsvorgaben dynamischer gestaltet werden, sodass sie sich verändernden Einsatzmöglichkeiten oder Umweltbedingungen anpassen, aber trotzdem eine sichere Produktion gewährleisten.
Allerdings zeigen nach Ansicht von Dr. Heyn die Erfahrungen bei der Anpassung der Normen an sich ändernde Bedingungen und Wünsche aus der Industrie, dass vorwiegend die wirtschaftlich mächtigen Unternehmen in der Lage sind, ihre Forderungen gegenüber den schwächeren Partnern durchzusetzen. Dies wiederum muss nicht zwangsläufig bedeuten, dass die besseren Systeme oder Verfahren den Weg in die Praxis finden – besser beispielsweise im Sinne von Ökologie.
Nach Meinung von Prof. Isecke besteht das Problem unter anderem darin, dass viele angebliche Fachleute mit unterschiedlichem Unternehmenspotenzial verschiedene Forderungen hinsichtlich der Korrosionsbeständigkeit aufstellen. Insbesondere lassen sich die in Zentraleuropa üblichen Behandlungsarten für Produkte nicht ohne Änderungen auf andere Märkte übertragen.
Dieses Problem ist nach Aussage von Peter Fischer bei den OEMs bekannt und wird zu einem gewissen Maß in den Normen berücksichtigt. Dadurch ergibt sich für die Unterlieferanten, beispielsweise Beschichter, die akzeptable Situation, für das eigene Unternehmen eine gesicherte Vorgehensweise vorzufinden.
Die Praxis zeigt derzeit drastische Änderungen bei den Anforderungen an Oberflächen. Zugleich werden aber nach den Worten von Rainer Venz die Vorgaben aus den bekanntermaßen lückenhaften Normen mehr als Vergleich zwischen den unterschiedlichen Anbietern benutzt und nicht als qualitatives Merkmal für die Beständigkeit von Oberflächen unter speziellen Einsatzbedingungen. Insbesondere finden laut Prof. Isecke die Erkenntnisse aus Wissenschaft und Forschung nicht oder nur sehr schleppend eine Umsetzung in die Praxis.
Zu berücksichtigen ist unter diesen Aspekten, dass die Normen lediglich ein Qualitätskriterium für eine auftragsmäßige Belieferung von Kunden, zum Beispiel der Automobilindustrie, sind (Anmerkung von Martin Juros).
Viele der heute verwendeten Tests wurden weiterentwickelt, so Rainer Venz, um die unterschiedlichen Neuerungen und Verbesserungen der Systemanbieter mit einzubeziehen. Dabei ist jedoch oft festzustellen, dass klassische Verfahren plötzlich nicht mehr einen Test bestehen, obwohl im Feld keine Ausfälle auftreten. Eines der bekanntesten Beispiele hierfür ist die Chromatierung, deren Unzulänglichkeiten bevorzugt bei der Suche nach alternativen Systemen in den Tests zutage getreten sind.
Insbesondere bei den Untersuchungen zur Korrosion ist nach Aussage von Prof. Isecke festzustellen, dass Korrosionsuntersuchungen nach den Vorstellungen des Versuchsführers abgewandelt werden, um beispielsweise Modellvorstellungen zu bestätigen. Aufgrund der Komplexität von Korrosionsabläufen sind Modelle erforderlich, um überhaupt zu sinnvollen Zusammenhängen mit entsprechenden Ergebnissen zu kommen. Dies setzt aber auch voraus, dass sich die Beteiligten über die fachlichen Einschränkungen bewusst sind.
Dazu wies Prof. Dr. Paatsch darauf hin, dass die OEMs die Bewertung von Oberflächen nach Standardtests wie dem Salzsprühtest erwarten und alle Beteiligten die Ergebnisse als Qualitätskriterien für eine Zusammenarbeit verwenden. Allerdings wird beim Salzsprühtest nicht ein eng definierter Prozess geprüft, sondern ein nicht überschaubares Sammelsurium von Prozessen und Systemgrößen.
Laut Christof Waibel wird in der Praxis oftmals während eines Einführungstests eine Änderung der Parameter vorgenommen, was dann dazu führen kann, dass ein zuvor gutes Schichtsystem dramatisch schlechter abschneidet. Um dann trotzdem ein Qualitätskriterium für eine Produktion zu erhalten, werden zusätzliche Tests und Prüfmethoden beigegeben oder entwickelt, was dann wiederum zum weiteren Anwachsen der Verfahren mit den bereits mehrmals genannten Nachteilen führt.
Umgekehrt sind aber die Hersteller von Prüfgeräten nach Ansicht von Prof. Isecke gezwungen, die Verfahren so zu vereinheitlichen, dass bei ähnlichen Oberflächen immer ähnliche Ergebnisse erzeugt werden. Trotz dieser Bemühungen zeigt die Praxis aber, dass die individuellen Einflüsse der Prüfer ganz erheblich in die Ergebnisse einfließen. Aus diesem Grund empfiehlt es sich, im Rahmen von Vergleichsversuchen die Beurteilung von stets der selben Person vornehmen zu lassen.
Rainer Venz betonte an dieser Stelle, dass sich dies beispielsweise bei der Einführung der chrom(VI)freien Passivierung bestätigt hat. Die damals durchgeführten Versuche haben belegt, dass die Ergebnisse entsprechender Untersuchungen nicht einheitlich sind und stark durch den Prüfer als Person beeinflusst werden.
Auf die Frage, wie große Beschichter mit der Prüfung von Oberflächenqualität umgehen, erläuterte Christof Waibel, dass oft ein großer Spagat vollzogen werden muss, um im Markt alle Kunden befriedigen zu können. Die unterschiedlichen Spezialtests der einzelnen OEMs können nicht in voller Breite ausgeführt werden. Zu Buche schlagen hier die Anlagen- und Personalkosten.
Die seit langem geführte Diskussion hat nach den Worten von Rainer Venz in Deutschland dazu geführt, dass bei den Beschichtern keine oder nur sehr selten Korrosionsprüfungen eingeführt wurden. In China sind die OEMs wesentlich rabiater vorgegangen, indem sie keine Aufträge mehr an Unternehmen ohne Prüfkammern vergeben haben. Dazu merkte Joachim Ramisch an, dass der Salzsprühtest ursprünglich für Lackierung entwickelt worden und dafür auch sinnvoll war. Für Galvanikschichten muss dies nach seiner Überzeugung bezweifelt werden.
Rainer Venz fügte an dieser Stelle ergänzend hinzu, dass inzwischen angepasste Verfahren zur Kontrolle der Beschichtungen von Produktionsprozessen entwickelt wurden und werden, die schnell eine Gut-Schlecht-Aussage liefern, ohne näher auf die Mechanismen einzugehen. Zu diesen Tests kommen inzwischen auch Simulationen hinzu, wie Dr. Heyn ergänzte. So gilt die Technologie der Erfassung und Bewertung des elektrochemischen Rauschens als ein erster Ansatz.
Wie Dr. Schillinger bemerkte, hat der Einsatz des Salzsprühtests leider zu Entfremdungen der eigentlich erzielbaren Ergebnisse geführt. So wurde insbesondere mit Einführung der Versiegelungen der Mechanismus zu einem extremen lokalen Angriff verändert. Christof Waibel ergänzte hierzu, dass die OEMs mit speziellen Abwandlungen und Anpassungen auf die Änderungen eingehen.
Abschließend betonte Rainer Venz, dass die Tests nur dann sinnvoll sind, wenn nach der geforderten Zeit gefragt wird, und nicht die Frage gestellt wird, ob der Test ohne Zeitbeschränkung überstanden wird. Nach Aussage von Peter Fischer liefert ein Teil ohne Beschädigung keinen Anhaltspunkt auf die tatsächlich vorliegende Behandlung im Feld, da hier immer eine oberflächliche Beschädigung vorliegen wird, die dann der Ausgangspunkt für einen Korrosionsangriff bei Einwirkung des korrosiven Mediums sein wird.
Prof. Isecke schloss die Diskusson mit dem Verweis ab, dass ein Test vorrangig dazu dienen soll, die Qualität einer Fertigung zu sichern und weniger dazu, Mechanismen aufzuklären.
Fazit
Für den neutralen Zuhörer folgt aus der Diskussion, dass eine weitergehende Normung keine prinzipielle Verbesserung der Situation bringen wird. Dies dürfte insbesondere auch deshalb der Fall sein, weil die Schutzverfahren derzeit einem erheblichen Wandel an neue Anforderungen unterworfen sind. Dazu zählen beispielsweise auch die durch REACh beeinflussten veränderten Zusammensetzungen bei Passivierungen als auch die erhöhten Qualitätsanforderungen oder der steigenden Wettbewerb des globalen Marktes. Demzufolge variieren auch die Prüftechnologien, sodass die Normung erfahrungsgemäß den tatsächlichen Gegebenheiten in der Industrie nicht schnell genug folgen kann. Darüber hinaus ist Korrosionsbeständigkeit eine Systemeigenschaft, bei der nur ein kleiner Teil der wirkenden Größen bekannt und erfassbar ist. Um zuverlässige Aussagen über den Korrosionsschutz treffen zu können, sind noch erhebliche Forschungsarbeiten zur Aufklärung der Mechanismen notwendig. Daraus können dann in Zukunft angepasste Testsysteme für die zahlreichen unterschiedlichen Systeme entwickelt werden. Nach Erledigung dieser Arbeiten könnte dann eine Normung möglich und sinnvoll sein.
Herbert Käszmann
WOTech GbR
Text zum Titelbild: Der Diskussion stellten sich: Peter Fischer, Rainer Venz, Prof. Dr. Bernd Isecke, Dr. Andreas Heyn und Christof Waibel (v. l. n. r.)