Elektrisches Fliegen ist keine Vision mehr
Elektrisch fliegen ist längst keine technologische Vision mehr, sondern machbar. Hersteller von Kleinflugzeugen, wie etwa Electric Aircraft aus den USA, Pipistrel aus Slowenien oder Yuneec aus China, träumen bereits vom Elektroauto der Lüfte. Die Pläne sind kühn: In Zukunft sollen nicht nur Elektrokleinflugzeuge sondern auch große Passagiermaschinen mit sauberem Strom abheben. Auch in Bayern ist man ganz vorne mit dabei, wenn es um die ersten Flugzeuge mit hybridem Elektroanbtrieb geht. Ein Team der zentralen Siemens-Forschung Corporate Technology in Erlangen arbeitet in einer Kooperation mit Airbus daran, die Vision vom elektrischen Fliegen wahr werden zu lassen.
Bayern Innovativ (B. I.) sprach auf dem Symposium Material Innovativ 2016 mit Dr. Mykhaylo Filipenko aus dem eAircraft-Team der zentralen Siemens-Forschung Corporate Technology der Siemens AG in Erlangen über die nächste Generation des Fliegens und wie wir bald reisen könnten.
B. I.: Die Luftfahrt wird elektrifiziert und begibt sich damit auf eine Reise in die Zukunft. Wann glauben Sie, Ihr Ticket für einen Flug mit Elektroantrieb von München nach Paris lösen zu können? Ist der Durchbruch in der zivilen Luftfahrt schon in Sicht?
Dr. Filipenko: Hybride Elektroantriebe werden in den nächsten Jahren bei zwei- und viersitzigen Flugzeugen, im nächsten Jahrzehnt auch bei 10- bis 20-sitzigen Flugzeugen zum Einsatz kommen. Wir rechnen damit, dass 2035 auch Regionalflugzeuge mit 60 bis 100 Passagieren mit hybriden Elektroantrieben an den Start gehen. Natürlich haben wir noch einen langen Weg vor uns und müssen das eine oder andere technologische Problem lösen. Auf jeden Fall gibt es keine physikalischen Gesetze, die wir brechen müssten, um an dieses Ziel zu kommen. Für mich als Physiker ist das schon mal 50 Prozent der Miete.
B. I.: Elektroflugzeuge sind ein zentrales Element Ihrer Forschung für die Zukunft der Luftfahrt. Welchen wegbereitenden Grundstein hat hier die automobile e-Mobility gelegt?
Dr. Filipenko: Die Entwicklung eines Umrichters beziehungsweise eines Motors nimmt einige Jahre in Anspruch. Während wir unseren eigenen Motor speziell für Fluganwendungen entwickelt haben, wollten wir parallel dazu auch Erfahrung bei der Elektrifizierung von Flugzeugen sammeln. Ein Elektromotor ist zwar immer ein Elektromotor, aber die Anforderungen bei Flugzeugen unterscheiden sich schon deutlich von denen bei Bahnantrieben, wo Siemens schon seit vielen Jahrzehnten Know-how-Träger ist. Hinsichtlich Leistung und Gewicht kommen tatsächlich Komponenten aus dem Automobilbereich am Nächsten. Bei den ersten Flugzeugen, die wir in die Luft brachten – wie die DA36-eStar von Diamond Aircraft – haben wir für den Zusammenbau des Antriebsstranges Motoren aus der Automobilbranche verwendet. Heute nutzen wir Umrichter von der Siemens Einheit eCar, da diese über ein sehr gutes Leistungsgewicht verfügen und sehr gut zu unseren Motoren passen.
B. I.: Bis 2050 soll die europäische Luftfahrt laut EU-Zielsetzung ihren Kohlendioxidausstoß um 75 Prozent reduzieren, die Stickoxidemissionen um 90 Prozent und den Lärm um 65 Prozent. Das geht nur mit radikal neuen Technologien. Welchen Beitrag können innovative neue Materialien für elektrisches Fliegen und die Einhaltung der CO2- und der Lärmreduktion leisten?
Dr. Filipenko: Innovative, neue Materialien sind wie in vielen anderen Bereichen auch hier der Schlüssel zum Erfolg. Während etliche Konzepte, wie man eine elektrische Maschine baut, schon lange bekannt sind und von vielen innovativen Firmen bis weit an die Grenze des Machbaren getrieben wurden, entdeckt man bei neuen Materialien immer wieder an der ein oder anderen Baustelle die Möglichkeit, mal zehn, mal 20 Prozent mehr Leistungsdichte herauszuholen. Das hört sich zwar zunächst nach nicht so viel an – insgesamt kommt aber schon einiges zusammen.
B. I.: Effizienz durch Leichtbau heißt die Maxime: Welche Rolle spielen hier ultraleichte Faserverbundstrukturen oder additiv gefertigte Strukturen?
Dr. Filipenko: Auch hier kann man sagen, dass sich bei unseren Maschinen Gewichtseinsparungen durch Faserverbundstrukturen erzielen lassen. Wie viel genau und an welcher Stelle werden wir in Zukunft sehr exakt unter die Lupe nehmen. Potenzial ist auf jeden Fall da.
B. I.: Wie will man den Herausforderungen Energiedichte-Optimierung und Reichweitensteigerung begegnen?
Dr. Filipenko: Wir arbeiten an der Leistungsdichte des elektrischen Antriebs, der die elektrische Energie beziehungsweise chemische Energie in mechanische umwandelt. Für die Optimierung der Leistungsdichte unserer Maschinen setzen wir insbesondere auf die Softwaretools, die bei Siemens entwickelt wurden. Damit kann man beispielsweise die Geometrie von Bauteilen so optimieren, dass sie möglichst wenig wiegen. Nicht zuletzt dadurch ist es uns gelungen, einen Weltrekord-Elektromotor zu entwickeln, der bei einem Gewicht von nur 50 Kilogramm rund 260 Kilowatt elektrische Dauerleistung liefert – fünfmal so viel wie vergleichbare Antriebe.
B. I.: Welchen Mehrwert erkennen Sie in der Netzwerktätigkeit von Bayern Innovativ vor dem Hintergrund neuer Fertigungstechnologien?
Dr. Filipenko: Bei meinem Vortrag auf dem Symposium Material Innovativ habe ich sehr positive Erfahrungen gemacht. Auf meinen Folien waren einige Materialien aufgeführt, die noch nicht existieren, aber für uns vorteilhaft wären. Unmittelbar nach dem Vortrag wurde ich von Experten aus dem Publikum hinsichtlich möglicher Materialentwicklungen in die jeweilige Richtung angesprochen. Besser kann es beim Netzwerkaufbau nicht laufen.
- www.bayern-innovativ.de
Elektrisches Fliegen – Vision und Umsetzung
Schon 2011 sorgten die Forscher um Frank Anton und sein Team der zentralen Siemens-Forschung Corporate Technology in Erlangen gemeinsam mit der Airbus Group und Diamond Aircraft für eine Weltpremiere, als sie das erste Flugzeug mit einem hybriden Elektroantrieb in die Luft brachten. Im Jahr 2013 flog dieses Flugzeug dann mit einem verbesserten Antriebsstrang. Damals erreichte der Elektromotor zwar schon ein ebenfalls bis dato unerreichtes Leistungsgewicht von knapp fünf Kilowatt pro Kilogramm, lieferte aber nur 60 Kilowatt Dauerleistung – das ist allenfalls genug Leistung für einmotorige Sportflugzeuge. Gemeinsam mit Airbus arbeitet Siemens jetzt daran, die Vision vom elektrischen Fliegen wahr werden zu lassen. Seit 2013 gibt es eine Kooperationsvereinbarung: Siemens beschäftigt sich dabei vor allem mit neuen elektrischen Antriebssträngen, während Airbus neue Luftfahrtzeugkonzepte entwickelt. Und schon 2035 könnte es die ersten 60- bis 100-sitzigen Flugzeuge mit hybridem Elektroantrieb geben – wenn es den Ingenieuren gelingt, noch leistungsstärkere Elektromotoren mit möglichst geringem Gewicht zu entwickeln.
Dr. Mykhaylo Filipenko
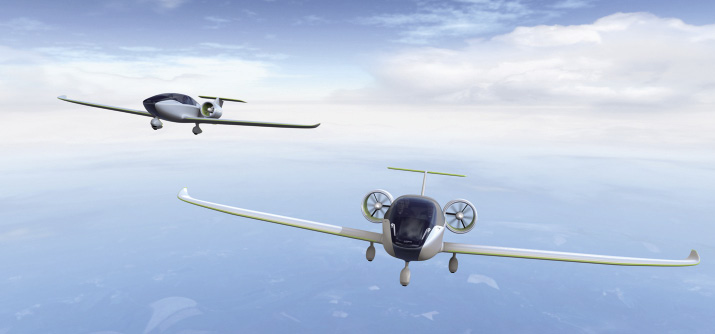
Der E-Fan Prototyp von Airbus wiegt 600 Kilogramm, ist 6,7 Meter lang und verfügt über eine Flügelspanne von 9,5 Meter. An Bord sind zwei Motoren vorhanden, die jeweils mit leistungsstarken Lithiumionenakkus angetrieben werden. Im Schnitt reist der Flieger mit 160 km/h; die Maximalgeschwindigkeit beträgt 220 km/h (Bildquelle: Airbus Group)