Um Waren innerhalb der Fertigung nachzuverfolgen, setzt die Drollinger GmbH Metallveredelungswerke auf RFID-Technologie. Gekoppelt mit dem eingesetzten ERP-System können so Warenbewegungen besser nachverfolgt und Mitarbeiter gleichzeitig entlastet werden.
Die Drollinger GmbH Metallveredelungswerke in Birkenfeld glänzen mit einem breiten Verfahrensspektrum von galvanischen Beschichtungen über Edelmetall, Wärmebehandlung bis hin zu Gleitschleifen und vielem mehr. Das 1966 gegründete Unternehmen war nicht von Beginn an so breit aufgestellt. Zwischenzeitlich lag der Fokus auf Hartchrom mit wenigen Großkunden. Mit der Entscheidung ein breiteres Kundenfeld anzusprechen, kamen weitere Verfahren hinzu. So wuchs das Unternehmen im Lauf der Zeit von 30 auf 85 Mitarbeiter an und besteht heute aus vier Werken.
Dr. Grischa Drollinger, Geschäftsführer der Drollinger GmbH, legt besonderen Wert darauf, dass kleine Kunden wie große Kunden behandelt werden. Diese Vielzahl an unterschiedlichen Kunden bringen aber auch einige Herausforderungen mit sich: So werden gleichzeitig viele verschiedene Bauteile veredelt. Daraus resultiert ein hoher organisatorischer Aufwand.
Projekte mit einem ERP-Partner
Um die Unternehmensabläufe zu steuern, wird die Drollinger GmbH seit 2015 durch das ERP-System OMNITEC der Softec AG unterstützt. Dr. Drollinger ist sehr zufrieden damit: Das System ist sehr stabil. Das ist enorm wichtig für uns als Lohnveredler. Rechnungen müssen kontinuierlich versendet werden, Ausfälle sind für uns sehr negativ.
Gemeinsam mit der Softec AG geht die Drollinger GmbH in einem neuen Projekt jetzt den nächsten Schritt Richtung Digitalisierung. Bisher gingen die Betriebsaufträge nach der Erfassung in die Fertigung und es war nicht immer nachvollziehbar, in welchem der vier Werke sich die Ware gerade befindet. Das erschwerte es, Kunden Auskunft über den aktuellen Stand ihrer Ware zu geben – insbesondere, wenn es um Aussagen zu Lieferterminen ging. Das ist bei uns sozusagen wie bei einer Hotline, beschreibt Dr. Drollinger den Ablauf von Kundenanfragen. Und dazu kommt, dass Anforderungen immer weiter steigen, indem beispielsweise die Lieferzeiten immer kürzer werden sollen.
Nach einer Kundenanfrage musste sich bisher ein Mitarbeiter auf die Suche nach der Ware im Prozessablauf begeben. Das kostete Zeit und war mit einigen Laufwegen durch die vier Werke verbunden. Damit soll jetzt Schluss sein. Stattdessen sollen RFID-Transponder auf jeder Box angebracht werden und Warenbewegungen automatisch verfolgen.
RFID – alter Ansatz, neue Ideen
RFID steht für radio-frequency identification und ermöglicht es Objekte mit Radiowellen zu identifizieren und ihren Standort zu bestimmen. Um die Transponder auszulesen, werden an den Eingängen der Werke Antennen angebracht, die an ein RFID-Lesegerät gekoppelt sind. Damit kann nachvollzogen werden, wann ein bestimmter Transponder die Antennen passiert hat. Immer zwei Antennen werden als sogenanntes Gate in den Ein- und Ausgängen der Werke angebracht. Pro Werk entstehen so zwei Gates. Über die Reihenfolge, in der ein Transponder die Gates passiert, wird erkannt, ob eine Ware sich aus einem Werk hinaus oder in ein Werk hinein bewegt.
Die RFID-Transponder werden auf Plastikklammern angebracht und machen damit jede Box nachverfolgbar
An sich handelt es sich dabei um keinen neuen Ansatz. Bei Drollinger wurde auch schon vor einigen Jahren mit RFIDs experimentiert. Allerdings scheiterten bisherige Versuche daran, dass es nicht möglich war auf einer Palette einzelne Boxen zu tracken. Ein weiterer einschränkender Faktor sind die transportierten Metallteile in den Boxen. Das Metall wirkt als Störfaktor und verhindert, dass die Transponder zuverlässig gelesen werden können.
Gelöst wird dies über RFID-Transponder, die auf Plastikklammern angebracht werden. Diese wiederum hängen an den einzelnen Boxen und haben somit genügend Abstand zum Metall. Gleichzeitig kann so jede Box als Transporteinheit einzeln verfolgt werden.
Über eine Schnittstelle werden diese Informationen an das ERP-System weitergegeben. Hier ist außerdem hinterlegt, welcher Transponder zu welchem Betriebsauftrag gehört. Wird nun ein bestimmter Transponder abgefragt, liefert die Schnittstelle die passenden Daten aus dem ERP-System. So kann für jeden Auftrag das Bewegungsprofil nachverfolgt werden. Dort werden alle Standpunkte mit Uhrzeit aufgelistet, sodass direkt festgestellt werden kann, in welchem Werk sich die Ware befindet.
Die richtige Ausrichtung ist wichtig: Zwei Antennen bilden ein Gate und müssen gemeinsam den Bereich abdecken, durch den die Waren transportiert werden
In jedem Werk sind die Antennen mit einem Lesegerät verbunden, in dem die Daten gesammelt und weiterverarbeitet werden
Ausblick
Insgesamt erhofft sich Dr. Drollinger, durch die Bewegungsprofile einen besseren Überblick zu bekommen. Nach seiner Überzeugung kann das Unternehmen dadurch belastungsfähige Aussagen treffen. Über den genauen Kenntnisstand wo und in welchem Bearbeitungsschritt sich die Ware befindet, kann eine realistischere Abschätzung zu Lieferterminen getroffen werden. Denn ohne diese Informationen werden tendenziell längere Zeiträume angegeben. Für Mitarbeiter stellt das System eine große Entlastung dar. Durch die genauere Standortbestimmung wird viel Zeit bei der Abklärung des Bearbeitungszustands der Waren eingespart. Da das System automatisch – beim Vorbeifahren an den Gates – funktioniert, fallen auch keine neuen Arbeitsschritte oder zusätzliche Aufgaben für die Mitarbeiter an. Die Warenverfolgung läuft im Hintergrund ab.
Nach der erfolgreichen Implementierung der RFID-Gates für die einzelnen Werke gibt es bereits Pläne, das System nach und nach auszuweiten. So könnten beispielsweise zusätzlich an einzelnen Anlagen Gates angebracht werden, um noch genauere Aussagen über den Aufenthaltsort von Waren erhalten zu können.
- www.softec.de
- www.drollinger.com
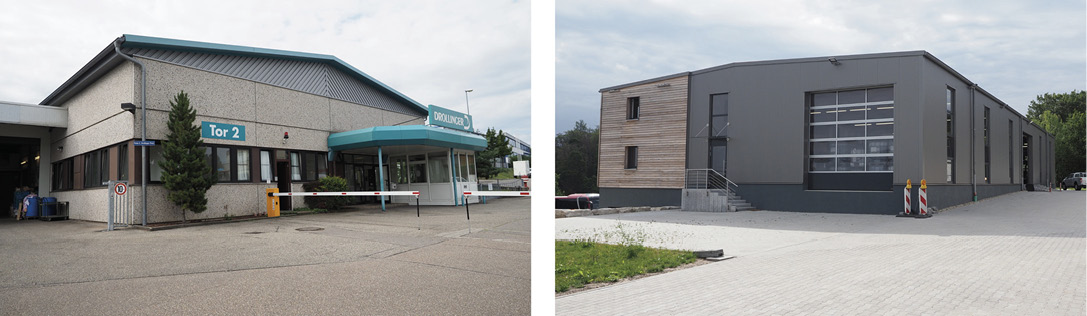

Stammgebäude der Drollinger GmbH Metallveredelungswerke in Birkenfeld (links); Erst vor kurzem wurde ein viertes Werk errichtet, das den Betrieb um 1850 m2 und eine neue Galvanikanlage erweitert