Korrosionsschutz und Oberflächentechnik
Eine der wichtigsten Aufgaben der Oberflächentechnik ist der Schutz von Werkstoffen gegen Korrosion; ein Thema, dem sich das
37. Ulmer Gespräch gewidmet hat. In 15 Vorträgen wurden die Herausforderungen in Bezug auf die wirtschaftliche Notwendigkeit ebenso beleuchtet, wie die unterschiedlichen Verfahren aus den Bereichen der physikalischen Beschichtung, der Galvanotechnik und der Lackiertechnik. Des Weiteren wurden die derzeit gebräuchlichen Testmethoden näher betrachtet und verglichen sowie alternative Verfahren und deren Möglichkeiten vorgestellt. Anhand von Korrosionsbelastungen und -erscheinungen an elektrischen Kontakten, an Offshore-Windanlangen sowie an den Korrosionserscheinungen der Biokorrosion wurden Spezialfälle aus dem Bereich der Korrosion vorgestellt. Mittels Simulationsverfahren und unter Einsatz von Datenbanken könnten Verbesserungen beim Korrosionsschutz in Zukunft einfacher und kostengünstiger erreicht werden. Bei den Beschichtungen sind Verbesserungen durch die Abscheidung von Sondermetallen aus nichtwässrigen Elektrolyten oder mithilfe von optimierten Nachbehandlungen zu erwarten.
Fortsetzung aus WOMag 6/2015
Realitätsnahe Prüfung von dekorativen Chromoberflächen
Die dekorativen Chromoberflächen im Außenbereich sind bei Fahrzeugen nach wie vor ein wichtiges Element. Allerdings haben sich die Anforderungen in Bezug auf die Beständigkeit gegen Korrosion in den letzten Jahren deutlich geändert, wie Marina Engelking in ihren Ausführungen eingangs vermerkte.
Der Aufbau der Beschichtung auf den Kunststoffsubstraten ist relativ komplex; sie besteht aus Kupfer (Grundschicht, ca. 25 µm), mehreren Nickelschichten (insgesamt ca. 20 µm) und der abschließenden dekorativen Chromschicht mit einer Dicke von weniger als 1 µm. Die dicke Kupferschicht trägt zum Glanz bei, ist aber insbesondere als Puffer für die unterschiedlichen thermischen Ausdehnungen von Substrat und Schicht zuständig. Die Nickelschichten sind für den eigentlichen Korrosionsschutz verantwortlich. Der Start der Schichtkorrosion wird durch die mikroporige oder mikrorissige Schicht ausgelöst, wobei sich die Wahl der Art (mikroporig oder mikrorissig) nach der erwarteten Belastung richtet. Die Chromschicht selbst hat dekorative und funktionelle Aufgaben.
Mit Auftreten der Calcium- und Magnesiumchloridkorrosion hat das klassische Schichtsystem nicht mehr in der erwarteten Weise seine Funktion erfüllt. Wie sich nach umfangreichen Untersuchungen gezeigt hat, erfolgt unter Einwirkung von Sonnenschein mit den vorhandenen korrosiven Medien ein Passivieren der Nickeloberfläche und als Folge davon eine Auflösung der Chromdeckschicht.
Ein weiterer Korrosionsfall ist die lokal beschleunigte Nickelkorrosion; mit Feuchtsalz 30 (Calcium- und Magnesiumchlorid) tritt eine drastisch beschleunigte Nickelkorrosion auf. Durch diese bricht die Chromschicht ein. Wie Untersuchungen zeigen, trägt der Bremsabrieb erheblich zu dieser Korrosionserscheinung bei.
Zu diesen speziellen Korrosionserscheinungen gab es bisher keinen Schnelltest; es waren nur Felderscheinungen erfasst. Um die Chromkorrosion nachzustellen, wird seit einiger Zeit der Test PPV 4017 Var. 2 verwendet, während für die beschleunigte Nickelkorrosion bisher keine zufriedenstellende Methode vorlag. Für beide Schadensarten wurde bei VW nach einem Schnelltest gesucht, der einfach durchführbar ist, zuverlässig die verschiedenen Erscheinungen nachstellt und nach Möglichkeit sehr schnell durchgeführt werden kann.
Entstanden ist ein Verfahren, bei dem mittels Sprühpistole ein Korrosionsmedium aufgesprüht wird und die Probe im Klimaschrank bei unterschiedlichen Klimaten ausgelagert wird. Es zeigte sich, dass hier die Chromkorrosion am ersten Prüftag bei mehr als 60 % der Teile auftrat. Als kritisch stellte sich die ursprünglich gewählte Feuchtigkeit heraus, die auf 95 % rel. Feuchte gesetzt worden war. Der gesamte Ablauf wurde inzwischen in der Vorschrift VW PV 1073A festgeschrieben.
Für die Nickelkorrosion wird eine Mischung aus Calciumchlorid und Natriumchlorid gewählt; für den Versuch werden Eisenpartikel auf die Oberfläche aufgesprüht. Unter diesen Eisenpartikeln tritt eine verschärfte Nickelkorrosion auf. Die Klimabedingungen wurden auf 50 °C und 95 % rel. Luftfeuchte gesetzt. Die Versuchsbedingungen finden sich in VW PV 1073B und zeigen unter den gewählten Bedingungen sowohl eine gute Nachstellung der mikroporigen als auch der mikrorissigen Korrosion der Chromschichten aus Chrom(VI)elektrolyten. In einem weiteren Schritt sollen die Prüfbedingungen auf die Chromoberflächen aus Chrom(III)elektrolyten ausgedehnt werden.
Wechseltests – Herausforderung für die Entwicklung
Derzeit stellen die unterschiedlichen Arten von Wechseltests zur Prüfung der Korrosionsbeständigkeit von Beschichtungen nicht nur die Beschichter vor eine Herausforderung, sondern auch die Chemie- und Verfahrensentwickler. Andrea Schiller, Chemetall GmbH, gab in ihren Ausführungen eine Übersicht über die momentan gängigen Verfahren, wie sie sich für den Verfahrensentwickler darstellen. Ihr zufolge können die Prüfungen zunächst in vier Gruppen eingeteilt werden:
- Prüfungen ohne Salzeinsatz mit Wechsel von Temperatur und Feuchtegehalt
- Prüfungen ohne Salzeinsatz aber mit Korrosionsbeschleuniger sowie Wechsel von Temperatur und Feuchtegehalt
- Prüfungen mit Salz in Form von Natriumchlorid, Mischsalzen, Zusatz von Säure zur pH-Einstellung sowie wechselnder Temperatur und Feuchte
- Prüfungen mit Salz, Temperatur- und Feuchtewechsel sowie Bestrahlung
Eine weitere Klassifizierung richtet sich nach den in den DIN-Normen erfassten Verfahren. Dies sind zum einen der reine Wechseltest (Temperatur, Feuchte) in DIN EN ISO 6270-2AHT sowie die Verfahren mit Korrosionsbeschleuniger – in der Regel Schwefeldioxid – aber ohne Salz, wie sie in DIN 50018, DIN EN ISO 3231, DIN EN ISO 6988 und DIN EN 13523-23 erfasst sind.
Ein weitaus größere Zahl an Verfahren nutzt Salz als Korrosionsbeschleuniger: Allein für die Verwendung von Natriumchlorid, als Sprühnebel aufgebracht, lassen sich 19 unterschiedliche Varianten aufzählen. Hier sind vorwiegend Werksnormen von allen wichtigen Automobilherstellern zu nennen. Für den Salzauftrag durch Beregnung nannte Andrea Schiller sieben unterschiedliche Normen (eine ISO-Norm und sechs Werksnormen) und mittels Tauchen in Natriumchloridlösung nochmals acht Werksnormen.
Als eines der meistverwendeten Verfahren, das damit fast den Status eines Standardverfahrens aufweisen kann, gilt das der VDA 621-415. Dies hat allerdings den Nachteil, dass das Angriffsbild des Tests nicht mit dem der Freibewitterung übereinstimmt. Dazu zeigte die Vortragende Messergebnisse an verschiedenen Vorbehandlungen, aus denen klar die Schwächen der unterschiedlichen Prüfmethoden abgeleitet werden können. Ein daraufhin neu entwickelter Test für Vorbehandlungen zeigte bei den meisten Varianten vergleichbare Ergebnisse, zumindest tendenziell. Bei zwei Varianten traten überraschenderweise zwei Effekte auf, deren Ursache näher untersucht werden muss. Der Steinschlagtest hat zum Testergebnis bei dem zweiten neuen Verfahren keine nutzbaren Kenntnisse beigetragen und kann daher für die Zukunft entfallen.
Kundenbezogene Prüfungen sind allerdings nicht auf andere Prüfungen übertragbar. Stets zu berücksichtigen ist das Verhalten des Substrats. Des Weiteren müssen bei Neuentwicklungen stets Prüfungen zu bestehenden Tests durchgeführt und ein Vergleich vorgenommen werden.
Instrumentierte Langzeittests
Dr. Andreas Heyn befasste sich mit der Instrumentierung von Langzeittests für Korrosion, die in erster Linie dazu dienen sollen, aus den Versuchen weitere hilfreiche Daten zu gewinnen. Unter dem Begriff des Langzeittests versteht Dr. Heyn Versuche, die mehrere Tage bis Monate dauern und durch einen deutlich höheren Aufwand charakterisiert sind. Dies beinhaltet die kontinuierliche Erfassung und Bewertung von Faktoren, die eine Korrosion auslösen, sowie deren Verlauf. Im Gegensatz dazu werden bei Kurzzeitprüfungen bewusst die auslösenden Prozesse für Korrosion angestoßen und erfasst.
Ansätze können beispielsweise die Zugabe von Proben immer gleicher Ausführung, die Kontrolle des Mediums, die Verwendung von Sensoren oder die Überwachung von Teilstrukturen unter Anwendung von Analysengeräten elektrochemischer oder zerstörungsfreier Art sein. Nach Ansicht des Vortragenden liefert vor allem das elektrochemische Rauschen wichtige Anhaltspunkte, die auch nicht von außen angeregt werden. Ein interessantes Messgerät wurde vom Vortragenden entwickelt; es kann bis zu sechs Probenbereiche vermessen. Aus den erhaltenen Kurven werden Werte wie Potenzial, Elementstrom oder Rauschwiderstand ermittelt.
Das System ist sehr universell einsetzbar; es wurde unter anderem an Alternativmaterialien für Wärmetauscher, den Einsatz von Inhibitoren für Kühlmittel, Implantatwerkstoffe oder Erosions-Korrosions-Tests getestet. Interessant ist der Einsatz der Technik für die Sprühnebelverfahren, bei denen ebenfalls elektrochemische Messungen vorgenommen werden können. Untersucht wurden mit der Methode galvanisch verzinkte Kleinteile entsprechend DIN EN ISO 9227. Dabei war erkennbar, wie schnell die Passivschicht aufgelöst und die aktive Korrosion in Gang gebracht wird. Das Verhalten eines solchen Systems kann durch Veränderung des Gehalts an Kohlenstoffdioxid näher untersucht werden, aus dem sich der Einfluss von verschiedenen Gaskonzentrationen zeigt.
Ein weiterer Anwendungsfall ist die Analyse der VDA-neu (233-102) mithilfe von ER-Sensoren, aus der sich der Zeitraum bis zum Auftreten einer passiven Oberfläche abschätzen lässt. Die Instrumentierung unterstützt das Erkennen von Effekten, die einen Korrosionsvorgang ändern, oder auch die Sinnhaftigkeit von Versuchen.
Goldoberflächen für elektrische Kontakte
Prof. Dr. Jian Song eröffnete die Runde der Freitagsvorträge mit einer Betrachtung modifizierter Goldoberflächen für elektrische Kontakte, insbesondere unter Berücksichtigung einer Verschleißbelastung. Für derartige Kontakte werden in der Regel Kupfer oder Kupferlegierungen als Basiswerkstoffe eingesetzt. Diese werden durch Schichten aus Zinn, Nickel, Silber oder Gold (und Mischungen dieser verschiedenen Metalle) verwendet. Diese Schichtmetalle schützen durch die Bildung einer dünnen, aber die Kontaktfähigkeit nicht beeinträchtigenden Passivschicht oder aufgrund ihres edlen Charakters.
Der Verschleiß bei solchen Kontakten ist eine Folge von Mikrobewegungen, die wiederum auf Vibrationen oder thermische Prozesse (mit den daraus resultierenden thermischen Ausdehnungen) zurückzuführen sind. Um den Schutz gegen Korrosion zu gewährleisten, dürfen die vorhandenen Schichten keine Poren besitzen.
Unterliegen die Kontaktoberflächen einer Oxidation, so steigt der Kontaktwiderstand, was sich beispielsweise als Wackelkontakt äußert. Bei zugänglichen Kontakten kann das Aus- und wieder Einstecken das Problem beheben. Besonders kritisch wird die Situation, wenn der Oberflächenbereich aus Edelmetall abgerieben ist und die darunter liegende Schicht oxidiert.
Bei Gold wird allerdings aus Kostengründen auf möglichst dünne Schichten zurückgegriffen, die dann fast immer Poren enthalten. Die Poren werden beispielsweise mit SAM-Beschichtungen verschlossen, was jedoch nur für Einsatztemperaturen bis 100 °C möglich ist. Je nach Schädigung einer Edelmetalloberfläche werden aufgrund des erkennbaren Kontaktwiderstandes unterschiedliche Lebensdauern (Lebensdauer 1 und Lebensdauer 2) charakterisiert, wobei Lebensdauer 1 einem noch funktionierenden Kontakt mit geringen Schadstellen zuzuordnen ist.
Die Verschleißbeständigkeit einer Goldoberfläche wird beispielsweise durch das Zulegieren von Elementen wie Kobalt oder Nickel erhöht. Allerdings ist die Verbesserung begrenzt, da bei zu hoher Härte die Schicht zerbricht und dadurch ein wesentlich stärkerer Verschleiß auftritt. Ein neuer Ansatz befasst sich mit dem Einbau von Nanopartikeln in die Schicht. Erste positive Ergebnisse wurden mit Nanopartikeln aus Keramik erzielt. Dabei zeigen die Partikel sehr unterschiedliche Werte: Aluminiumoxid weist hier die höchste Verbesserungsrate auf; es ist jedoch eine relativ uneinheitliche Verteilung festzustellen. Des Weiteren spielt die Größe eine Rolle; hier zeigen die sehr kleinen und die größeren Nanopartikel die geringste Verbesserung. Abhängigkeiten ergeben sich auch durch unterschiedliche Schichtaufbauten beziehungsweise unterschiedliche Unterschichten.
Schichtsysteme für neue Energien
Lars Lichtenstein gab einen Einblick in die Zertifizierungsverfahren für Windkraftanlagen. Dabei wies er eingangs darauf hin, dass die heute üblichen 6-MW-Anlagen bei enormen Abmessungen während ihres Lebens etwa 108 Rotationen ausführen und damit primär das Fundament sehr stark belasten beziehungsweise auch zerstören. Für solche Systeme müssen heute nachweislich beständige Beschichtungssysteme vorhanden sein, die den Schutz über einen Zeitraum von 25 Jahren gewährleisten. An Beispielen zeigte Lars Lichtenstein Korrosionsschäden, die durch unsachgemäße Herstellung, Transport oder Montage verursacht wurden.
Genehmigt werden solche Anlagen durch das Bundesamt für Seeschifffahrt und Hydrographie im Rahmen eines mehrstufigen Prozesses. Zu berücksichtigen sind dabei auf jeden Fall Mindestanforderungen mit einem ausführungsreifen Detaillierungsgrad, die bereits planerisch enthalten sein müssen und somit bereits vor der Auftragsvergabe einer Anlage festgelegt werden. Die Anforderungen der Genehmigungsbehörde beziehen sich auf Schadstoffe in den Beschichtungen sowie die Tauglichkeit der Beschichtungssysteme.
Als Richtlinien sind ISO 20340, Norsok M-501 sowie der BSH-Standard zu berücksichtigen. In ISO 20340 ist ein Kurzzeittest enthalten, der jedoch über 4200 Stunden läuft und die gesamte geforderte Lebensdauer abdecken soll. Für die geforderten Beständigkeiten liegen einige zertifizierte Systeme vor.
Funktionsschichten gegen Biokorrosion
Einer der kritischen Korrosionsangriffe ist die Biokorrosion; sie ist häufig durch den vorhandenen Bewuchs auf befallenen Teilen nur sehr schwer als solche zu erkennen. Wie Prof. Dr. Uwe Landau einleitend betonte, liegt der Anteil der Biokorrosion an allen Korrosionsschäden in Deutschland bei etwa 20 Prozent. Ausgelöst wird Biokorrosion durch das Milieu, das sich durch Bewuchs im erzeugten Biofilm einstellt und gegen den Zugriff von Außen stark geschützt ist. Bisher liegen noch relativ geringe Kenntnisse über das System aus Biofilm und korrodierendem Metall vor, sodass auch Schutzmechanismen kaum vorhanden sind.
Biokorrosion wird durch drei Bedingungen identifiziert: Biofilm, Korrosionsprodukte und Rückführung der Korrosionsspuren auf Mikroorganismen. Schwierig ist dies durch die hohe Komplexität der Biokorrosion. Als einfachster Hinweis gilt der vorhandene und häufig gut erkennbare Biofilm. Als Ansatzpunkt für eine Besiedlung gelten konditionierte Filme auf Oberflächen, aber auch bestimmte Strukturen der Oberfläche. Daraus wächst dann der eigentliche Biofilm unter Bildung der günstigen Umgebung. Im Biofilm findet eine Kolonialisierung statt, bei der neue Stoffe gebildet werden. Die Filme enthalten Bakterien, Viren und sonstige Keime. Sie können sehr große Ausmaße annehmen und die Funktion von Anlagen und Geräten beeinträchtigen. Zudem werden dort schädliche Inhaltsstoffe, wie Chloride oder Schwefelverbindungen, angereichert, die einen Korrosionsvorgang beschleunigen. Bereits die ersten Untersuchungen zur Aufdeckung der Biokorrosion von 1934 hatten vor allem Schwefelverbindungen als kritisches Element identifiziert.
Die Auswirkungen des biologischen Befalls von Oberflächen sind vielfältig. Sie reichen von der Veränderung der Strömungseigenschaften bei Schiffsrümpfen über Druckverlust und Verstopfungen in Rohrleitungen, verstärkter Kalkablagerung und Blockierungen von Ventilen, Verblockung von Membranen und Harzen in der Wasseraufbereitung bis hin zu verstärkter Korrosion oder Beeinträchtigung des Aussehens.
Verhindert wird Biokorrosion durch die Verwendung von Bioziden. Dabei ist zu berücksichtigen, dass die Filme beim Einsatz von Bioziden nicht dauerhaft entfernt werden. Alternativ dazu kann die spezielle Silberoberfläche AGXX verwendet werden, bei der auch die Keime selbst verringert werden und so einem erneuten Bewuchs vorgebeugt wird. Die AGXX-Oberfläche bewirkt die Erzeugung einer katalytischen Reaktion zum Austausch von Elektronen, das heißt die Auslösung von Redoxvorgängen. Des Weiteren können Stoffe freigesetzt sowie die Oberfläche im Mikrobereich so gestaltet werden, dass sich keine Keime anlagern können. Eine weitere Methode ist die Auftragung von Polyglycerinen, die den Zugang der Mikroorganismen zur Oberfläche unterbinden. Stachelige Oberflächen lassen sich durch Zinkoxid herstellen; sie zerstören gezielt die Membranen der Mikroorganismen.
Die Funktion der Freisetzung kann unter anderem mit zusätzlich enthaltenem Kupfer erzeugt werden. Hierbei wirkt nicht nur das Kupfer als solches, sondern dessen Phasenanteile und Kristallstruktur. Durch Legierungsanteile wie Chrom, Zirkon, Aluminium, Nickel und Eisen kann die desinfizierende Wirkung noch verstärkt werden.
Die Wirkung der speziellen Silberoberfläche AGXX wurde unter anderem in Wassersystemen von Flugzeugen, Duscheinrichtungen, Maschinen zur Papierherstellung oder der Wasserversorgung der internationalen Raumstation unter Beweis gestellt.
Simulation
Korrosionserscheinungen können sehr vielfältig sein, deshalb werden auch Ansätze zur Simulation von Korrosionsvorgängen als Möglichkeit zur Aufklärung der Abläufe und damit zum vorbeugenden Schutz herangezogen. Dr. Robrecht Belis stellte hierzu Ansätze vor, die durch Untersuchungen zusammen mit dem amerikanischen Militär, insbesondere der Navy, angestellt wurden. Insbesondere bei Flugzeugen machen sich die Verwendung der unterschiedlichen Leichtbauwerkstoffe und deren Einsatz in Meeresklima nachteilig bemerkbar, ebenso wie die zunehmende Verbannung von Stoffen wie Chromat oder Kadmium. Darüber hinaus erweist es sich als nachteilig, das die Konstrukteure oftmals nicht das entsprechende Fachwissen besitzen, um die Wirkungen von Materialkombinationen abzuschätzen. In Europa sind nach Aussage von Dr. Belis derzeit vor allem die Änderungen durch REACh ein starker Anlass zur Modifikation von bestehenden Prozessen und zur Einführung neuer Verfahren. In den USA ist das die OSHA housekeeping.
Im Weiteren betonte der Vortragende, dass nicht korrodierende Werkstoffe in den seltensten Fällen eine Lösung für Korrosionsprobleme darstellen, oftmals fördern sie Korrosion, wie beispielsweise CFK. Besonders macht sich dies bei Flugzeugen bemerkbar; diese sind neben den Korrosionsmedien starken Änderungen in Temperatur und Feuchtigkeit unterworfen, wobei sich häufig sehr rasch Feuchtigkeit innerhalb der Geräte ansammeln kann. Eine Anpassung an neue Technologien ist hier schwierig, da in der Luftfahrt Änderungen nur sehr schleppend umsetzbar sind.
Mithilfe von Programmen werden als kritisch erachtete Punkte mit entsprechenden Materialkombinationen ermittelt und deren Auswirkungen berechnet. Solche Kombinationen werden (virtuell) unterschiedlichen Medien ausgesetzt und deren elektrochemisches Verhalten wird ermittelt. Aufgrund dieser Ergebnisse werden die Auswirkungen auf die jeweiligen Bereiche simuliert und dargestellt. In den Simulationen können auch unterschiedliche Mengen an korrosivem Medium (Dicke von Feuchtefilmen) betrachtet werden. Vor allem lassen sich relativ schnell Änderungen vornehmen und deren Auswirkungen wiederum simuliert darstellen.
An verschiedenen Bauteilen zeigte Dr. Belis, welche Ergebnisse die Simulationen erwarten lassen. Am Beispiel eines sehr komplexen Ventils, das aus einer ganzen Reihe von Werkstoffen hergestellt wird, war zu erkennen, dass zudem Möglichkeiten zur Verbesserung der Korrosionssituation bestehen. Auch hier zeigt die Simulation sehr schnell, wie sich Änderungen auswirken. Durch die Einpflege von weiteren Werkstoffen mit den dazu gehörigen Polarisationsdaten wird das System kontinuierlich erweitert. Diese Daten sind dann auch für andere Industriebereiche als die Luftfahrt verwendbar.
Abscheidung von Sondermetallen aus nicht-wässrigen Elektrolyten
Dr. Reinhard Böck gab einen Überblick über die Abscheidung von Sondermetallen aus nicht-wässrigen Elektrolyten als Einsatz für den Korrosionsschutz, wobei es sich bei den Elektrolyten um ionische Flüssigkeiten handelt. Auch wenn einige Ansätze zur Abscheidung aus nicht-wässrigen Elektrolyten seit vielen Jahren bestehen, hat bisher nur die Aluminiumabscheidung erste industrielle Anwendung gefunden. Die ionischen Flüssigkeiten bieten durch die gute Handhabbarkeit die derzeit besten Aussichten zur Abscheidung von Sondermetallen wie Aluminium, Titan, Tantal oder Niob. Der Bedarf ist vor allem in der Medizintechnik sowie der Luft- und Raumfahrt besonders hoch.
Außer den klassischen ionischen Flüssigkeiten bieten die Systeme, bei denen aus organischem Salz und einer Metallverbindung durch Mischen ein Elektrolyt entsteht, ein hohes Einsatzpotenzial. Diese haben den großen Vorteil, dass die Metallgehalte in diesem Fall deutlich höher als bei klassischem Lösen in ionischer Flüssigkeit sind. Bei diesen Systemen können durch Erhöhung der Temperatur häufig die Viskosität und Leitfähigkeit erhöht werden. Allerdings muss mit diesen Elektrolyten in der Regel in Inertgas gearbeitet werden, da die Metallsalze sehr reaktiv sind.
Neuere Arbeiten befassen sich auch mit der Zugabe von Additiven, um die Eigenschaften des Elektrolyten oder der Abscheidung zu modifizieren. Vorteile in Bezug auf die Rauheit der Schicht lassen sich durch Anwendung von Pulsstrom erzielen. Im günstigen Fall können damit beispielsweise sehr weiche und geschlossene Aluminiumschichten auf Stahl abgeschieden und anschließend auch anodisiert werden. Ein großes Problem ist allerdings die Vorbehandlung, da auf vollkommene Wasserfreiheit geachtet werden muss; bisherige Reinigungsverfahren werden jedoch ausschließlich mit wässrigen Verfahren durchgeführt. Vorteilhaft ist, dass mit löslichen Aluminiumanoden bei annähernd gleicher Elektrodenausbeute gearbeitet werden kann.
Derzeit ist es noch nicht gelungen, geschlossene Titanschichten zu erzeugen. Probleme bereiten die Beständigkeit der Elektrolyten, die Art der Ausgangsstoffe oder auch das Arbeiten mit unlöslichen Anoden. Etwas günstiger ist die Situation bei Tantal und Niob, wodurch die Abscheidung von Legierungen mit Aluminium möglich sein könnte.
REACh und Korrosionsschutz
Den Einfluss von REACh auf die Zukunft des Korrosionsschutzes beleuchtete der Vortrag von Dr. Christoph Werner. Er stellte eine Untersuchung zu Passivierungen ohne Kobalt vor. Im ersten Ansatz der Untersuchungen wurden ausgezeichnete Ergebnisse erzielt, sowohl bezüglich der Schichteigenschaften als auch der Anwendungen im Abscheideprozess.
Die ersten technischen Einsätze in der Praxis zeigten dagegen deutliche Unterschiede in der Bewertung: von vollkommen zufrieden bis absolut unzufrieden. Probleme ergaben sich beispielsweise daraus, dass Fehler in der Zinkschicht wesentlich stärker zutage traten oder ein zu hoher Glanzgrad entstand, der nicht akzeptiert wurde. Eine weitere Eigenschaft ergab sich aus der Orientierung der Passivschicht, die in der Folge das Aussehen und die Korrosionsbeständigkeit verändert.
Da diese Resultate nicht ohne weiteres erklärbar sind, wurde mithilfe der Literatur und eigenen weiterführenden Tests das neue System beispielsweise in Anlehnung an DIN EN 15205 näher untersucht. Dabei wurde deutlich, dass die Art des Fehlers, die Art der Schichtmorphologie oder die Art des Angriffmediums das Verhalten drastisch verändern.
So zeigte es sich, dass bei einer Testmethode (Rochestertest) bei den Passivierungen mit Kobalt geringe Mengen an Chrom(VI) im Salzsprühtest erzeugt werden. Diese können – entsprechend den konventionellen Chromatierungen – Defektstellen repas-
sivieren. Befindet sich dagegen kein Kobalt in der Passivierung, so entfällt dieser Mechanismus. Eine Lösung des Problems stellt die Verwendung von Versiegelungen oder Nachtauchlösungen dar. In beiden Fällen können Oberflächendefekte ausgebessert werden und so ein Versagen der Schicht unterbunden oder zeitlich stark verzögert werden.
Fazit
Die DGO hat mit der Auswahl des Themenkreises um Korrosion und Korrosionsschutz eines der interessantesten Themen der Oberflächentechnik angeboten. In den Vorträgen wurden mit den galvanischen Beschichtungen und Lackierungen die meistverwendeten Systeme angesprochen und neue Entwicklungen aufgezeigt. Ganz besonders interessant und für die Fachleute entlang der gesamten Prozesskette zur Herstellung von korrosionsbeständigen Bauteilen interessant, waren die Diskussionen über Korrosionsprüfungen. Hierüber wird seit Jahren in allen Bereichen der Oberflächentechnik heftig diskutiert. Die große Zahl an Varianten zur Prüfung der Korrosionsbeständigkeit, wie sie beispielsweise in der Automobilindustrie üblich sind, zeigt die Notwendigkeit, neue und einheitliche Untersuchungsmethoden zu schaffen. Hierzu wurden mögliche Ansätze gezeigt, die auf jeden Fall ein deutlich größeres Publikum zur Tagung gerechtfertigt hätten.

Verschärfte Nickelkorrosion findet unter Eisenpartikeln statt
Quelle: Engelking, VW

Ergebnisse der Langzeitauslagerung von Zinküberzügen in unterschiedlichen Klimaten, bei denen die Unterschiede im maritimen Klima deutlich werden
Quelle: Heyn
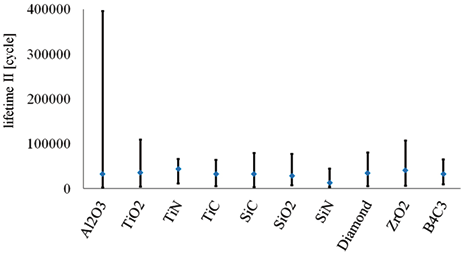
Aluminiumoxid und Titandioxid weisen als eingebaute Nanopartikel die höchsten Lebensdauern auf
Quelle: Song

Beispiel für Korrosionsschäden an Winkraftanlagen
Quelle: Lichtenstein

Stachelige Zinkoxide in PTU eingebettet
Quelle: Landau
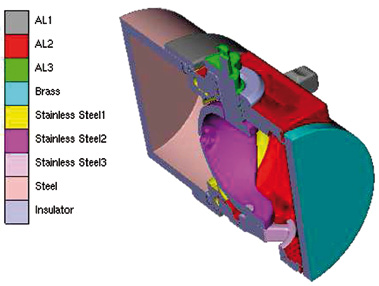
Beispiel für die Vielzahl der verbauten Werkstoffe an einem Ventil für ein Flugzeug
Quelle: Belis

Mit Aluminium (aus ionischer Flüssigkeit) beschichtete Stahlbleche sind sehr duktil bei guter Haftung und können zudem anodisiert werden (rechts)
Quelle: Böck