Mit dem Erwerb einer Eisengießerei in Nürnberg-Mögeldorf 1891 legten die Brüder Georg und Christian Decker den Grundstein der heutigen Decker Anlagenbau GmbH. Die Herstellung von Teilen aus Gusseisen stand in den ersten 70 Jahren im Vordergrund; die Aufnahme der Produktion von Elektrostahl (1927) und des Sphärogusses (1956) oder die Mechanisierung der Formerei mit vollständigem Recycling des Formsands zeigen, dass das Unternehmen innovativen Neuerungen gegenüber aufgeschlossen war. Die Suche nach Verbesserungsmöglichkeiten könnte auch den Ausschlag dafür gegeben haben, dass 1961 ein Unternehmen zur Herstellung von Beizanlagen übernommen und eingegliedert wurde.
Die Übernahme entwickelte sich zu einem wachsenden Geschäftszweig, dem mit der Auslagerung der Produktionsstätte nach Burgthann 1979 Rechnung getragen wurde. Neben den Beizanlagen, die anfänglich im Vordergrund standen, folgte bald die Ausdehnung auf weitere nasschemische Verfahren, insbesondere die galvanotechnische Beschichtung, das Durchführen von Beizverfahren für Buntmetalle oder das Reinigen von Metallteilen in einer mechanischen Fertigung. Eine erneute Erweiterung der Produktionskapazitäten folgte 1988 mit dem Umzug nach Berg in der Oberpfalz, nachdem 1982 der Gießereibetrieb in Nürnberg stillgelegt worden war. In dieser Zeit stieg der Bedarf nach besonders umweltfreundlichen Anlagen. Die Entwicklungen der Decker Anlagenbau führten dazu, dass 1988 die erste abwasserfreie Beizanlage in Betrieb genommen werden konnte.
Mit Übernahme der Gesellschaftsanteile der Decker Anlagenbau GmbH durch die Fuchs & Söhne GmbH wurde zusätzlicher Schwung in die Geschäftsaktivitäten gebracht. Die stetig steigende Nachfrage nach Halbleiterrohlingen brachte erste Kontakte zur Siliziumindustrie. Hieraus entstanden beispielsweise Anlagen zum Recycling von Siliziumgranulat, Anlagen zum Ätzen von Silizium, die unter anderem bereits 2007 nach China ausgeliefert wurden, Anlagen zum Reinigen von Siliziumrohprodukten sowie eine Anlage zur Vereinzelung von Wafern, die 2011 mit dem Intersolar Award ausgezeichnet wurde. Parallel dazu wurde zudem für Kunden im Automotive-Bereich gefertigt, wie etwa eine Großeloxalanlage für ein Zulieferunternehmen in 2011 oder eine Beizanlage mit vollautomatischer Be- und Entlade für einen namhaften deutschen Automobilhersteller. Als weiterer Technologiebereich wurde die Luftfahrt mit Rissprüfanlagen ausgestattet, sodass ein sehr breiter Kreis an Kundenbranchen abgedeckt wird.
Die Anlagen der seit 2007 in Berching mit nochmals vergrößerter Produktionsfläche fertigenden Decker Anlagenbau GmbH zeichnen sich durch ein hohes Maß an Individualität aus. Zahlreiche Neuentwicklungen, beispielsweise zum schonenden Transport von Siliziumwafern, zur Abgasreinigung oder zur Recyclingtechnik, wurden durch Auszeichnungen für umweltfreundliche Anlagentechnologien gewürdigt. Die Anlagen selbst reichen von Kleinanlagen mit wenigen Quadratmetern Standfläche bis hin zu hallenfüllenden Großanlagen für die nasschemische Bearbeitung oder Prüf- und Messeinrichtungen, wie sie für die Herstellung von Elektronikteilen oder Automobilkomponenten Anwendung finden. Diese breite Streuung der Verfahren, verbunden mit einer hohen Innovationskraft und einer hohen Anlagenqualität, sichern der Decker Anlagenbau ihre gute Akzeptanz bei Kunden weltweit.
Die gute Zusammenarbeit mit den Herstellern von Einzelkomponenten zeigte sich zur 125-Jahr-Feier des Unternehmens, die Anfang März in Berching stattfand. Lieferanten boten im Rahmen der Feier einen Einblick in deren Produkte und die Anwendungsmöglichkeiten in modernen Anlagen. Zahlreiche zufriedene Kunden griffen die hierbei vorgestellten Ideen und Möglichkeiten auf, aus denen sich in Zusammenarbeit mit den Fachleuten der Decker Anlagenbau neue Produktionseinrichtungen entwickeln können.
Anlagenbau im festlichen Rahmen
Galvanik-Tag
Geschäftsführer Robert Fuchs konnte zum Galvanik-Tag bei Decker Anlagenbau am 3. März im Rahmen der Jubiläumsfeier etwa 200 Besucher begrüßen. Er stellte einführend die Entwicklung der 125 Jahre währenden Aktivitäten des Unternehmens vor. Des Weiteren betonte er die Position von Decker als Sonderanlagenbauer: Jede Anlage ist an die Anforderungen des Kunden angepasst und ein Unikat. Ensprechend breit ist die Art der bisher gefertigten Anlagen, von der Kleinanlage bis zu Großanlagen. Dazu zählen unter anderem auch Anlagen zum Beizen von Aluminium mit anschließender Rissprüfung. Weitere Anwendungen liegen in der Halbleitertechnik oder der Glasverarbeitung. Decker fertigt hierfür alle Komponenten, von den Behältern über Transporteinrichtungen bis zur Abluftreinigung oder Trommeln. Bezüglich der Anlagenperformance werden Ressourcen- und Energieeffizienz, Betriebssicherheit und Produktionskosten berücksichtigt.
Robert Fuchs zeigte sich stolz, dass das Unternehmen seit 2004 ein Teil der Firmengruppe Fuchs ist. Fuchs ist vor allem im Bereich Hoch- und Ingenieurbau sowie Umwelttechnik tätig und breit aufgestellt.
Begrüßungsworte der Geschäftsleitung an die zahlreichen Gäste
Menschen – Organisation – Technik
Wolfgang Kohl, seit vielen Jahren im Zentralverband Oberflächentechnik e. V., ZVO, in verschiedenen Ressorts aktiv, gab als Festredner einen Einblick in die wichtige Einheit aus Menschen, Organisation und Technik, wobei er betonte, dass ein Unternehmen mit 125-jähriger Geschichte kaum Impulse benötigt. In seiner Arbeit hatte er erfahren, dass es besonders aufwendig war und ist, Neuerungen in Gang zu setzen, da Menschen Veränderungen stets mit einem erhöhten Aufwand in Verbindung bringen. Jeder Einzelne muss mit Willen zur Veränderung beitragen. Für Wolfgang Kohl kann daraus abgeleitet werden, dass das Veränderungsvermögen einer Unternehmung zum wichtigsten Erfolgsfaktor zählt. Eine gute Planung von Projekten ist für ihn dabei dringend geboten; dass dies in vielen Fällen nicht optimal ist, zeigt sich an der oftmals auftretenden Hektik gegen Abschluss von Projekten. Es empfiehlt sich deshalb, Zielvorgaben festzulegen und diese im Laufe des Projekts zu überprüfen und abzugleichen. Dabei müssen sich alle Beteiligten der regelmäßigen Kontrolle unterziehen und so vermeiden, scheinbarer Kompetenz zu entgehen.
Im Bereich des Anlagenbaus für die Oberflächentechnik sind das vor allem die Basisdaten für die Anlagenplanung, wie beispielsweise der Teilegrößen, Chargengröße, Verfahrensaufbau oder die rechtlich relevanten Rahmenbedingungen. Hindernisse entstehen häufig deshalb, weil die Zusammenstellung von Arbeitsteams für die Projektdurchführung nicht optimal ist oder zeitlich nicht optimal in Gang gesetzt wird. In der Oberflächentechnik macht sich eine optimierte Vorgehensweise besonders deshalb bezahlt, weil unterschiedliche Komponenten – Gleichrichter, Pumpen, Steuerungen – aufeinander abgestimmt und beim Betreiber der Anlage bestmöglich betrieben werden müssen.
Impulsvortrag zum Thema Der Kompetenzkreislauf in der Galvanik: wirksames Zusammenspiel Anlagenbauer – Kunde sowie Mensch – Maschine
Moderne Heiztechniken
Die Mazurczak GmbH ist einer der renommiertesten Hersteller von Heizungen für die Galvano- und Oberflächentechnik. Frank Pfeuffer gab einen Einblick in den Aufbau von modernen Elektroheizungen, bei denen hoher Wert auf die Sicherheit in Bezug auf Brandschutz, einen unkomplizierten Einsatz in Produktionsanlagen oder auch die Effizienz gelegt wird.
Die hauptsächlichen Energieverbräuche bei nasschemischen Prozessen, wie sie die galvanotechnische Abscheidung darstellt, liegen bei Gleichrichtern und Heizungen. Bei üblichen Werten für den Energieverbrauch im Bereich von 5 bis 10 Mio. kWh sind nach seiner Meinung in den letzten Jahren Einsparungen zwischen fünf und zehn Prozent durch den Einsatz modernster Heiztechnologie möglich geworden.
Vortrag Temperieren von Prozessflüssigkeiten in der Galvanotechnik – Elektrowärme versus Wärmetauscher von Frank Pfeuffer, Mazurczak GmbH
Elektroheizungen sind sicher und einfach zu bedienen sowie zu installieren. Weitere Vorteile sind die schnelle Ein- und Abschaltung. Durch Einbau über eine feste Verbindung kann die Sicherheit deutlich erhöht werden. Nachteilig ist die Tatsache, dass die Energiekosten langfristig weiter steigen werden. Bei Einsatz entsprechender Sensorik ist die Brandgefahr sehr gering, erfordert allerdings eine regelmäßige Kontrolle. Ergänzend sind seit einiger Zeit zur Erhöhung der Betriebssicherheit integrierte Abschaltsysteme erhältlich.
Ebenfalls bewährt ist das Heizen mit Austauschern, die neben der Betriebssituation Heizen das Kühlen ermöglichen. Um konstante Leistung zu garantieren, ist mehr Aufwand notwendig als bei Elektroheizungen. Zu berücksichtigen ist bei dieser Heizungsart die Erfordernis eines Temperaturunterschieds zwischen zu beheizendem Medium und dem Heizstoff. In der Regel sollte das Delta mindestens 15 K betragen. Bezüglich der Einrichtung ist der Aufwand deutlich höher; besonders günstig ist die Nutzung von Blockheizkraftwerken. Deutlicher Vorteil ist das vollständige Fehlen einer Brandgefahr. Trotzdem ist es zu empfehlen, Trockenschutzeinrichtungen vorzusehen, da bei fehlendem Medium ein Behälter durch den Tauscher geschädigt werden kann. Bei großem Wärmebedarf ist der Wärmetauscher im Vorteil, bei kleinen Wärmemengen die Elektroheizung.
Kondensationstrocknung
Wie Reinhold Specht einführend betonte, arbeitet das Verfahren der Harter GmbH zur Trocknung von nassen Teilen als geschlossenes System. Es findet also kein Austausch mit der Luft des umgebenden Produktionsbereichs statt. Eine weiterer Vorteil ist die hohe Konstanz, unabhängig von der Umgebungsatmosphäre. Das Ergebnis ist zudem eine fleckenfreie Oberfläche.
Reinhold Specht, Harter Oberflächen- und Umwelttechnik GmbH
Bei dem Verfahren der Harter GmbH wird mit entfeuchteter Luft gearbeitet. Diese wird durch Abkühlung der Luft erreicht, wobei die entnommene Wärme über eine Wärmepumpe zum Aufheizen der trockenen Luft verwendet wird. Die getrocknete Luft wird mit hoher Geschwindigkeit an den feuchten Oberflächen vorbeigeführt, nimmt dort Feuchtigkeit auf und wird anschließend dem Kondensationsteil der Trocknung zugeführt. Das System kann für unterschiedliche Anwendungen eingesetzt werden; derzeit wird es vor allem in der Oberflächentechnik, der Pharmazie und der Lebensmittelverarbeitung verwendet.
Enthalten die Teile sehr viel Feuchtigkeit, werden die Oberflächen beim Einfahren in den Trockner abgeblasen; so wird bereits ein großer Teil des Wassers entfernt. Als wichtiges Element ist ein gut schließendes Deckelsystem vorhanden. Vorteilhaft ist die Technologie besonders bei kleinen und gut aneinander haftenden Teilen, die als Schüttgut bearbeitet werden.
Mit dem System lassen sich gegenüber konventionellen Verfahren erhebliche Mengen an Energie von 70 bis 80 Prozent im Vergleich zu früher üblichen Umlufttrocknern einsparen. Das System wird deshalb unter anderem für die Trocknung von Rohren, die im Bund verarbeitet werden, oder auch für die Trocknung von Lacken verwendet. Bei der Trocknung von Schlamm, eine der ersten Anwendungen der Kondensationstrocknung, lassen sich Gewicht und Volumen deutlich vermindern. Die Tatsache der kontinuierlich steigenden Energiekosten macht den Einsatz der Kondensationstrocknung besonders attraktiv. Bei Betrachtung der Energiekosten amortisiert sich eine Anlage derzeit innerhalb von zwei Jahren.
Pumpen- und Filtertechnik
Pumpen und Filter für den nasschemischen Einsatz sind nach Aussage von Dr. Martin Renner individuelle Geräte, bei denen sich die verschiedenen Zustände der zu bewegenden Medien deutlich unterscheiden. Relevant sind die Verbindungsleitungen in Bezug auf Querschnitt und Länge zwischen Pumpe und Behälter sowie die notwendigen Strömungsgeschwindigkeiten. Die Wahl des Werkstoffs für eine Pumpe richtet sich nach dem angestrebten Preis für das Gerät oder die auftretenden Temperaturen im Einsatz. Bezüglich des Motors für die Pumpe spielen die verfügbaren Strom-Spannungswerte des Netzes sowie die Außentemperaturen eine Rolle. Zur Vermeidung von Korrosion werden gesamte Pumpen auch in Gehäuse gesetzt, wodurch allerdings höhere Aufwendungen für die Motorkühlung vorgenommen werden müssen. Bewährt hat sich ein Baukastensystem, das zu gesamten Pump-Filter-Systemen als Plattform aufgebaut wird.
Martin Renner (Mitte), Renner GmbH
In durchschnittlichen Galvanikbetrieben werden nach den Erfahrungen von Dr. Renner etwa 13 Prozent des gesamten Stroms für Pumpen verbraucht, woraus sich ein relativ hohes Interesse zur Verbesserung des Wirkungsgrades ableitet. Der Wirkungsgrad eines Pumpsystems weist ein Maximum sowie und eine abfallende Kurve für die Förderhöhe auf. Hieraus wird durch eine Optimierung der bestmögliche Einsatzpunkt für ein Pumpsystem ermittelt. Insbesondere ist zu berücksichtigen, dass Pumpen im Prinzip durch den Betrieb Wärme erzeugen, die wiederum durch Kühlen abgeführt werden muss – was oftmals übersehen wird. Ein weiteres Augenmerk sollte auf die Betriebsart gerichtet werden, wobei häufig Drossel- und Drehzahlregelung zur Verfügung stehen. Abschließend wies er darauf hin, dass Pumpen ab 2015 nach IEC3-Standard ausgeführt sein müssen. Derzeit werden Anstrengungen unternommen, den Filterwirkungsgrad durch Anwendung von Simulationsverfahren zu optimieren.
Galvanik-Gleichrichter
Gleichrichter sind wie viele andere Produktionseinrichtungen zunehmend individuelle Geräte, wie Thomas Mark einführend betonte. Deren Differenzierung richtet sich nach der Kühlungsart: Luft-, Öl/Wasser- und reine Wasserkühlung. Der ölgekühlte Gleichrichter ist der ursprüngliche Typ, der sich durch eine sehr effiziente Kühlung auszeichnet. Vollkommen gleichartig aufgebaut ist der Gleichrichter mit Öl/Wasserkühlung (Hybridlösung). Hierbei fällt Wasser an, das zur Heizung von anderen Einrichtungen verwendet werden kann. Bei reiner Kühlung mit Wasser durchfließt dieses metallische Komponenten des Geräts und gibt hierbei die Wärme ab.
Zu den neuesten Gleichrichtertypen zählen Schaltnetzteile, die sehr kompakt aufgebaut sind. Diese aus mehreren kleinen Einheiten zusammengesetzten Geräte werden häufig wassergekühlt. Bei einer Luftkühlung ist zwischen den verschiedenen Arten der Luftzufuhr zu wählen, die sich auf die Schutzart auswirken.
Thomas Mark (rechts), Munk GmbH
Kriterien für den Einsatz sind die Schein-, Wirk- und Blindleistung. Wichtig ist die Beachtung der Begriffe Schein-, Wirk- und Blindleistung. Insbesondere die Bezeichnungen Wirkungsgrad und cos phi werden oft miteinander in Bezug gebracht, was jedoch unrichtig ist. Der Wirkungsgrad ist der Quotient aus abgeführter zu zugeführter Wirkleistung. Dies hat nichts mit dem cos phi zu tun.
Bei der Restwelligkeit der unterschiedlichen Technologien ist zu beachten, dass Stelltrafogeräte und Schaltnetzteile konstant niedrige Welligkeiten aufweisen. Der Thyristorgleichrichter hat eine natürliche veränderbare Welligkeit. Mithilfe von Glättungsmaßnahmen werden ebenfalls vergleichbar niedrige Welligkeiten, wie es beispielsweise bei Hartchromgeräten gewünscht ist, erreicht.
Schließlich wies Thomas Mark darauf hin, dass durch die ausreichende Dimensionierung der Zuleitungen enorme Mengen an Energie in Form von Wärme eingespart werden können. Hier ist besonders darauf zu achten, dass der Spannungsabfall der Zuleitung 0,5 Volt nicht übersteigt.
Gut aufgestellt in die Zukunft
Die Decker Anlagenbau GmbH hat mit ihrem breiten Spektrum an Anlagenarten, der hohen fachlichen Kompetenz der Mitarbeiter und einer guten Auswahl an zuverlässigen Zulieferanten eine gute Basis für die Zukunft. Das Unternehmen hat sich auf dem globalen Markt mit individuellen Anlagen aus dem Bereich der nasschemischen Werkstoffbearbeitung gut platziert, sodass auch in Zukunft hochqualitative Produktionsanlagen aus der Oberpfalz überall auf der Welt anzutreffen sein werden.
- www.decker-anlagenbau.de
Decker freute sich über die Vielzahl interessierter Gäste
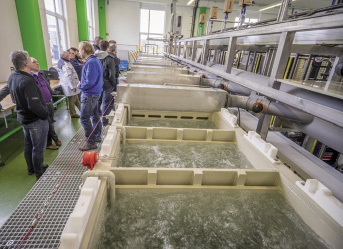
Phosphatierautomat, 24 x 16 m, mit Seitenläufer, Taktzeit 15 Min., Durchsatz 116 Teile/WT, mit teilautomatischer Regeneration für das Phosphatierbecken, im Probebetrieb mit Wasser
Text zum Titelbild: Elektropolieranlage, 4,5 x 1,8 m, Warendurchsatz 1 m/min, Anlage für Nickel-Wolframband zur späteren Beschichtung mit Nanopartikeln für einen führenden deutschen Spezialisten für chemische Beschichtungstechnologien