Schneestrahlreinigung keramischer Sensorbauteile mit Kohlenstoffdioxid vor einer funktionellen Beschichtung
Je nach Aufgabenstellung benötigen in Fahrzeug verbaute Sensoren eine funktionelle Beschichtung, die hohe Anforderungen an die Partikelfreiheit der Oberfläche stellt. Ein renommierter Automobilzulieferer nutzt dafür ein vollautomatisiertes CO2-Schneestrahlsystem, mit dem die Reinigung im Viersekunden-Takt erfolgt.
Ob Verbrennungsmotor, Elektromobilität oder autonomes Fahren – die Funktion unterschiedlichster Komponenten wird in Fahrzeugen durch zahlreiche Sensoren überwacht, gesteuert und geregelt. Damit die Detektoren ihre Aufgabe optimal erfüllen können, erhalten viele eine Funktionsbeschichtung, deren Qualität entscheidend von der Sauberkeit der Oberfläche abhängt. Dies ist auch bei keramischen Sensorbauteilen der Fall, bei denen vor der Beschichtung feiner Schleifstaub aus einem vorgelagerten Fertigungsschritt zu entfernen ist. Da diese Verschmutzung in einem klassischen nasschemischen Prozess nicht oder nur extrem aufwändig abgereinigt werden kann, entschied sich der Hersteller, ein namhafter Automobilzulieferer, für ein quattroClean-Reinigungssystem der acp – advanced clean production GmbH. Die modular aufgebaute Reinigungslösung mit Kohlenstoffdioxidschnee lässt sich auf kleinstem Raum in vollautomatisierte, verkettete Produktionslinien integrieren und durch übergeordnete Produktionsleitsysteme steuern oder separat einsetzen.
Das für die Reinigung der Sensorbauteile konzipierte quattroClean-System ist komplett eingehaust und verfügt über ein geschlossenes Reinigungsmodul (Bildquelle: acp – advanced clean production)
Trockene, umweltneutrale Reinigung
Als Reinigungsmedium kommt flüssiges, praktisch unbegrenzt haltbares Kohlenstoffdioxid (CO2) zum Einsatz, das als Nebenprodukt bei chemischen Prozessen und der Energiegewinnung aus Biomasse entsteht und daher umweltneutral ist. Es wird aus Flaschen oder Tanks zugeführt.
Das nicht brennbare, nicht korrosive und ungiftige Kohlenstoffdioxid wird durch die verschleißfreie Zweistoff-Ringdüse des acp-Systems geleitet und entspannt beim Austritt zu feinem Schnee. Dieser wird durch einen
ringförmigen Druckluft-Mantelstrahl gebündelt und auf Überschallgeschwindigkeit beschleunigt. Beim Auftreffen des nicht abrasiven und gut fokussierbaren Schnee-Druckluftstrahls auf die zu reinigende Oberfläche kommt es zu einer Kombination aus thermischem, mechanischem, Sublimations- und Lösemitteleffekt. Durch diese vier Wirkmechanismen entfernt das quattroClean-System Schleifstaub und andere partikuläre Verunreinigungen von der gesamten Oberfläche sowie aus Sacklochbohrungen ebenso zuverlässig und reproduzierbar wie filmische Kontaminationen, beispielsweise Schmauchspuren nach einer Laserstrukturierung. Die Reinigung erfolgt materialschonend, sodass auch empfindliche und fein strukturierte Oberflächen behandelt werden können. Das quattroClean-System kann daher für praktisch alle technischen Werkstoffe und Materialkombinationen eingesetzt werden.
Maßgeschneidertes Anlagenkonzept
Um sowohl die hohen Sauberkeits- als auch die Taktzeitvorgabe von nur vier Sekunden pro Bauteil des Automobilzulieferers umzusetzen, entwickelten acp und der Automatisierungsspezialist ACI AG ein maßgeschneidertes Anlagenkonzept. Es basiert auf einem für zahlreiche Anwendungen einsetzbaren Standardmodul, in das der quattroClean-Prozess integriert ist, einem mit drei Stationen ausgestatteten Rundtakttisch sowie zwei Robotern für das Teilehandling. Durch ihre vollständig geschlossene Ausführung entspricht die in eine Fertigungsumgebung integrierte Reinigungslösung Vorgaben zur technischen Sauberkeit in vollem Umfang. Ein Augenmerk legten die Konstrukteure auch auf die gute Reinigbarkeit der Anlage, was ebenfalls einen Beitrag zur effizienten Erfüllung hoher Sauberkeitsanforderungen leistet. Darüber hinaus sorgt die effektive Geräuschdämmung für eine angenehme Arbeitsatmosphäre.
Vollautomatischer, unterbrechungsfreier Reinigungsprozess
Die Beschickung der Anlage erfolgt für einen unterbrechungsfreien Betrieb durch drei Schubladeneinheiten, in denen sich Trays mit verunreinigten Bauteilen befinden und einzeln in den Arbeitsbereich des Roboters transportiert werden. Dieser entnimmt nacheinander fünf Teile und platziert diese in eine Zentrierstation. Da die etwa zwei Zentimeter langen und rund 0,5 Zentimeter breiten Sensorkomponenten nicht am Grundkörper berührt werden dürfen, steht für das Greifen nur eine Randzone von weniger als einem Millimeter zur Verfügung. Nach dem automatischen Zentrieren positioniert ein weiteres Greiferystem alle fünf Teile gleichzeitig in Aufnahmen auf einer Station des Rundschalttisches, der sie mit einer Drehung definiert in das geschlossene Reinigungsmodul transportiert. Dort befindet sich über jeder Teileposition eine Düse, die eine festgelegte Zeit auf die während des Reinigungsprozesses rotierenden Sensorkomponenten strahlt. Die abgereinigten Verschmutzungen werden zusammen mit dem Kohlenstoffdioxid durch eine aktive Absaugung mit Abscheidefilter aus dem Reinigungsmodul entfernt.
Eine weitere Schaltung bringt die Aufnahme zur Entladeposition. Hier entnimmt der zweite Roboter die gereinigten Teile und legt sie in kundenspezifischen Trays ab, in denen sie zu den nächsten Prozessschritten transportiert werden.
Umfangreiche Prozessüberwachung und -anpassung
Für eine gleichbleibend hohe Prozessqualität werden die Düsen einzeln hinsichtlich Kohlenstoffdioxid- und Druckluftzufuhr sowie Strahlkonsistenz und -dauer überwacht und die ermittelten Werte automatisch gespeichert. Diese Parameter lassen sich ebenso wie die Rotationsgeschwindigkeit der Teile variabel einstellen und als Programme in der Anlagen- oder einer übergeordneten Steuerung hinterlegen. Diese Flexibilität ermöglicht einerseits, dass der Reinigungsprozess an unterschiedliche Verschmutzungsgrade angepasst werden kann. Andererseits können auch Reinigungsprogramme für die Entfernung von Schmauchspuren nach der Laserbearbeitung der beschichteten Teile gespeichert werden.
Die Konzentration an Kohlenstoffdioxid im Bereich des an die Fertigungsumgebung angrenzenden Ein- und Auslaufs der Anlage erfolgt entsprechend der Maschinenrichtlinie mit weltweit zertifizierten und zugelassenen Sensoren. Doris Schulz
- www.acp-micron.com
- www.aci.ag

Das für die Reinigung der Sensorbauteile konzipierte quattroClean-System ist komplett eingehaust und verfügt über ein geschlossenes Reinigungsmodul (Bildquelle: acp – advanced clean production)
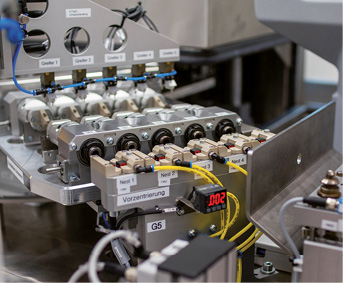

Der Roboter entnimmt die Teile einzeln aus den Trays und platziert sie in einer Zentrierstation (Bildquelle: acp – advanced clean production)
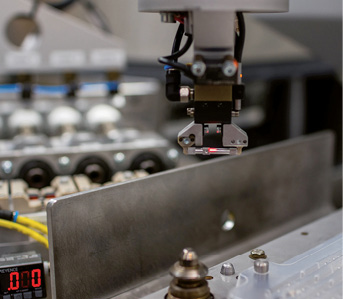
Nach der Zentrierung entnimmt ein Greifersystem alle fünf Bauteile und setzt sich positionsgerecht in die Aufnahmen für die Reinigung ein (Bildquelle: acp – advanced clean production)

Text zum Titelbild: Jedem der in den Aufnahmen platzierten und während des Reinigungsprozesses rotierenden Teile ist eine Düse zugeordnet. Sie strahlt mit definierten Parametern, die überwacht werden, auf das Werkstück (Bildquelle: acp – advanced clean production)
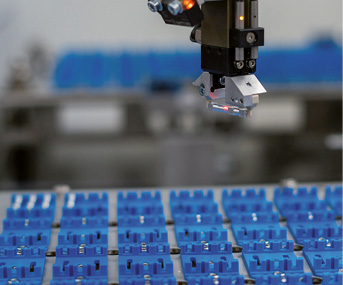
