Beim fünften Symposium Angewandte Elektrochemie in der Materialforschung am Fraunhofer-IKTS, Dresden, am 24. und 25. November 2016 standen erneut die anodischen Oxidschichten im Fokus der 2005 begonnenen Tagungsreihe. Neben klassischen Feldern der Anodisation von Leichtmetallen als Korrosions- oder Verschleißschutz sind nanotechnologische Arbeiten, bei denen Anodisierschichten als Template oder Membranen eingesetzt werden, ein zunehmender Trend. Des Weiteren gewinnt die plasmaelektrolytische Anodisation immer mehr an industrieller Akzeptanz. Die Anwendungsgebiete des Anodisierens haben sich auch aufgrund der stattgefundenen Entwicklungen deutlich erweitert, bieten zugleich aber noch weiteres Potenzial aufgrund der vielfältigen Eigenschaften. Die Beiträge reichten von der Grundlagenforschung bis zu anwendungsorientierten Ansätzen und boten Einblicke in Messtechniken sowie Herstellungsverfahren. Das Angebot zu einem interessanten Überblick über Oxidschichten, das unter der Leitung von Dr. Michael Schneider stand, hatten 50 Fachleute und sechs ausstellende Unternehmen wahrgenommen.
Dr. Michael Schneider
Anodische Oxidbildung
Dr. Lohrengel hatte den Titel seines Vortrags über die anodische Oxidbildung durch den Hinweis erweitert, dass einiges zur Sauerstoffentwicklung und Metallauflösung im Rahmen der Oxidschichtbildung bekannt ist und einiges noch im Detail erforscht werden wird. Bekannt ist, dass Aluminiumoxid in zwei Schritten über die Bildung von Aluminiumhydroxid und Umwandlung in Oxid erzeugt wird. Dabei entsteht Aluminiumoxid mit einer der höchsten Beständigkeiten gegen Durchschlagen mit Feldstärken bis 106 V/cm; ein Grund, weshalb Aluminiumoxid sehr gut zur Herstellung von Kondensatoren zur Energiespeicherung geeignet ist. Die Oxideigenschaften sind denen von Titan oder Tantal ähnlich.
Beschreiben lässt sich die Entstehung der Oxidschicht mit Hilfe der Hochfeldgleichung. Diese sollte eigentlich auch für andere Metalle anwendbar sein. Allerdings treten häufig störende Nebenreaktionen auf, wie beispielsweise bei Chrom. Zu betrachten sind in diesem Zusammenhang verschiedene Aspekte der Sauerstoffentwicklung. Dazu zählen die Sichtbarkeit der Sauerstoffentwicklung, die Tatsache, dass Sauerstoffentwicklung nur auf Oxiden erfolgt, oder das Ausbleiben einer sichtbaren Sauerstoffentwicklung bei Ventilmetallen.
Mit etwas Aufwand verbunden ist die Erklärung des Oxidationsprozesses, da für die Oxidation Sauerstoff durch das Oxid diffundieren müsste und das Oxid eine elektrische Leitung aufweisen sollte. Um die Sauerstoffreaktionen an Ventilmetallen zu untersuchen, werden beispielsweise große Metalloberflächen oder sehr empfindliche Analyseverfahren für Sauerstoff benötigt. Mit deren Hilfe ist beispielsweise bei Tantal festzustellen, dass etwa 4 % der Gesamtladung in Tantaloxid umgewandelt wird und Sauerstoffentwicklung nur erfolgt, wenn Oxid vorhanden ist.
Des Weiteren zeigt sich bei der Oxidbildung auf Metallen wie Eisen, Nickel oder Chrom, dass das Hochfeldgesetz simuliert werden kann. Auch hierbei erfolgt die Sauerstoffentwicklung nur an Oxiden und die Sauerstoffbindung in Oxid liegt in der Regel bei etwa 5 % . Die Kristallform der entstandenen Oxide sind Spinelle wie sie als Chromit (Cr2O3 FeO) oder Gahnit (Al2O3 ZnO) in der Natur vorkommen.
TEM-Untersuchungen an Barriereschichten
Dr. René Hübner stellte Arbeiten zur Untersuchung von Oxidschichten mit Hilfe der Transmissionselektronenmikroskopie (TEM) am Helmholtz-Zentrum Rossendorf in Dresden vor. Diese Technologie ermöglicht Auflösungen bis etwa 0,1 nm, wobei jedoch eine optimale Probenpräparation ausschlaggebend für die Durchführung von aussagekräftigen Untersuchungen ist.
Für die Untersuchungen wurde eine Aluminiumschicht auf einen Siliziumwafer aufgesputtert und anodisiert. Als entscheidendes Kriterium für die Untersuchung im TEM gilt die Durchlässigkeit für Elektronen, das heißt eine geringe Dicke der Proben, die beispielsweise durch chemisches Dünnen erfolgen kann. Zur Interpretation der entstehenden Aufnahmen müssen vor allem Streueffekte bewertet werden. Schattierungen ergeben sich zudem durch die Anordnung der Atome, also insbesondere Unterschiede zwischen optimal aufgebauten Kristallen und Kristalldefekten. Insbesondere ist die Bewertung der unterschiedlichen Eigenschaften der Elektronen (Phase, Amplitude) zu berücksichtigen.
Ein Charakteristikum ist, dass die Dicke der Oxidschicht an Korngrenzen vergleichbar ist mit der an einer Kornfläche, Korngrenzen also keinen markanten Einfluss auf das Oxidwachstum ausüben. Die Analysen zeigen beispielsweise, dass der Ionisationsgrad des Aluminiums im Oxid geringfügig variiert und die Oxidschicht Poren mit Durchmessern von wenigen Nanometern besitzt. Abhängigkeiten der Oxidschichtdicke zeigten sich durch die Wahl des Anodisierstroms, beispielsweise den Kennwerten von pulsierendem Strom.
Korrosion von Ventilmetallen
Prof. Achim-Walter Hassel befasste sich mit der Korrosion von Ventilmetallen, die im vorliegenden Fall als Ersatzwerkstoff für Implantate aus Platin im Hörsystem eingesetzt werden sollen. Hier werden an die Platinkörper Spannungen von bis zu 8 V angelegt, die wiederum zur Oxidation und Korrosion des Platins führen. Als in Betracht kommende Ventilmetalle wurden Tantal, Niob, Titan, Wolfram und Aluminium auf deren Eigenschaften untersucht.
Bei Tantal konnte eindeutig nachgewiesen werden, dass das Metall nur elektrochemisch aufgelöst wird. Dabei wird nahezu nur Oxid gebildet und kein Tantal (als Tantalion) freigesetzt. Die Umsetzung zu Oxid erfolgt zu mehr als 99,8 %.
Bei Niob ist die Auflösung höher als bei Tantal, wobei das Verhalten des Metalls mit dem von Tantal vergleichbar ist. Die Auflösung des Titans lässt sich in Ionenstrom und Elektronenstrom auftrennen. Ab einer Spannung von etwa 4 V tritt ein merklicher Elektronenstrom auf, der zur Sauerstoffbildung (erkennbar an Gasblasen) führt.
Bei Wolfram zeigt sich eine höhere Metallauflösung mit erkennbarem Abtransport von Wolfram in den Elektrolyten. Gleiches gilt für Aluminium. Hierfür wurde eine Schichtdicke von 1,6 nm pro Volt als Grenze für die akzeptable Anodisationsspannung gefunden; bei darüber liegenden Werten wird Aluminium freigesetzt.
Tantal ist den Untersuchungen zufolge perfekt und Niob nahezu perfekt für den Einsatz als Implantatmetall im Hörsystem.
Einfluss von Oxidfilmen auf die Haftfähigkeit von Klebungen
Im Flugzeugbau wird neben dem Nieten zunehmend auf Kleben als Verbindungstechnologie gesetzt. Dabei hat die Struktur des Aluminiumoxids einen deutlichen Einfluss auf die Haftung der Verklebungen, insbesondere ist eine optimale Porenstruktur des Oxids ausschlaggebend, wie Shoshan Abrahami einführend betonte. Erwartungsgemäß ändert sich die Struktur des Oxids mit den unterschiedlichen Arten an Elektrolyten wie Schwefelsäure, Weinsäure oder Phosphorsäure. Darüber hinaus hat die Temperatur des Elektrolyten für die Haftung einen erkennbaren Einfluss. In Untersuchungen der Vortragenden wurde die Haftung durch Verkleben von zwei Aluminiumblechen bewertet. Deutlichen Einfluss hat der Anteil an Hydroxid, das an der Oberfläche angelagert wird.
Weitere Kriterien für die Haftung der Verklebung sind die Länge der Oxidporen sowie der Porendurchmesser. Hierbei ist eine Zunahme der Haftung mit dem Porendurchmesser und der Porenlänge festzustellen. Die Elektrolyttemperatur führt zu einer Zunahme der Rauheit der Oxidschicht, die ebenfalls eine Verbesserung der Klebehaftung bewirkt.
Zusammenfassend wurden drei Einflussgrößen für die Qualität der Verklebung beziehungsweise der hierbei relevanten Haftung ermittelt: Oberflächenchemie, Porendurchmesser und Rauheit der Oxidoberfläche.
Hochviskose Elektrolyte
Wie Lissy Peter einführend erläuterte, besteht Bedarf an hochviskosen Elektrolyten zur Entwicklung eines speziellen Bearbeitungsverfahrens für Aluminiumbauteile. Ziel des neuen Verfahrens ist eine lokale Vorbehandlung an einem größeren Aluminiumbauteil, um beispielsweise Schnittkanten oder Klebeflächen zu bearbeiten. Derzeit wird partiell mit Abdecken oder mit Anodisierstiften gearbeitet. Bei dieser Methode sind der mögliche Kontakt mit der Anodisierflüssigkeit sowie die beschränkte Fläche für die Bearbeitung nachteilig.
Für das neue Verfahren wurde eine Klebefolie entwickelt, die alle Komponenten für die Anodisierung enthält, also Elektrolyt, Kathode und die erforderliche Stromzuführung. Aufgrund der geforderten hohen Viskosität (um das Fließen des Elektrolyten zu vermeiden) ist die Elektrolytleitfähigkeit wesentlich höher, was jedoch durch den geringen Abstand zwischen Anode und Kathode ausgeglichen wird. Den Effekt dieses Unterschieds hat Lissy Peters mittel EIS und TEM untersucht.
Ein Stromdichteverlauf deutet auf eine Limitierung des Stofftransports hin. Im TEM zeigen die Schichten zwischen konventioneller und Klebebandanodisierung keinen merklichen Unterschied. Lediglich die Schichtdicken bei längeren Anodisierdauern sind bei der konventionellen Anodisierung höher. Die Untersuchungen zur Schichtdicke und Schichtmorphologie deuten darauf hin, dass sich bei der Tape-Anodisierung in der Oberfläche Ablagerungen anreichern.
Mit Hilfe von Zugversuchen wurde die Eignung des neuen Anodisierverfahrens für den praktischen Einsatz beim Kleben untersucht und bestehende Unterschiede ermittelt. Hier führte die Klebebandtechnik zu sehr guten Ergebnissen, die relativ nahe an die der konventionellen Anodisierung heranreichen.
Nanoporöses Aluminiumoxid
Einen besonders interessanten Aspekt von Aluminiumoxid stellte Dr. Petra Göring vor. Ihr gelingen die Herstellung und multifunktionale Anwendungen von nanoporösem Aluminiumoxid und Siliziumoxid, wobei hochgeordnete poröse Materialien im Vordergrund stehen. Die Materialien lassen sich mit unterschiedlichen Porendurchmessern und großen Längen (das heißt mit hohen Aspektverhältnissen) erzeugen. Während bei Aluminium die natürlichen Eigenschaften von anodisch hergestelltem Aluminiumoxid genutzt werden können, muss bei Silizium zur Herstellung eines Oxids mit definierten Poren eine Vorstrukturierung durchgeführt werden. Bei Silizium sind die nano- und mesoporösen Werkstoffe eher schwarmmartig, während die makroporösen Strukturen sehr regelmäßig sind. Letzteres erfolgt auf Basis eines Lithographieprozesses. In Silizium können mit diesem Verfahren Membranen mit Dicken von einigen zehn Mikrometern zuverlässig hergestellt werden.
Bei Aluminium lassen sich drei unterschiedliche Porenanordnungen erzeugen. Die entsprechende Membran entsteht, wenn die Oxide zum Bearbeitungsabschluss vom Aluminiumsubtrat abgehoben werden. Die hochstrukturierte Porenstruktur wird durch mehrere Prozessschritte (Anodisieren, Auflösen, erneut Oxidieren) hergestellt. Die Anodisationszeit ist bei diesem Prozess der entscheidende Arbeitsparameter.
Die Porengrößen erlauben die Herstellung von Membranen für die Diffusionstrennung, wobei die Stärke der gewünschten Diffusion beziehungsweise die Größe der zu trennenden Teile über die Porendimensionen einstellbar ist.
Anwendungen sind vor allem in der Biomedizin zu finden, beispielsweise zur Trennung von biologischen Strukturen, Zellen oder Wirkstoffen. Speziell für einen Kunden wurde auf Basis von mikroporösem Silizium ein 3D-Sensor entwickelt, aber auch eine Membran für eine Brennstoffzelle. Aluminiumkörper mit homogenen Strukturen eignen sich zur Herstellung von Folien (z. B. Antireflexfolien). Für diese Anwendung wird die Porenstruktur über Walzen oder Pressen in Kunststoff übertragen. Ein Entwicklungsprozess befasst sich mit der Herstellung von selbstreinigenden Strukturen, ebenfalls durch Übertragung von regelmäßigen Oberflächenmikrostrukturen auf einen Grundwerkstoff.
Die Herstellung der Poren eignet sich im Falle von Silizium aber auch, um Poren durch Lift-oft zur Erzeugung von ultradünnen Siliziumwafern zu nutzen. Herausforderung ist die Gewährleistung der mechanischen Stabilität der Strukturen sowie der mikroskopischen Struktur über den Herstellungsprozess hinweg.
Energieausbeute beim Hartanodisieren
Bei Herstellen von anodischen Oxidschichten auf Aluminium für den funktionellen Einsatz - das sogenannte Hartanodisieren - wird durch Kühlen des Elektrolyten die Rücklösung an Oxid verringert. Die Oxidschichten weisen daher ein geringeres Porenvolumen auf als Oxidschichten, die bei höheren Elektrolyttemperaturen erzeugt werden. Allerdings führt diese Technologie zu einem hohen Energieverbrauch bei der Produktion, wie Stefan Kölle einführend darlegte.
Als mögliche Handlungsfelder zur Energieeinsparung bieten sich die Elektrolytkühlung, -umwälzung oder auch die Elektrolyttemperatur und -zusammensetzung. Bei der Betrachtung der Wirkung einer Kühlung ist zu berücksichtigen, dass die Elektrolyttemperatur nicht mit der Temperatur an der Teileoberfläche übereinstimmen muss und somit der Zusammenhang zwischen Elektrolyttemperatur und den Eigenschaften der Oxidschicht nicht direkt ableitbar sein muss. Zur Klärung des Zusammenhangs wurden Messung der Härte bei unterschiedlichen Tiefen der Schicht sowie der Temperatur an der Oberfläche durchgeführt.
Für funktionelle Oxidschichten sind Härten von mehr als 400 HV gefordert. Daraus entstand ein Verfahren, bei dem mit höherer Temperatur und mit pulsierenden Strömen gearbeitet wird. Die Eigenschaften der daraus entstandenen Schichten entsprechen denen des konventionellen Hartanodisierens (Härte, Verschleiß), wogegen die Kosten für Energie in der Größenordnung von 40 % gesenkt werden können. Darüber hinaus kann die Energie durch Einsatz von entsprechenden Technologien zum Heizen eingesetzt beziehungsweise im Winter auf eine Kühlung verzichtet werden.
Selbstorganisierendes Anodisieren auf Titan
Robert Hahn stellte hochgeordnete Titanoxidschichten und deren Anwendungen vor. Titan kommt z.B. Für Solarzellen, Photokatalyse oder biomedizinische Produktionsverfahren zur Anwendung. Ähnlich wie bei Aluminium kann auf Titanoberflächen eine Porenstruktur mit hoher Ordnung erzeugt werden. Die Abmessung der sich bildenden Röhren liegt im Nanometerbereich und damit in der Größenordnung von sogenannten Nanotubes.
Durch die hohe Ordnung werden die elektrochemischen Eigenschaften des Systems aus Oberflächen und angrenzendem Elektrolyten verändert. Die Durchmesser können gezielt zwischen 10 und 800 nm Durchmesser sowie zischen 300 nm und 100 µm Länge eingestellte werden. Darüber hinaus ist eine derartige Röhrenstruktur auch auf anderen Ventilmetallen und deren Legierungen herstellbar. Voraussetzung für die Herstellung bei Titan ist der Einsatz von Fluorid im Elektrolyten.
Bei der Oxidbildung findet eine Ausdehnung des Werkstoffes statt, was sich in der Entstehung von Spannungen im Werkstoff äußert. Derartige Spannungen tragen zu einer Verlängerung der Röhren bei. Die Bildung der Röhrenstruktur auf Titan wird vor allem auf die anwesenden Fluoridionen zurückgeführt, die an den Außenflächen der Röhren angelagert werden und im Kontaktbereich zum Elektrolyten in Lösung gehen. Neueren Untersuchungen zufolge gibt es zwei Arten von Oxid: das der Röhrchen und das des Zwischenbereichs. Nanostrukturiertes Titanoxid Titanoxid zeigt eine geringere Neigung zur Anhaftung von Gas. Eine Besonderheit bei Titan ist die Bildung von Magnelli-Phasen, die eine sehr gute elektrische und thermische Leitfähigkeit besitzen. Einsatzmöglichkeiten sind in der Elektrotechnik als Kondensator oder zur Erzeugung einer schaltbaren Benetzungsfähigkeit.
Schichteigenschaften – Einfluss von Wärmeeintrag
Beim Anodisieren stellte der Wärmeeintrag aufgrund hoher Stromstärken bei sich ändernden Widerständen einen wichtigen Faktor dar, der die Eigenschaften der Oberfläche beeinflusst. Zum Teil werden die Aluminiumwerkstücke beim Anodisieren so stark erwärmt, dass sogenannte Anodenbrände stattfinden können. Hierzu führte Christoph Lämmel Untersuchungen durch, die vor allem die Temperaturänderungen an der Metalloberfläche und die Strömungseffekte bei Strombelastung in den Mittelpunkt stellten.
Um eine hohe laterale Auflösung der Temperaturverteilung zu erzielen, kam eine Thermokamera zum Einsatz. Dabei zeigt sich, dass die Temperaturverteilung stark inhomogen ist. Deutlich unterschiedlich sind die Temperaturverteilungen in Abhängigkeit von der Dicke der Proben. Interessanterweise zeigt sich beim Arbeiten mit Strompulsen eine sehr schnelle Temperaturrelaxation. Um bei dieser Technik die selbe Ladung umzusetzen, werden kurzzeitig Stromdichten von etwa dem 10fachen Wert dem der Gleichstromanodisation eingesetzt. Vorteilhaft ist dabei der Effekt, dass bei Anpassung der Strompulse gleichmäßige Schichtdicken (mit etwas höheren Absolutwerten) entstehen. Interessanterweise zeigen die Röhren eine wellenförmige Wandung, deren Entstehen auf die pulsierenden Ströme zurückgeführt werden könnte. Die dabei auftretende, relativ raue Oberfläche kann durch Erhöhung der Elektrolyttemperatur verringert werden.
Wärmebehandlungszustand von Oxidschichten
Roy Morgenstern befasste sich mit dem Anodisieren von Alu-Cu-Mg Legierungen und dem Einfluss der Wärmebehandlung zur Veränderung der Schichteigenschaften. Um die Ausscheidungen von Kupfer an den Korngrenzen zu vermeiden, wird bei dieser Legierung auf etwa 800 °C erwärmt und abgeschreckt. Die anschließende Auslagerung führt zur Clusterbildung von Kupfer und Magnesium, wobei die Ausscheidung vor allem an Versetzungen stattfinden und so die Bewegung der Versetzungen hindert. Neben diesem als T4 bezeichneten Aushärtezustand wird durch eine Warmauslagerung nach dem Abschrecken der Zustand höchster Festigkeit (Benennung T6) erzielt. Eine weitere Auslagerung (Überalterung T7) führt zum Anwachsen von Al2CuMg-Phasen und Ausscheidungen an den Korngrenzen bei zunehmender Verarmung an Kupferatomen im Bereich der Phasen.
Wie die Untersuchungen zeigen, bilden sich beim Anodisieren Kupferanreicherungen an den Korngrenzen in Form von Nanopartikeln und Mikroausscheidungen. Im Falle von Kupfer entsteht elektronenleitendes Kupferoxid in der Matrix aus Aluminiumoxid. In den durchgeführten Untersuchungen konnt der Übergang von Nanopartikeln zu größeren Partikeln nachgewiesen werden.
In technischen Legierungen liegen stets intermetallische Phasen mit Eisen, Mangan und Kupfer in der Größe von einigen Mikrometern vor. Nanoskalige Ausscheidungen sind kaum erkennbar, allerdings sind im Zustand T6 und T7 längliche Ausscheidungen zu finden, die eine netzwerkartige Struktur bilden bei gleichzeitig abnehmender Porosität. Die aus diesen Legierungen hergestellten Oxidschichten sind durch eine steigende Schichtdicke sowie eine über die Schicht nach innen abnehmende Schichthärte gekennzeichnet. Die Wärmebehandlung beeinflusst die Härte der Schicht sowie die Stromausbeute der Schichtbildung dahingehend, dass die Ausscheidung sowohl die Stromausbeute und die Schichtdicke erhöht, als auch Schichthärte.
Plasmaelektrolytische Oxidation
Mikhail Zheludkevich befasst sich mit der Plasmaoxidation zur Herstellung von Schichten auf Aluminium und Magnesium. Die Oxidbildung findet bei Spannungen von mehr als 300 V statt, bei der aufgrund von Funken Plasmakanäle entstehen und aufgrund deren die Oxide und das Grundmaterial lokal aufschmelzen. Insbesondere sind hierbei Partikel aus Siliziumoxid interessant, die bei etwa 1600 °C schmelzen und Größen im Nanometerbereich aufweisen. Für die Untersuchungen wurde ein Elektrolyt auf Basis von Kaliumhydroxid und Natriumphosphat verwendet, dem Siliziumoxidpartikel mit Durchmessern von etwa 12 nm sowie im Mikrometerbereich zugesetzt wurden. Die Anodisation wurde mit Pulsstrom durchgeführt und einer Arbeitsspannung von 450 V beziehungsweise einer konstanten Stromdichte von etwa 2,5 A/dm2 durchgeführt. Bereits der Stromverlauf beim Anodisieren lässt darauf schließen, dass die Schichten durch die anwesenden Partikel dicker oder dichter sind. Des Weiteren beeinflusst die Pulsfrequenz die Porengröße, die wiederum die Einlagerung von Partikeln beeinflussen.
Es zeigt sich, dass die Siliziumoxidpartikel während der Abscheidung, vermutlich durch den Entladungsprozess, reagieren und dann in unterschiedlichen Größen und Zuständen in die Oberfläche eingelagert werden. Ein deutlicher Unterschied ist zwischen Nano- und Mikropartikeln festzustellen: Nanopartikel sind in höherer Konzentration sehr gleichmäßig über die Schicht verteilt, wogegen die Mikropartikel punktuell in geringerer Gesamtkonzentration zu finden sind. Eine Erklärung könnte in der erforderlichen Energie zum Aufschmelzen der Partikel liegen: diese ist für kleine Partikel geringer. Die auftretenden teilweise sehr großen Poren stellen nach Aussage des Vortragenden einen guten Haftgrund beispielsweise für Imprägnierungen dar.
Neben Siliziumoxid wurde auch mit Titanoxid gearbeitet, um beispielsweise photokatalytische Eigenschaften zu erzielen.
Ematal – Alternative zur Hartanodisation
Wie Marc Pfenninger erläuterte, wird beim Ematal-Verfahren mit einem Oxalatelektrolyten mit Kalium-Titan-Oxalat sowie Zusätzen an Borsäure und Zitronensäure gearbeitet. Die Elektrolyttemperatur liegt zwischen 25 und 70 °C und die Arbeitsspannungen bei über 100 V. Das Verfahren eignet sich nicht für die Herstellung von dicken Schichten. Ematal ist ein Nischenverfahren mit anspruchsvollen Elektrolyten und Randbedingungen. Übliche Schichtdicken liegen zwischen 12 und 18 Mikrometer, währen diese Werte beim konventionellen Hartanodisieren zwischen 25 und 30 Mikrometer betragen. Der Scheinleitwert als Hilfsgröße für die Korrosionsbeständigkeit ist beim Ematalverfahren im Schnitt gleichwertig oder besser. Die Verschleißbeständigkeit ist dagegen bei einigen Legierungstypen schlechter. Die Durchschlagspannungen liegen bei Ematal wesentlich besser als bei Hartanodisierschichten (normiert auf 1 Mikrometer). Die Rauheiten sind geringer als bei konventionellen Hartoxidschichten. Die Härten übertreffen die des konventionellen Anodisierens, wobei diese wie üblich von außen nach innen abnimmt. Die Porenstruktur ist bei Ematal nicht sehr ausgeprägt. Allerdings ist das Verfahren aufwendig zu bedienen, was zu höheren Herstellkosten führt, so dass auch in Zukunft vor allem Spezialprodukte damit beschichtet werden.
Temperaturmessung bei der Plasmaanodisation
Mit der Temperaturmessung bei der Plasmaoxidation befasst sich eine IKTS-Arbeitsgruppe um Karsten Voigt. Gemessen wurde mittels Thermoelement auf der Rückseite eines Versuchsbleches. Die Messungen wurden auf die übertragene Ladungsmenge normiert.
Die Untersuchungen zeigten, dass das Zünden des Plasmas stark von der angewandten Stromdichte abhängig ist. Bei derartigen Messungen ist zu berücksichtigen, dass die Wärmefluss sowohl in Richtung des Elektrolyten als auch des Aluminiummetalls erfolgt. Erstaunlicherweise steigt die Temperatur im Metall sehr schnell an und sinkt anschließend auf einen für den Prozess annähernd konstanten Wert ab.
Je nach angewandter Stromdichte unterscheidet sich die Morphologie der Oxidoberfläche: bei Werten von 18 mA/cm2 ist diese relativ glatt und bei 75 mA/cm2 porös und rau. Die rauere Oberfläche zeigt zudem einen ungleichmäßigeren Dickenverlauf.
Herstellung von Aluminiumoxidfasern
Für Werkstoffe in Flugzeugen mit Schutz gegen Brandförderung werden Aluminiumoxidfasern benötigt, mit deren Herstellung sich Katarina Chernyakova befasst. Die von ihr untersuchte Verfahrenstechnik basiert auf der Erzeugung einer stark porösen Oxidschicht und anschließendem vereinzeln der Oxidbereiche. Dazu wird Aluminium in einem zweistufiger Prozess zunächst in Oxalsäure anodisiert und dann in Natronlauge geätzt.. Eine Alternative ist das Anodisieren in Phosphorsäure, wobei das erste Verfahren Prozesszeiten von 10 Stunden und das zweite von 24 Stunden beansprucht. Die Untersuchungen zeigen, dass das Aussehen der Fasern von der Anodisationsspannung abhängig ist. Hergestellt werden Nanofasern mit Durchmesser 50 nm und Längen von 60 Mikrometer. Die Faser entstehen durch Aufweiten der Poren, so dass am Ende nur noch die Zwischenwände verbleiben, die vereinzelt werden.
Anodisieren von Tantal-Hochvoltpulvern
Tantalkondensatoren sind wichtige Bausteine von elektronischen Baugruppen. Dazu kommen Pulver zum Einsatz die vor allem durch eine hohe Reinheit und gleichmäßige Struktur gekennzeichnet sind, wie Marcel Hagymasi in seinen Ausführungen betonte. Entscheidend für Kondensatoren ist, dass die verwendeten Pulver sehr hohe Oberflächen aufweisen, da diese für die gespeicherte elektrische Ladung maßgeblich ist. Die Pulver werden so verpresst, dass sehr hohe Oberflächen verbleiben, aber ein ausreichende Stabilität des Presslings gewährleistet ist. Durch Anodisation wird auf das Tantal eine Oxidschicht aufgebracht. Dies stellt das Dielektrikum des Kondensators dar, während als Gegenelektrode unterschiedliche Elektrolyten verwendet werden. Tantalkondensatoren zeichnen sich durch eine sehr hohe Volumeneffizienz aus.
Die Anforderungen an das Pulver bezüglich der Reinheit liegen in der Regel im ppm-Bereich für Begleitstoffe. Anwendungen für den Hochvolteinsatz sind z.B. SSD-Platten, Medizintechnik und vor allem jede Art von Transportgeräten. Alle diese Bereiche fordern eine hohe Zuverlässigkeit der elektronischen Bauteile. Die Anwendungsspannungen liegen im Bereich zwischen 100 und etwa 170 V. Gesteuert wird dies durch die Partikelgröße, die zugleich eine hohe Homogenität besitzen muss. Zur Erzielung hoher Kapazitäten ist es notwendig, eine möglichst gute Kontaktierung zwischen den einzelnen Partikeln zu erreichen und zugleich eine hohe Oxidschichtdicke unter Beibehaltung der Fläche zu gewährleisten.
Kritisch für die Pulverentwicklung ist das beschränkte Wissen (oftmals aus Gründen der Betriebsgeheimnisse der Hersteller) über die Funktion zu den Herstellverfahren der Kondensatoren. Problematisch ist beispielsweise die Formierung (Oxidschichtherstellung), da die tatsächliche Oberfläche nicht bekannt und konstant ist und zudem während des Formierens sich die tatsächliche Oberfläche ändert.
Für die Kathode wird bis etwa 100 V ein Elektrolyt auf Wasserbasis verwendet und bei höheren Arbeitsspannungen kommt Glykol zum Einsatz. Ein weiterer Punkt ist die Geschwindigkeit der Formierung, da beispielsweise bei schnellem Formieren eine Gasentwicklung auftritt, die zu Durchschlägen führen kann. Die Zerstörung des Materials wird nach Untersuchungen der Pulverhersteller auf drei Auslöser zurückgeführt: Änderung des Oxideigenschaften, lokaler Durchbruch des Oxids sowie lokale totale Zerstörung.
Anodisieren von Aluminium für Membranen
Die poröse Struktur von Aluminiumoxid eignet sich zur Herstellung von Membranen mit definierten Poren. Javier Garcia Fernandes befasst sich mit der Herstellung derartiger Membranen unter Anwendung des Hartanodisierens mittels Pulsströmen. Je nach verwendetem Elektrolyten reicht der Porenanteil von 12 % (Oxalsäure) bis 18 % (Phosphorsäure). Die Porenform kann darüber hinaus vom Strom-/Spannungsverlauf beeinflusst werden. Durch Beschichtung des porösen Aluminiumoxids mit Aluminium unter Anwendung der ALD-Technik lassen sich beispielsweise Superkondensatoren herstellen.
Wird bei einem Aluminiumsubstrat mit porösem Aluminiumoxid des Substrat entfernt und beispielsweise durch einen geschlossenen Goldfilm ersetzt, kann dieser durch die Poren hindurch mit säulenartigen Goldstrukturen aufgebaut werden. Durch anschließendes chemisches Entfernen des Aluminiumoxids entsteht Goldnanodrähte in geometrischer Form der Poren. Dabei ist es auch möglich, während des Aufbaus der Nanodrähte den Werkstoff zu wechseln, beispielsweise zu Kobalt-Nickel. Daraus lassen sich dann Nanodrähte aus mehreren Werkstoffen herstellen.
Anodisieren – mehr als nur Oberflächenschutz
Das vom IKTS unter der Leitung von Dr. Schneider veranstaltete Symposium zeigte in beeindruckender Weise, dass Aluminiumoxid mehr als nur ein vorzüglicher Schutz von Aluminiumteilen ist. Die interessante Anwendung der Porenstruktur als Membranen oder Formwerkzeug für Nanodrähte stellten hier interessante Beispiele dar, die sicher in Zukunft noch durch neue Einsatzmöglichkeiten erweitert werden.
Aber auch die Weiterentwicklung des Plasmaanodisierens machen klar, dass die elektrochemische Verfahrenstechnik des Anodisierens noch durchaus Potenzial für Verbesserungen bietet. Das IKTS ist hier neben dem Kerngebiet des Fraunhofer-Instituts der Keramiktechnologie in Dresden eine exzellente Anlaufstelle für die Weiterentwicklung des Anodisierens von Aluminium und den weiteren Ventilmetallen wie Titan oder Tantal eine gute Adresse.
- www.ikts.fraunhofer.de
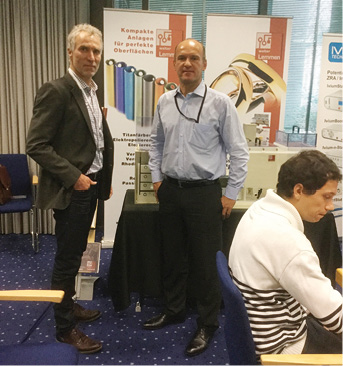
Unternehmen wie die Walter Lemmen GmbH bereicherten die Veranstaltung durch die Vorstellung ihrer Produkte und Verfahren
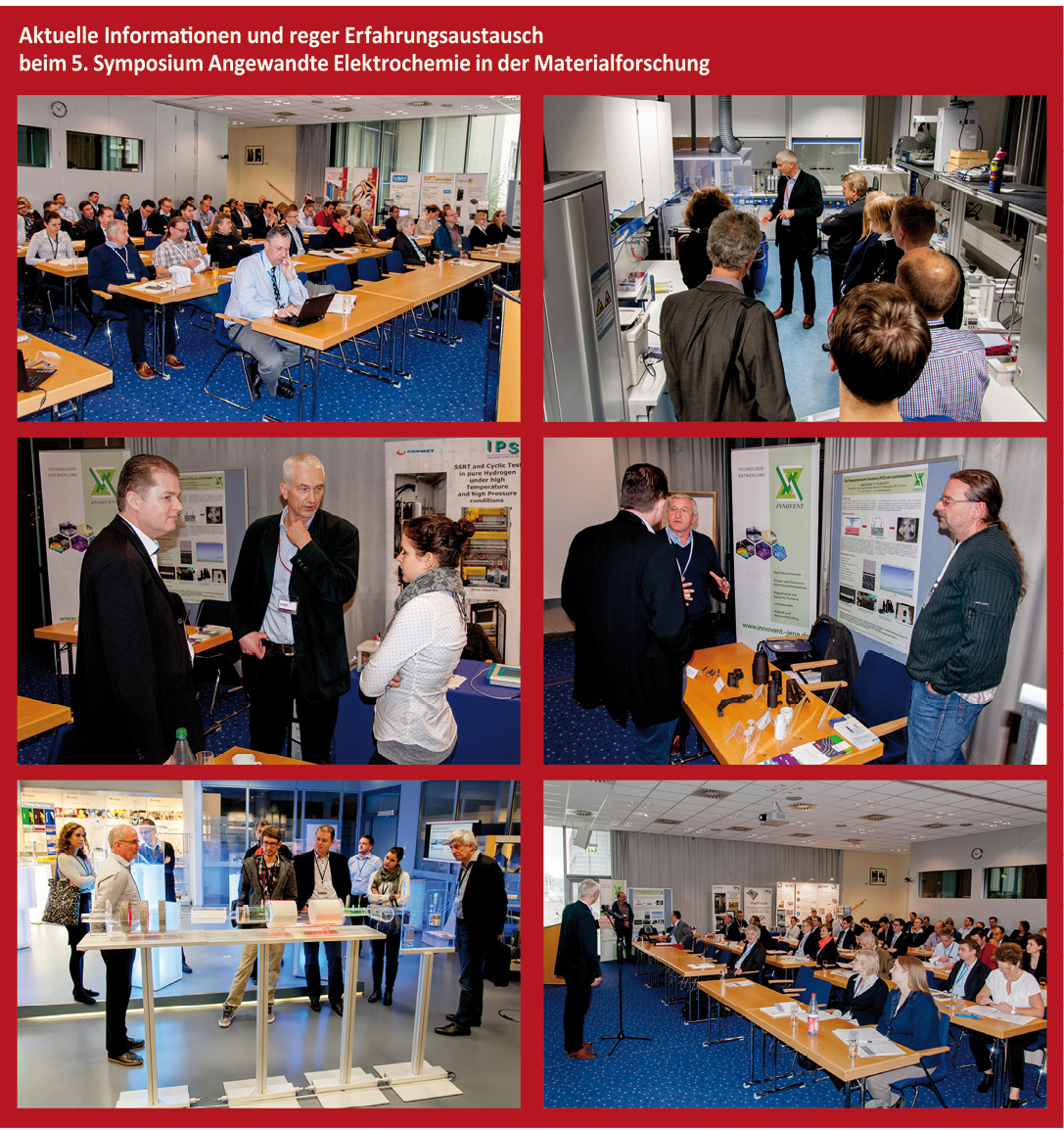