Bauteile für Automobile und Maschinen werden häufig in mehreren Massivumformschritten hergestellt. Dabei können die Werkstoffe bis an die Grenze ihrer Verformbarkeit belastet werden und unsichtbare Schäden auftreten, die wichtig für die Lebensdauervorhersage eines Bauteils sind. Bisher gebräuchliche Computersimulationen zur Auslegung eines Bauteils können die Schädigungsentwicklung in mehrstufigen Prozessen nicht immer präzise genug berechnen, um Ort und Zeitpunkt eines Materialversagens vorherzusagen. Dies leistet nun ein neues Simulationsmodell, das am Fraunhofer-Institut für Werkstoffmechanik IWM in Freiburg entwickelt wurde.
Mit diesem Simulationstool, das die tatsächlichen Schädigungs- und Versagensmechanismen in metallischen Werkstoffen abbildet, können Massivumformunternehmen die Kosten bei Prozessauslegungen reduzieren und Entwicklungszeiten verkürzen. Zudem sind komplexere Bauteilgeometrien als bisher zu realisieren, die ohne die neue und präzisere Simulation nur sehr aufwändig verwirklicht werden könnten.
Schädigungsmodell für viele Werkstoffe einsetzbar
Das neue Verfahren wurde modular aufgebaut, damit es flexibel auf die große Anzahl der Werkstoffe einsetzbar ist, wie Dr. Maksim Zapara, Leiter des Teams Massivumformung der Gruppe Umformprozesse am Fraunhofer IWM, die Technologie erklärt. Das Modell beschreibt, unter welchen Voraussetzungen sich bei der plastischen Verformung des Werkstoffs Poren bilden, unter welchen Bedingungen sie wachsen oder sich mehrere Poren zusammenschließen. Aus diesen Zusammenschlüssen können Makroporen, dann Mikrorisse und letztlich ein kritischer Makroriss entstehen. Je nach Materialzustand bestehen bereits im Gefüge des Ausgangswerkstoffs Poren, beim Umformen nimmt dann die plastische Deformation zu und es entstehen zusätzliche Poren an Einschlussteilchen und an Korngrenzen des Metalls, so Zapara. Bisher gaben die Standardsimulationen lediglich eine Hilfestellung im Entscheidungsprozess für die Auslegung von Bauteilen ab: Das Expertenwissen war hierbei der wichtigste Faktor. Größere Vorhersagegenauigkeit liefern jedoch die so genannten mechanismenbasierten Schädigungsmodelle. Für Prozesse bei der Kaltmassivumformung wurde im Rahmen eines IGF-Projekts das bekannte mechanismenbasierte Materialmodell nach Gurson, Tvergaard und Needleman, oder GTN-Modell, so erweitert, dass es beobachtete Mechanismen der duktilen Schädigung für die relevanten Materialien genauer abbildet als bisher. Bei der duktilen Schädigung ist ein Material so stark belastet, dass es sich plastisch verformt und seine Mikrostruktur sich verändert. Bei Überbeanspruchung kann das Material brechen.
Neue Erkenntnisse zum Werkstoffverhalten bei hoher Dehnung und Druck
Als Grundlage für das neue Materialmodell wurden die physikalischen Ursachen für das Werkstoffverhalten in Kaltmassivumformprozessen am Fraunhofer IWM systematisch erforscht. In umfangreichen
Mikrostrukturuntersuchungen fanden die Forscherinnen und Forscher beispielsweise heraus, dass sich bei der Umformung Poren insbesondere an nichtmetallischen Einschlussteilchen im Material bilden: Entweder zerbricht das Teilchen oder es löst sich vom umgebenden Material ab. Entgegen der bisherigen Meinung, dass sich Poren schließen, wenn das Material hohen Druckbelastungen ausgesetzt ist und damit Schädigungen quasi verschwinden, fand das Forschungsteam heraus, dass sich im Gegenteil neue Poren an Einschlussteilchen infolge von starkem Querfließen des Materials unter Druck bilden und damit größere Schädigungen entstehen können als bisher angenommen.
Modell bildet Vielzahl realer Schädigungsmechanismen ab
Die gefundenen Schädigungsmechanismen treten jedoch nicht in allen Werkstoffen gleichermaßen auf. Beispielsweise gibt es Mechanismen, die allein im Zusammenhang mit spröden Partikeln wie Mangansulfiden auftreten. Der modulare Aufbau des neuen Schädigungsmodells ermöglicht es, eine große Anzahl in der Anwendung zugänglicher Werkstoffe damit simulieren zu können: Je nach betrachtetem Werkstoff können Module an- oder abgeschaltet werden. Es beschreibt zudem die physikalischen Ursachen der Schädigungen wie Porenzusammenschlüsse, Wachstum von Poren oder Bildung von Mikrorissen.
Das neue Modell ist als Benutzer-Routine in das häufig genutzte Finite Elemente-Programm ABAQUS implementiert und kann auch in bestehenden Simulationsprogrammen für die Massivumformung umgesetzt werden. Dies ermöglicht den Umformbetrieben, ihre bestehenden Simulationstools zur Schadensvorhersage und Auslegung von Herstellungsprozessen mit der neuen Methode erweitert verwenden zu können.
Bessere Schadensvorhersage in komplexen Umformprozessen
Mit dem neuen modularen Schädigungsmodell simulierte das Forschungsteam industrielle Massivumformprozesse, bei denen in Realität bereits Bauteilschädigungen auftraten. Die industriell etablierten Simulationsansätze konnten den tatsächlichen Schadensort nach Kenntnis von Dr. Zapara nicht immer präzise genug vorhersagen. Das am Fraunhofer IWM erweiterte GTN-Modell jedoch bestimmte Ort und Zeitpunkt des Versagens korrekt vorher, zum Beispiel an einer kaltfließgepressten Getriebewelle. Werden die nach dem Herstellungsprozess bestehenden Werkstoffeigenschaften wie lokale Verfestigung oder Eigenspannungen, die nun durch das neue Modell exakter bestimmt sind, als Eingangsgrößen für Simulationen des späteren Bauteilverhaltens im Betrieb genutzt, sind auch dort genauere Simulationsaussagen möglich, beispielsweise zur Bauteillebensdauer.
- www.iwm.fraunhofer.de
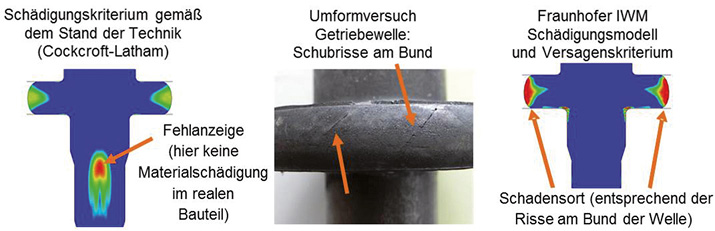

Verbesserung der Schadensvorhersage am Beispiel einer Getriebewelle: Schadensort im Umformexperiment (Mitte), inkorrekte Schadensvorhersage nach Stand der Technik (links) sowie die korrekte Schadensvorhersage (rechts) mit dem Fraunhofer IWM-Materialmodell (© Fraunhofer IWM)

Umlaufender Riss im fließgepressten Napf: reales Teil (links) und Simulation (rechts) (© Fraunhofer IWM)