Präzisionsdreh- und -frästeile für anspruchsvolle Branchen sind die Spezialität der Mattig Präzision GmbH. Um die geforderte hohe Qualität liefern zu können, setzt das Unternehmen auf eine hochqualifizierte Belegschaft und einen modernen Maschinenpark, der seit Mitte 2019 auch eine innovative Vollvakuumreinigungsanlage R1 der Pero AG beinhaltet. Sie zeichnet sich unter anderem durch höchste Produktivität und Zuverlässigkeit aus.
Anspruchsvolle Player im Motorsport setzen ebenso auf präzise Bauteile und Bauteilgruppen von Mattig Präzision im österreichischen Obertrum, wie Unternehmen der Uhrenindustrie und Medizintechnik. Denn neben Qualität und Zuverlässigkeit zeichnen sich die Fertigungsspezialisten durch Flexibilität und Vielseitigkeit aus, wie Geschäftsführer Roman Gratzer hervorhebt: Durch das umfangreiche Know-how unserer Mitarbeiter sind wir in der Lage, bereits bei der Entwicklung von Prototypen zu unterstützen. Das heißt, wir sind meist schon weit vor der ersten Serienfertigung mit unseren Kunden im Gespräch und beraten im Hinblick auf optimale Machbarkeit.
Ist die Serie freigegeben, fertigt Mattig zeitnah und mit einer hohen Präzision von bis zu 1 µm bis 2 µm Toleranzbreiten. Meist sind mittlere Losgrößen von bis zu 5000 Stück pro Jahr gefragt, gelegentlich stellt der Fertigungsbetrieb aber auch 20 000 oder in Einzelfällen gar bis zu 200 000 Bauteile pro Jahr her. Dabei zerspanen die Österreicher nahezu jedes Material – HSS und Titan ebenso wie Messing oder Kunststoffe, um nur ein paar wenige aufzuzählen.
Danach durchlaufen die meisten anspruchsvollen Bauteile die Reinigungsanlage Pero R1, um nach höchsten Standards gereinigt und teils konserviert oder anschließend beschichtet und/oder zu Baugruppen montiert zu werden. Nicht zuletzt dank dieser großen Angebotsbandbreite gelingt es dem Unternehmen regelmäßig, Kostenpotenziale für seine Kunden zu erschließen.
Zudem weißt Gratzer darauf hin, dass sein Betrieb seit einigen Jahren in der Lage ist, hundertprozentige Rückverfolgbarkeit zu gewährleisten. Der Ingenieur erklärt dazu: Wir können von jedem einzelnen Bauteil alles nachvollziehen – vom Ausgangsmaterial über das durchlaufene Bearbeitungszentrum, die Prüf- und Messmaschinen sowie die Reinigungsanlage bis hin zu den beteiligten Mitarbeitern. Für unsere anspruchsvollen Branchen ist das ein nicht zu unterschätzender Faktor.
In der Fertigung von Mattig stehen hochmoderne Dreh-Fräszentren. Die dort hergestellten Bauteile – wie der abgebildete Präzisionsdichtring – kommen unter anderem im Motorsport zum Einsatz (Bilder: Pero AG)
Von Mattig Präzision hergestellte Bauteile kommen in vielen Bereichen zum Einsatz – neben Motorsport und Automotive auch in der Medizintechnik und in Uhren (Bilder: Mattig Präzision GmbH)
TCO entscheidet über Anschaffung von Maschinen und Anlagen
Neben höchster Zuverlässigkeit und Präzision setzt der Präzisionsfertiger vor allem auf hohe Produktivität. Dementsprechend investiert Produktionsleiter Peter Klinger selten in die billigste Lösung. Die Anschaffungskosten sind nach seiner Aussage natürlich nicht unerheblich, aber letztlich nur ein Faktor der von Mattig erstellten Lastenhefte zur Anschaffung von Maschinen und Anlagen. Genauso wichtig seien Dinge wie Durchsatz, Zuverlässigkeit, Flexibilität und vieles mehr. Letztlich stellen wir eine zu erwartende Total Cost of Ownership auf, die uns als wichtige Entscheidungsbasis dient, so Peter Klinger.
So war auch die Anschaffung der jüngsten Reinigungsanlage wohl überlegt. Referenzkunden haben den Maschinenbau- und Mechatronikmeister auf die Reinigungsspezialisten von Pero aus Königsbrunn bei Augsburg aufmerksam gemacht, so dass Peter Klinger gemeinsam mit Fertigungsgruppenleiter Gerold Pertiller auf der Fachmesse parts2clean im Oktober 2018 einen ersten Kontakt herstellte. Die aktuellen Bedarfe wurden erläutert und intensive Gespräche geführt. Ähnlich gingen Klinger und Pertiller bei anderen Anbietern vor.
Die Chemie stimmt! Das betonen die Fach- und Führungskräfte von Mattig und Pero gleichermaßen (v.l.n.r.): Fertigungsgruppenleiter Gerold Pertiller, Geschäftsführer Roman Gratzer, Vertriebsingenieur Josef Deutsch und Produktionsleiter Peter Klinger (Bild: Pero AG)
Die automatische Wartung von Reinigungsmedium, Destille und Filter erleichtert den Umgang mit der Pero R1 (Bild: Pero AG)
Auf Basis diverser Vergleichsdaten gab es eine erste Selektion und bereits wenige Wochen später bekamen die verbliebenen potenziellen Lieferanten Bauteile zur Probereinigung. Kurz danach – im Februar 2019 – stand die Entscheidung fest: Eine speziell konfigurierte Pero R1 wurde im Juni 2019 installiert, und die Pero AG ist künftig unser bevorzugter Reinigungspartner, stellt Peter Klinger fest.
Viermal kürzere Taktzeiten, achtmal produktiver
Die Gründe sind facettenreich. Ganz allgemein äußern sich Geschäfts- und Produktionsleitung sowie die beteiligten Mitarbeiter sehr positiv über die Chemie. Wie Peter Klinger betont, war das Verhältnis zu Pero-Vertriebsingenieur Josef Deutsch und allen andern Pero-Kollegen von Anfang an sehr angenehm. Dabei schätzen wir die menschliche Komponente ebenso wie die fachliche Kompetenz. So bekommen wir von den Königsbrunner Kollegen beispielsweise stets schnell und unkompliziert gute Tipps, wenn neue, komplexe Teile zu reinigen sind. Das klappe reibungslos.
Als ebenso wichtig bezeichnet Gerold Pertiller die spezifische Leistungsfähigkeit der Pero R1. Ihm zufolge könnten jetzt manche Bauteile bis zu achtmal produktiver gereinigt werden, als das mit der vorherigen Lösung möglich gewesen sei. Entscheidend für die enorme Steigerung sind mehrere Faktoren. Unter anderem erzielt die neue Anlage rund viermal kürzere Taktzeiten bei reproduzierbaren Reinigungsergebnissen.
Darüber hinaus nennt er die Teilekonservierung in einem Arbeitsgang extrem effizient. Die Anlage dosiert hierbei sogar das Öl im Konservierungsbad automatisch. Früher erledigte diese gesamte Aufgabe ein Mitarbeiter manuell. Er bereitete das Reinigungsmedium auf und tauchte die Teile von Hand. Das dauerte relativ lange, war unangenehm und weder wirtschaftlich noch umweltfreundlich. Die eingesparte Zeit nutzen meine Kollegen jetzt sinnvoll fürs Verpacken und andere Aufgaben, freut sich der Fertigungsgruppenleiter.
Als weiteren Vorteil nennt Produktionsleiter Peter Klinger die Vielseitigkeit der neuen Reinigungsanlage, die für das gesamte Spektrum der spanhebenden und spanlosen Metallverarbeitung ebenso ausgelegt ist wie für Werkstücke aus Kunststoff, Keramik oder Glas. Alles wird bedarfsgerecht unter Vollvakuum als Schüttgut, gesetzte Ware oder Einzelteil effizient gereinigt.
![]() |
![]() |
Nach dem Einlesen eines Barcodes zur Programmzuordnung, stellt die Produktionsmitarbeiterin Stanojka Tadic von Mattig ihre Bauteilkörbe zweireihig auf die Zuführung und startet den Reinigungsvorgang in der Pero R1 am Touch Panel (Bilder: Pero AG)
![]() |
![]() |
Wenn Bauteile von Mattig die Pero R1 verlassen, erfüllen sie eine hohe Technische Sauberkeit. Dies wird durch die Prozesskombinationen aus Reinigen, Spülen, Dampfentfetten und optionaler Ultraschallreinigung erreicht. Von Vorteil ist zudem die Möglichkeit, in einem Arbeitsgang zu konservieren (Bilder: Pero AG)
Vollautomatisch erfolgt die Zu- und Ausführung der Bauteile in den Arbeitsraum der unter Vollvakuum arbeitenden lösemittelbasierten Reinigungsanlage Pero R1 (Bild: Pero AG)
Geschäftsführer Roman Gratzer und Produktionsleiter Peter Klinger (beide Mattig Präzision) sind mit dem Reinigungsergebnis ihrer Pero-Anlage sehr zufrieden (Bild: Pero AG)
Destillierleistung von 140 Liter pro Stunde
Als Lösemittel kommt in der Pero R1 modifizierter Alkohol zum Einsatz, der durch integrierte Hauptstromfilter, permanente Destillation sowie intelligente Wartungsprogramme automatisch gepflegt wird. Mit einer Destillierleistung von 140 Liter pro Stunde, in der die Reinigungsmedien regeneriert werden, kann die Anlage enorm hohe Durchsätze bewältigen. Pero-Vertriebsingenieur Josef Deutsch ist überzeugt, dass das in dieser Anlagenkategorie absolute Benchmark-Werte am Markt sind.
So reinigt die Anlage stets zuverlässig und erreicht sehr hohe Anforderungen, die als Technische Sauberkeit definiert werden. Das bedeutet, es verbleiben bei Bedarf nur Partikel mit einer maximalen Größe von zirka 100 µm bis 200 µm. Für Mattig sind diese Möglichkeiten insbesondere auch für Kunden aus der reinheitssensiblen Medizintechnik wichtig.
Der Betrieb unter Vollvakuum schont darüber hinaus das Reinigungsmedium und senkt den Lösemittelverbrauch auf ein Minimum. Nach Aussage von Peter Klinger musste bislang jedes Jahr das Lösemittel einmal komplett ausgetauscht werden. Jetzt wird der modifizierte Alkohol gelegentlich überprüft und gegebenenfalls durch chemische Zugaben stabilisiert. Aber selbst das sei lediglich in Abständen von mehr als einem Jahr notwendig, so Peter Klinger.
Als hilfreich bezeichnet Geschäftsführer Roman Gratzer auch die hohe Bedienerfreundlichkeit, die Pero durch ein Touch Panel bietet. Übersichtlich und strukturiert sind alle relevanten Werte und Funktionen auf einen Blick zu erfassen. Der Mitarbeiter muss lediglich einen Barcode einlesen, damit die Programmzuordnung passt. Dann stellt er die zweireihig einführbaren Bauteilkörbe auf die Zuführung und startet den Vorgang am Panel. Zu- und Ausführung der Bauteile erfolgen dann vollautomatisch.
Über die Mattig Präzision GmbH
Die Mattig Präzision GmbH mit Sitz in Obertrum am See, Österreich, wurde 1995 gegründet und hat im Jahr 2019 mit rund 60 Mitarbeitern einen Umsatz von 9,5 Millionen Euro erwirtschaftet. Als leistungsfähiger und flexibler Partner stellt Mattig anspruchsvolle Präzisions-Dreh-Frästeile in hoher Qualität her und liefert diese in kleinen und mittleren Serien primär an Unternehmen aus den Bereichen Motorsport, Automotive, Marine und Bahn, Uhren/Schmuck sowie Medizintechnik und Sportgeräte. Neben der präzisen spanenden Herstellung, Reinigung und der Konservierung von Bauteilen übernimmt der Fertigungsbetrieb bei Bedarf auch die Baugruppenmontage und unterstützt bei der Entwicklung von Prototypen.
- www.mattig.com
Über die PERO AG
Pero wurde 1953 von Peter Erbel gegründet; das Unternehmen hat seinen Hauptsitz in Königsbrunn bei Augsburg und erwirtschaftet heute mit rund 200 Mitarbeitern einen Umsatz von etwa 30 Millionen Euro. Das Unternehmen stellt modular aufgebaute, leistungsstarke Teilereinigungsanlagen für den industriellen Einsatz her, die auf Basis von Lösemitteln oder wässrigen Medien arbeiten. Sie entölen, entfetten und reinigen Werkstücke verschiedenster Art und sorgen bei Bedarf für gleichmäßigen Korrosionsschutz. Neben hochwertiger Technik zeichnet sich Pero durch eine umfangreiche Beratung und Prozessbegleitung ebenso aus wie durch einen qualifizierten Service.
- www.pero.ag


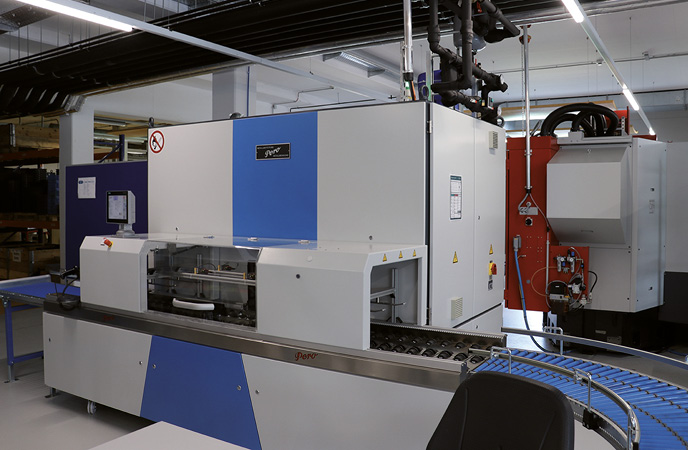